Hebei Messi Biology Co., Ltd. stated that the impurity-removed liquid after preliminary purification reacts with magnesium oxide slurry under certain conditions to generate cobalt hydroxide precipitation, and the reaction is as follows: Mg(OH)2+CoSO4=Co(OH)2↓+MgSO4
In order to obtain high-grade cobalt hydroxide products and higher cobalt recovery rates, the use of active magnesium oxide conditions was tested to find out its effects on cobalt grade, cobalt recovery rate, and pH, and to determine the optimal amount of magnesium oxide.
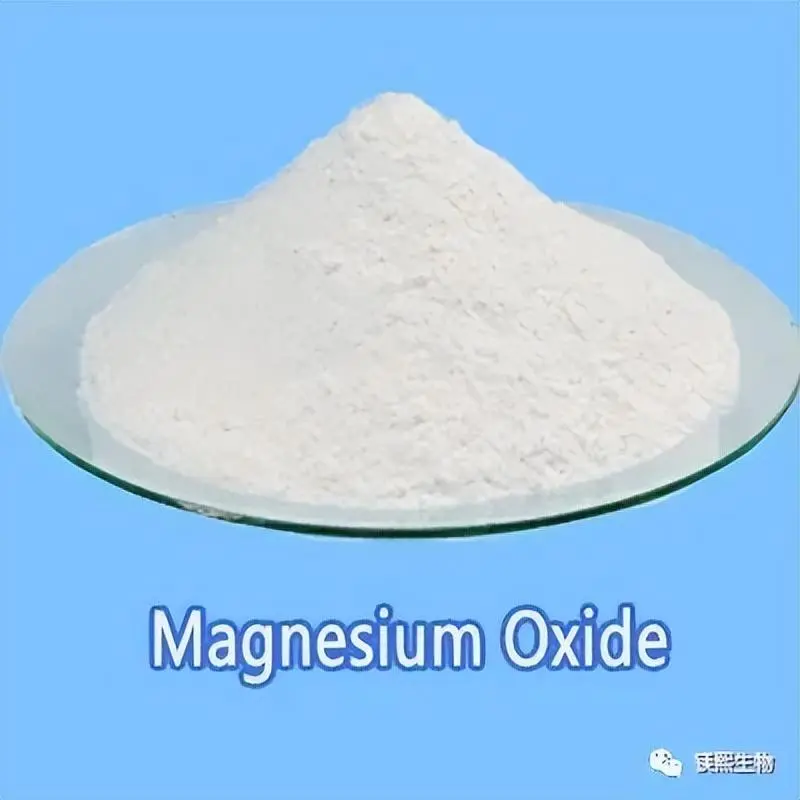
Experimental conditions: temperature 60℃, continuous stirring during the reaction, magnesium oxide slurry concentration 10%, and magnesium oxide addition amounts of 1.0, 1.2, 1.4 and 1.6 times the amount of cobalt metal in the solution.
As the amount of magnesium oxide used increases, the cobalt grade in the cobalt hydroxide product gradually decreases. When the amount of magnesium oxide used is 1.0tMgO/tCo, the cobalt grade reaches the highest value of 36.4%. The more magnesium oxide is added, the higher the cobalt recovery rate of the first cobalt precipitation. When the magnesium oxide addition is 1.6tMg0/tCo, the cobalt recovery rate is almost 100%, but the cobalt grade of the cobalt hydroxide product is only 26%. The pH value of the solution increases with the extension of the reaction time, and within 1 hour after the start of the reaction, the pH value of the solution rises rapidly. The pH value at the end of the reaction increases with the increase of the magnesium oxide addition, and when the magnesium oxide addition is 1.0tMgO/tCo, the end pH is 7.3, and when the addition amount is other multiples, the end pH is above 8.0.
Based on the above, in the industrial trial production, the magnesium oxide usage is selected as 1.0 times the amount of cobalt metal in the solution. The industrial production data are as follows: the end pH of the first cobalt precipitation reaction is 7.2, the cobalt recovery rate is about 81.5%, and a higher grade cobalt hydroxide product is obtained, and its cobalt grade reaches 32.96%.
After the first cobalt precipitation, the cobalt concentration in the solution is still 0.67g/L, so it is necessary to carry out the second cobalt precipitation to recover all the cobalt. The magnesium content in cobalt hydroxide products is relatively high, reaching 5.75%. After inspection and analysis, it was found that about 38% of the magnesium in the product exists in the form of magnesium sulfate. This is caused by the coprecipitation of magnesium sulfate with cobalt hydroxide and magnesium hydroxide during the cobalt precipitation reaction. Therefore, a washing process can be added in production to use new water to wash cobalt hydroxide to remove soluble magnesium sulfate and reduce the content of impurities such as magnesium in cobalt products.