Glassy carbon electrodes made from nano magnesium oxide have many characteristics, such as good battery stability, high conductivity, high purity, no gas in the electrode, easy surface regeneration, small hydrogen and oxygen overpotential, and low price. Below, Hebei Messi Biology Co., Ltd. briefly introduces the preparation process of adding nano magnesium oxide to lithium batteries.
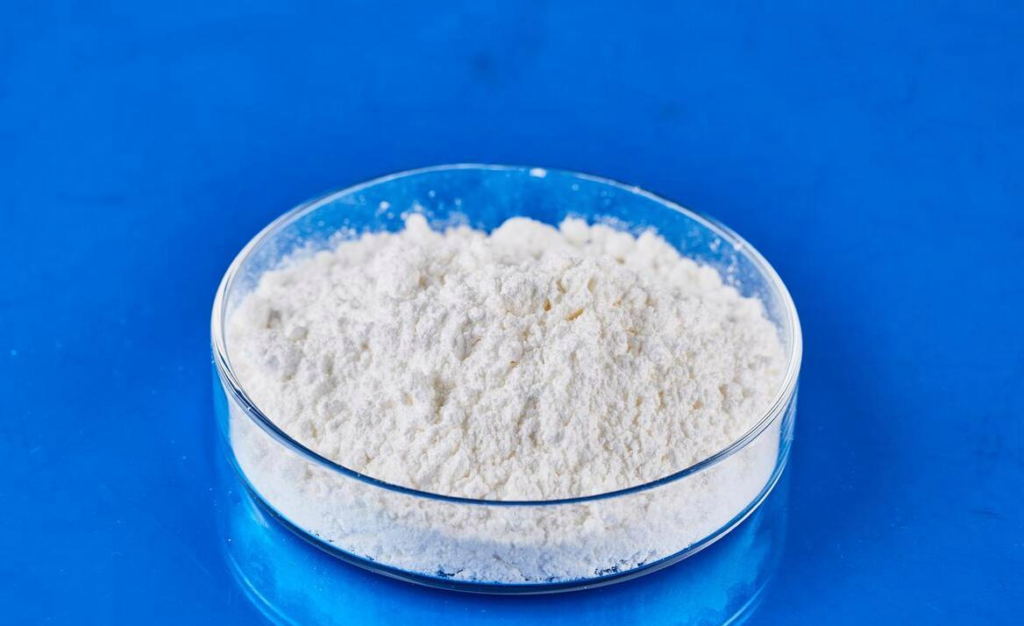
First, lithium-ion batteries choose to add 10-100g/L of insoluble solid particles with a diameter of 0.05-10μm, such as titanium dioxide, silicon dioxide, chromium trioxide, zirconium dioxide, cerium oxide, iron oxide, barium sulfate, silicon carbide, and magnesium oxide; the prepared materials have good charge and discharge efficiency, high specific capacity, and stable cycle performance as lithium ions.
Secondly, the positive electrode material of lithium batteries uses nano magnesium oxide as a conductive dopant to generate magnesium-doped lithium iron manganese phosphate through solid phase reaction, and further makes a nanostructured positive electrode material, whose actual discharge capacity reaches 240mAh/g. This new positive electrode material has the characteristics of high energy, safety and low price, and is suitable for liquid and colloidal lithium-ion batteries, small and medium-sized polymers, and especially for high-power power batteries.
Then, the capacity and cycle performance of the spinel lithium manganese oxide battery are optimized. In the electrolyte of the lithium-ion battery with spinel lithium manganese oxide as the positive electrode material, nano magnesium oxide is added as a deacidifying agent for deacidification, and the addition amount is 0.5-20% of the weight of the electrolyte. By deacidifying the electrolyte, the content of free acid HF in the electrolyte is reduced to below 20ppm, reducing the dissolution effect of HF on LiMn2O4 and improving the capacity and cycle performance of LiMn2O4.
Finally, in the first step, an alkaline solution of nano magnesium oxide as a pH regulator and an ammonia solution as a complexing agent are mixed and added to a mixed aqueous solution containing cobalt salt and nickel salt to coprecipitate Ni-CO composite hydroxide.
In the second step, lithium hydroxide is added to the Ni-CO composite hydroxide, and the mixture is heat-treated at 280-420℃.
In the third step, the product generated in the second step is heat treated in an environment of 650-750°C. Depending on the coprecipitation time, the average particle size of the lithium composite oxide is reduced or the packing density is increased. When the lithium composite oxide is used as an anode active material, a high-capacity lithium-ion secondary battery can be obtained, and the actual amount of magnesium oxide added depends on the specific formula.