Hebei Messi Biology Co., Ltd. stated that hydromagnesite is a natural mineral with a chemical composition of 4MgCO·Mg(OH)·4H2O, which is a superior mineral resource in my country. When hydromagnesite is calcined, magnesium carbonate decomposes, releasing carbon dioxide gas and generating magnesium oxide at the same time. The most important factors affecting the activity of magnesium oxide are calcination temperature and time. Low-activity magnesium oxide is not easy to hydrate, and the activation energy of the reaction increases. Hexagonal magnesium hydroxide has the advantages of flame retardancy, smoke elimination, safe filling, and low price. It has become an important inorganic flame retardant and has broad market prospects. At present, the production routes of hexagonal magnesium hydroxide flame retardant are mainly sea (brine) water alkali method and brucite crushing processing. The preparation of high-purity hexagonal magnesium hydroxide powder suitable for high-grade flame retardant filler by calcining magnesium oxide with hydromagnesite has important industrial value.
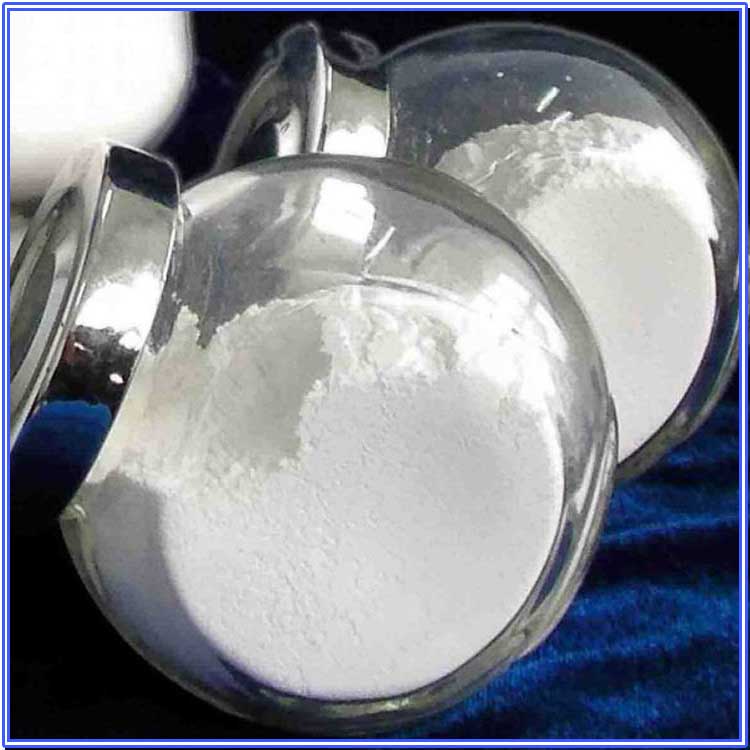
First, after being crushed by a ball mill, the hydromagnesite is purified by reverse flotation and then by forward flotation. Reverse flotation mainly removes silicate minerals, while forward flotation removes calcium-containing minerals, silicate minerals that are not completely removed by reverse flotation, and other impurities. Forward flotation uses water glass and sodium hexametaphosphate as inhibitors and oleic acid as collector, which can effectively remove silicon, calcium minerals and other impurities, and the reagents are simple. After flotation, the Si and Ca contents in the final product magnesium hydroxide obtained by calcination and hydration are significantly reduced, especially the silicate impurities are basically completely removed, and the magnesium hydroxide content is 99.08%.
Secondly, the effects of calcination temperature and calcination time on the activity of magnesium oxide are studied. In the case of complete decomposition of hydromagnesite, too high calcination temperature or too long time will reduce the activity of magnesium oxide, but too short calcination time may cause incomplete decomposition of magnesium carbonate. The citric acid method and hydration method were selected for the determination of the activity of light-burned magnesium. XRD analysis confirmed that the calcined product was magnesium oxide. The experimental results showed that the magnesium oxide obtained was most active under the conditions of calcination at 750℃ and 1.5h. The magnesium oxide was used as raw material to prepare magnesium hydroxide by hydration reaction, and the hydration product was confirmed to be magnesium hydroxide by X-ray diffraction. The hydration curves of magnesium oxide at 30℃, 50℃ and 70℃ were obtained experimentally, and the hydration reaction rate constants at various temperatures were calculated. Then, according to the Arrhenius equation, the hydration activation energy of magnesium oxide was calculated to be approximately 60.7 KJ/mol, which is a chemical reaction rate control.
Finally, the effect of hydration reaction conditions on the particle size and morphology of the obtained magnesium hydroxide was investigated. The particle size of magnesium hydroxide was characterized by polarizing microscopy combined with Dongtu image processing software, and the microscopic size and morphology of the product were observed by scanning electron microscopy. The optimal reaction conditions for preparing ultrafine magnesium hydroxide by hydration of magnesium oxide are: 70℃, 2h, and the concentration of magnesium oxide suspension is 0.5mol/L, and it is not suitable to add ethanol. The effects of additives such as alkali, magnesium salt and dispersant on the particle size and morphology of magnesium hydroxide were studied. Strong alkalinity is not conducive to the preparation of ultrafine magnesium hydroxide by hydration of magnesium oxide.