The influence of magnesium oxide on alumina ceramics
1. The influence of magnesium oxide on the sintering temperature and densification of alumina ceramics
First of all, magnesium oxide, as a common sintering aid, can effectively reduce the sintering temperature of alumina ceramics. Using high-purity a-Al2O3 powder as raw material and magnesium oxide as sintering aid, alumina ceramics were prepared by spark plasma sintering (SPS). The effects of magnesium oxide addition and sintering temperature on the densification process and microstructure of alumina ceramics were studied, and the diffusion and evolution of pores during sintering were analyzed. The results show that adding an appropriate amount of magnesium oxide can reduce the sintering temperature of alumina ceramics, inhibit grain growth, and improve density. 0.25% (mass fraction) is the optimal addition of magnesium oxide.
2. The influence of magnesium oxide on the mechanical properties and grain growth of alumina ceramics
Alumina ceramics were prepared by using alumina powder as raw material, magnesium oxide as additive, and two-step sintering process, and the influence of changes in additives on the density, mechanical properties and microstructure of alumina ceramics were analyzed.
The study found that with the increase of magnesium oxide addition, the relative density, bending strength and hardness of alumina ceramic sintered samples showed a trend of first increasing and then slightly decreasing. When the magnesium oxide content is lower than the solid solubility limit, Mg accelerates the grain boundary diffusion, has a certain grain refinement effect, and has good density and mechanical properties; when the magnesium oxide content exceeds the solid solubility limit, although the grain refinement effect is enhanced, the magnesium aluminum spinel formed at the grain boundary will hinder the discharge of pores.
In terms of grain growth, with the increase of magnesium oxide addition, the grain size and uniformity of the sample show a trend of first increasing and then slightly decreasing. When the magnesium oxide content is 0.25%, the average particle size is the smallest, the grain distribution is more concentrated, and the performance is the best; when the magnesium oxide content is 0.5%, the grains are finer, the grain distribution is more uniform, and the largest grain size is only 2.2μm, but the density is the worst.
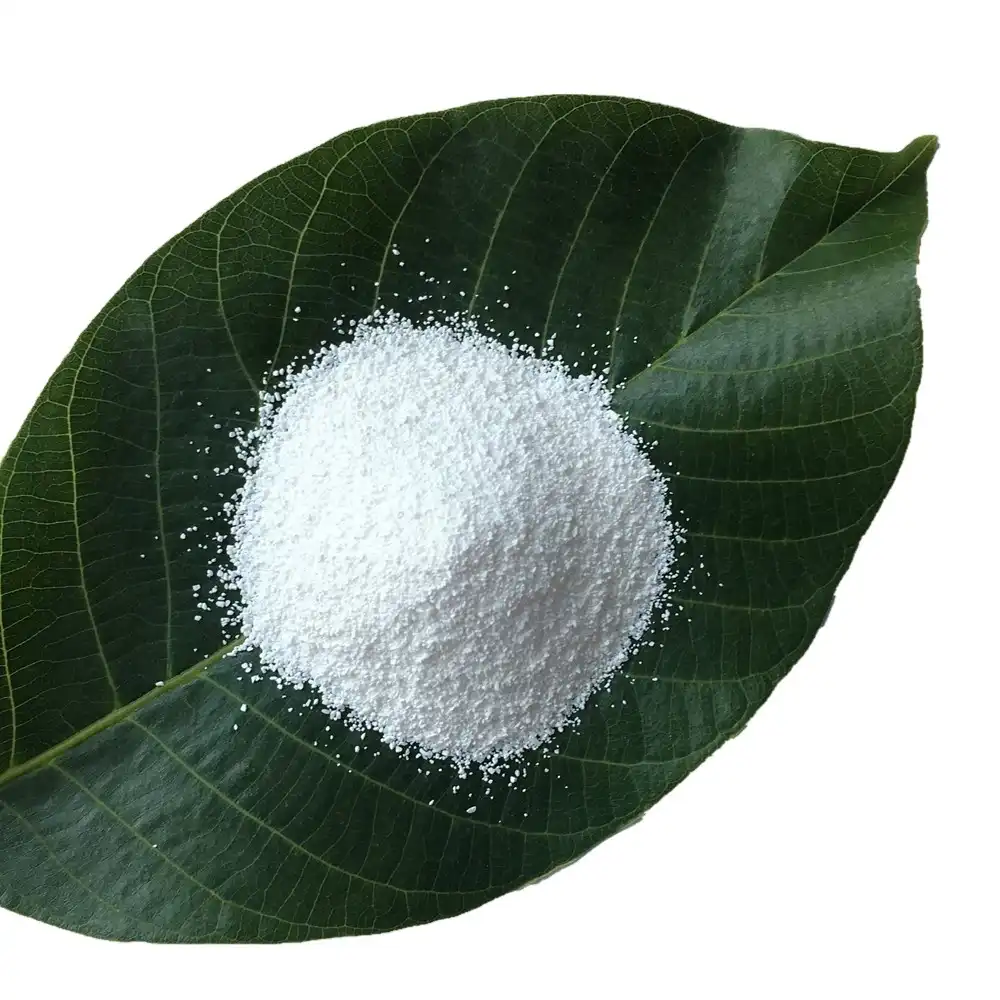
3. Effect of magnesium oxide on the optical properties of alumina transparent ceramics
The effect of magnesium oxide on the mechanical properties and density of alumina transparent ceramics is similar to that of ordinary alumina ceramics. The appropriate amount of magnesium oxide added has a positive effect on its mechanical properties, density, and inhibition of grain growth.
In terms of the optical properties of transparent alumina ceramics, when the doping amount of magnesium oxide is low, the light transmittance of transparent ceramics is relatively high. This is because the appropriate amount of magnesium oxide can inhibit the rapid movement of grain boundaries, making the pores more completely discharged, the ceramics more dense, and the transmittance is higher.
However, with the increase of the doping amount, when the magnesium oxide content exceeds the solid solubility in Al2O3, a second phase will be formed locally, forming a scattering center of light, causing the transmittance of transparent ceramics to decrease.
Effect of magnesium oxide doping on zinc oxide linear ceramics
Zinc oxide linear ceramic resistors in industrial manufacturing have the advantages of a large resistivity variation range, large current density, low nonlinear coefficient, and small resistance temperature coefficient. They are widely used in power-electronics, transportation, communications, and household appliances. However, traditional zinc oxide composite ceramics still have many problems, such as poor structural uniformity, low industrial production repetition rate, poor stability, and insufficient theoretical research.
The effect of magnesium oxide doping on the nonlinear coefficient, resistivity and temperature resistance coefficient of zinc oxide linear ceramic resistors was studied. The results show that the addition of magnesium oxide helps to improve the temperature resistance coefficient of zinc oxide ceramic resistors. An appropriate amount of magnesium oxide can promote sintering and increase the density of ceramics, but excessive addition will reduce the density of ceramics.
Zinc oxide linear ceramic resistors with a basic formula of ZnO‒Al2O3‒magnesium oxide‒Fe2O3‒TiO2‒SiO2 were prepared by solid phase sintering. The effect of magnesium oxide doping on the microstructure, impedance, temperature resistance and frequency resistance characteristics of zinc oxide linear ceramic resistors was studied. The experiment also concluded that in zinc oxide linear ceramic resistors, an appropriate amount of doped magnesium oxide can effectively improve the resistivity and temperature resistance coefficient of the sample.
Effect of magnesium oxide on ferroelectric ceramics
1. Effect of magnesium oxide on the structure and properties of barium strontium titanate ceramics
Barium strontium titanate (BST) ferroelectric ceramic materials have very good application prospects as phase shifters in phased arrays and adjustable devices at microwave frequencies due to their high adjustability and low dielectric loss.
Since various ferroelectric materials currently have certain deficiencies, improving their comprehensive performance through various means has become a key issue that must be solved for the large-scale application of barium strontium titanate materials.
In addition to using rare earth element ions for A-site doping substitution, adding magnesium oxide, MgTiO3, Mg2SiO4 and other compounds to BST ceramics and films can also reduce their dielectric constant and dielectric loss.
2. Effect of magnesium oxide on the properties of BaTiO3-based ceramics
Using a uniform precipitation method, magnesium oxide is uniformly coated on the surface of BaTiO3-based ceramic powder to prepare BaTiO3-based ceramic composite particles coated with magnesium oxide. The effects of different coating amounts on the microstructure, micromorphology, dielectric properties, insulation properties and breakdown voltage of BaTiO3-based ceramics are studied.
Experiments show that the coating agent magnesium oxide can effectively inhibit grain growth, thereby obtaining ceramics with uniform grains. This fine grain effect is due to the inhibitory effect of magnesium oxide in the grain boundary region; magnesium oxide helps to form “shell-core” structure grains, reduce and broaden the ε peak of BaTiO3-based ceramics, and increase resistivity and breakdown voltage strength.
Effect of magnesium oxide on the sintering properties of YAG transparent ceramics
YAG transparent ceramics have the characteristics of high melting point (1950℃), high strength, high thermal conductivity, and stable physical and chemical properties. Whether as a functional material or as a structural material, it shows excellent application prospects. Magnesium oxide is a commonly used sintering aid in its preparation process.
YAG transparent ceramics were prepared by vacuum solid phase reaction sintering technology, and the effect of magnesium oxide as a sintering aid and its addition amount on the microstructure, optical transmittance and other properties of YAG transparent ceramics were studied in depth. The results show that high-quality YAG transparent ceramics can be prepared by using trace magnesium oxide as a sintering aid and vacuum solid phase reaction sintering.
As a sintering aid, magnesium oxide is beneficial to control the diffusion of grain boundaries, the growth of grains and the elimination of pores. However, with the increase of magnesium oxide content, excessive addition will form a second phase in the ceramic, or cause the ceramic to shrink too quickly during sintering to form pores and be unable to eliminate grains, thereby greatly reducing the transmittance of YAG ceramics.
Effect of magnesium oxide on the mechanical properties of Sialon ceramics
Sialon is a solid solution based on Si3N4. When synthesizing Sialon, due to the low diffusion coefficient of Si3N4, decomposition reaction usually occurs when the sintering temperature of Sialon ceramics is reached (greater than 1800℃). Therefore, low-temperature sintering is the development direction of preparing Sialon ceramics.
Through research, it was found that magnesium oxide increased the density of β-sialon ceramics and reduced the sintering temperature. With the increase of sintering temperature, the flexural strength and fracture toughness of β-sialon ceramics increased first and then decreased. When the sintering temperature was 1600℃, the β-sialon ceramic material prepared was tightly bonded, and the flexural strength and fracture toughness reached the maximum.
The above is the influence of magnesium oxide on the mechanical properties, microstructure and other aspects of several ceramics produced by Hebei Messi Biology Co., Ltd. It can be seen that magnesium oxide, as an additive, does play an important role in the production of advanced ceramics.