Hebei Messi Biology Co., Ltd. stated that high-purity magnesium oxide powder material is an important high-temperature resistant material, and the magnesium oxide ceramics prepared by it are widely used in the field of translucent materials. Transparent magnesium oxide ceramics are an optically isotropic body with good resistance to alkali metal vapor corrosion, high melting point, high thermal conductivity, small theoretical density, high insulation and high infrared transmittance. High-quality refractory transparent magnesium oxide ceramics are a very promising material with better performance than alumina ceramics and are widely used in the field of visible light and infrared translucent materials.
1. Preparation method of high-purity MgO powder
High-purity magnesium oxide powder refers to sintered magnesium oxide with a mass fraction of MgO greater than 99% (domestic generally refers to a mass fraction of MgO greater than 98%) and a volume density greater than 3.40g/cm3. The preparation of high-purity MgO uses magnesium-containing compounds as raw materials. Some are made into light-burned magnesium oxide and then fused or re-burned to obtain high-purity magnesium oxide, and some are directly calcined or pyrolyzed to obtain high-purity magnesium oxide. At present, the main preparation methods are direct calcination, brine precipitation, brine direct pyrolysis, and electrofusion.
2. Morphology and control process of different high-purity magnesium oxide powders
- 01 Cubic block magnesium oxide powder
Cubic block high-purity magnesium oxide powder is prepared by electrofusion, with uniform particle size distribution, and can be used to prepare transparent magnesium oxide ceramics and electronic material fillers. In addition, the electrofusion method can also be used to prepare single-crystal MgO with a purity of more than 99.9%, which is widely used as a new material film substrate, such as high-temperature superconducting film, MRAM ferroelectric film, etc.
- 02 Spherical magnesium oxide powder
The thermal conductivity of spherical magnesium oxide can reach 1.5 times that of spherical alumina, which greatly enhances the flexibility of material design in thermal management. It is called the “next generation thermal conductive filler” that connects to spherical alumina.
- 03 Flake magnesium oxide powder
The preparation of rhombic flake magnesium oxide powder is based on low-grade dolomite as raw material, using brine precipitation method, secondary acid leaching and ammonia precipitation method to prepare the precursor magnesium hydroxide, and calcined to obtain rhombic flake multi-void structure nano-MgO crystals. The magnesium oxide is well-crystallized, cubic, with a thickness of about 10-20nm and a maximum area of about 1μm2. It has a chrysanthemum-like two-dimensional rhombic flake void structure. It is widely used in advanced ceramic materials, cosmetics, paints, rubber fillers, catalyst carriers and other fields. It also has important application prospects and huge economic potential in the fields of military, quantum devices, microelectronics, etc.
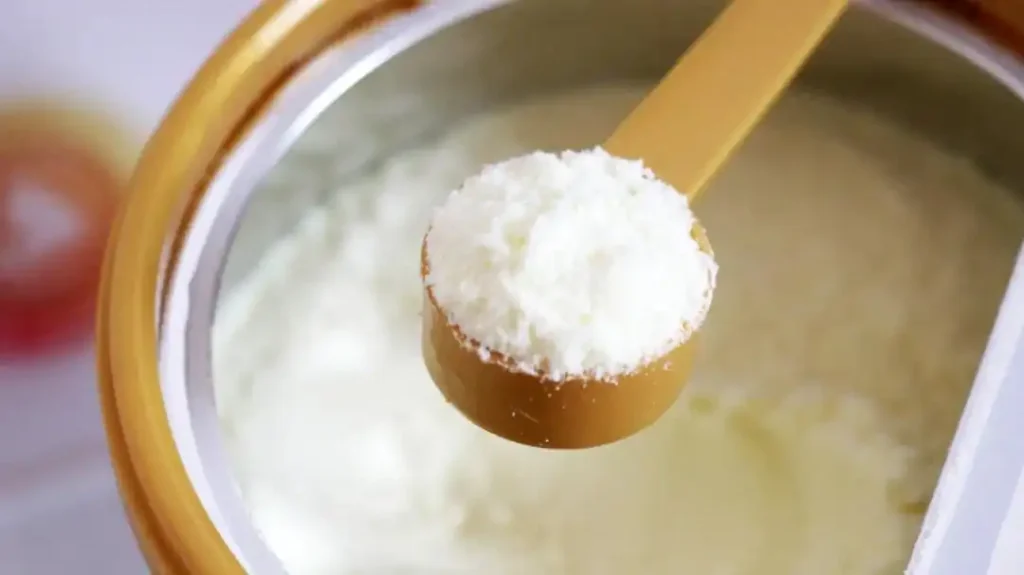
2. Research progress of magnesium oxide ceramics
Currently, the research direction of transparent magnesium oxide ceramic technology is mostly focused on the determination of hot pressing sintering system. There are many sintering methods for transparent ceramics, mainly normal pressure sintering, hot pressing sintering, hot isostatic pressing sintering, spark plasma sintering, etc. The details are as follows:
III. Application of magnesium oxide ceramics
- 01 Transparent magnesium oxide ceramics
Transparent magnesium oxide ceramics are a kind of transparent magnesium oxide ceramics. It belongs to the cubic crystal system and has a melting point of 2800℃. It is made of high-purity magnesium oxide as raw material, adding a small amount of grain growth inhibitor, and is made by hot pressing or normal pressure sintering process.
- 02 Magnesium oxide microwave dielectric ceramics
High-purity magnesium oxide has greater surface activity and high temperature characteristics and high purity. Therefore, magnesium oxide is generally used in ceramic filters to ensure that the filter has good conductivity, mechanical strength and high temperature resistance. Microwave dielectric ceramics are a new type of electronic material. With the official commercialization of 5G, 5G base stations across the country will also be covered in pieces. Microwave dielectric ceramics are also widely used as filters in the construction of 5G base stations. High-purity magnesium oxide usually affects three parameters of the filter: relative dielectric constant, quality factor, and resonant frequency temperature coefficient.
- 03 Preparation of molten ceramic particles
High-purity magnesium oxide and aluminum oxide are used together to prepare molten ceramic particles, which can be widely used in the field of abrasive tools. Together with rare earth oxides as sintering aids, silicon nitride ceramics can be prepared to efficiently and economically manufacture various complex-shaped products, such as cutting tools, sealing rings, bearings, nozzles, and various high-temperature, wear-resistant, and corrosion-resistant products.
- 04 Preparation of magnesium oxide ceramic cores
The magnesium oxide ceramic cores produced have a use temperature of not less than 1600°C, do not react with the cast metal under high temperature conditions, and have a smooth casting surface, which makes up for the defects of a large number of pores and sand sticking in the inner holes of the castings when such materials are cast using silicon-based cores; they have excellent solubility and can be well dissolved in weak acids, with short core removal time, simple core removal equipment, pollution-free, safe and reliable core removal process, and reduced precision casting costs; casting hollow thin-walled castings do not undergo thermal cracking; the core size is highly accurate; they have sufficient strength and do not deform or break during molding, transportation, and furnace loading. Edit and search images
- 05 Preparation of high-toughness ceramic materials
Partially stabilized zirconia ceramics with excellent mechanical properties and resistance to high-temperature aging are made by sintering and heat treating high-purity magnesium oxide and yttrium oxide or rare earth metal oxide as composite stabilizers. This ceramic material can be widely used as high-temperature engineering components and advanced refractory materials.