Hebei Messi Biology Co., Ltd. gab an, dass die direkte Kalzinierungsmethode darin besteht, Magnesiumsalz oder Magnesit bei hohen Temperaturen direkt zu kalzinieren, um Magnesiumoxid zu erhalten. Magnesiumcarbonatpentahydrat (4MgCO₃·Mg(OH)₂·5H₂O) und Magnesiumhydroxid wurden 3 Stunden bei 450 °C kalziniert, um Magnesiumoxidprodukte mit durchschnittlichen Größen von 9 nm bzw. 4,8 nm zu erhalten. Die direkte Kalzinierungsmethode ist einfach im Prozess, erfordert wenig Ausrüstung und lässt sich leicht industrialisieren. Allerdings ist die Morphologie des Magnesiumoxids mit dieser Methode nicht leicht zu regulieren.
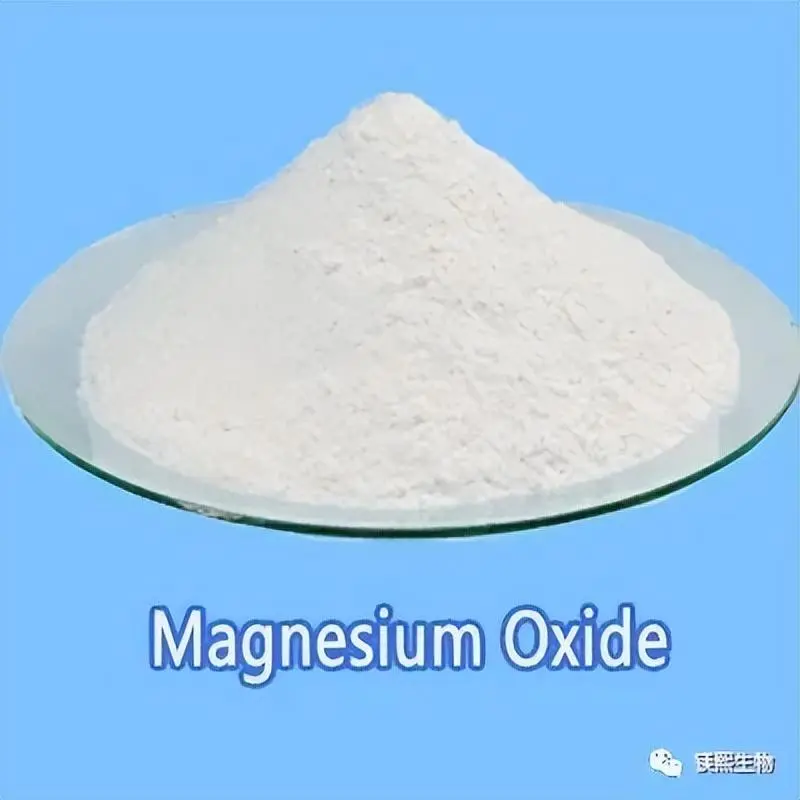
Ammoniumlaugungsmethode
Bei dieser Methode wird das nach der Kalzinierung von Dolomit erhaltene Produkt mit einer Ammoniumsalzlösung umgesetzt, das Filtrat filtriert, mit Ammoniakwasser zu Mg(OH)₂ umgesetzt und Mg(OH)₂ zu Magnesiumoxid kalziniert. Huang et al. Als Magnesiumquelle wurde kalzinierter Dolomit und als Lauge Ammoniumsulfat verwendet. Bei einem Molverhältnis von (NH₄)₂SO₄:MgO von 1,8:1, einem Volumen von 350 ml destilliertem Ammoniak und einer Dosierung von 20 g kalziniertem Dolomit erreichte die Magnesiumlaugungsrate 96,81 %. Das erhaltene Mg(OH)₂ wurde bei 500–1000 °C kalziniert, um Magnesiumoxid mit einer Partikelgröße von 12,4–42,2 nm zu erhalten.
Im Versuch entsteht durch die Ammoniumlaugung Ammoniakgas, das nach Rückgewinnung mit Wasser als Fällungsmittel für die nachfolgende Magnesiumfällung verwendet werden kann. Dadurch entsteht ein geschlossener Kreislaufprozess. Das gewonnene Magnesiumoxid weist ebenfalls eine hohe Reinheit auf. Allerdings ist das Ammoniumsalz-Laugemittel relativ teuer und der Prozessablauf langwierig.
Säurelaugungsverfahren
Bei diesem Verfahren wird das magnesiumhaltige Erz zerkleinert, in Schwefelsäure- oder Salzsäurelösung getaucht, um MgSO₄ oder MgCl₂ zu erhalten. Anschließend wird ein Fällungsmittel verwendet, um MgCO₃ oder Mg(OH)₂ auszufällen. Anschließend wird der Niederschlag kalziniert, um Magnesiumoxid zu erhalten. Gängige Fällungsmittel sind Na₂CO₃, NH₃·H₂O, (HN₄)₂CO₃, NH₄HCO₃ usw. Serpentin dient als Magnesiumquelle und Schwefelsäure als Laugungsmittel. Bei einer Erzpartikelgröße von 75 μm, einer Schwefelsäurekonzentration von 40 %, einer Reaktionstemperatur von 95 °C und einer Reaktionszeit von 3 Stunden beträgt die Magnesiumlaugungsrate 98,40 %. Anschließend wird NH4HCO3 als Fällungsmittel verwendet. Bei einem Molverhältnis von Magnesium zu Ammoniumcarbonat von 1:2, einer Anfangskonzentration des Reaktanten C (Mg2+) von 0,5 mol/l, einer Reaktionstemperatur von 50 °C, einer Reaktionszeit von 50 min, einem pH-Wert der Reaktionslösung von 9,5 und einer Zugabemenge des Additivs CXC-13 von 1 % (Massenanteil) des Gesamtsystems entstehen MgCO3·3H2O-Whisker. Das erhaltene MgCO3·3H2O wird 2 h bei 600 °C kalziniert, um Magnesiumoxid zu erhalten.
Das Säurelaugungsverfahren ist einfach durchzuführen, erfordert wenig Ausrüstung und ist kostengünstig. Es eignet sich besonders für die Verarbeitung minderwertiger Erze. Allerdings gelangen bei der Säurelaugung einige Verunreinigungsionen in die Lösung, sodass die Lauge nachbehandelt werden muss, um die Reinheit des Produkts zu verbessern.
Karbonisierungsmethode
Bei dieser Methode wird das nach dem Kalzinieren des magnesiumhaltigen Erzes gewonnene Material aufgeschlossen, um eine Mg(OH)₂-Suspension zu erzeugen. Anschließend wird es karbonisiert, um Mg(HCO₃)₂ zu erhalten. Anschließend wird es pyrolysiert, um basisches Magnesiumcarbonat zu erhalten, und schließlich kalziniert, um Magnesiumoxid zu erhalten. Gan Yu et al. verwendeten Dolomit als Magnesiumquelle und stellten hochreines Magnesiumoxid mit einem MgO-Gehalt von 99,56 % her. Das Flüssig-Feststoff-Verhältnis (Flüssig-Feststoff-Verhältnis) betrug 10 ml/g, die Temperatur betrug 60 °C, die Rührgeschwindigkeit 500 U/min und die Reaktionszeit 1 Stunde. Das Flüssig-Feststoff-Verhältnis (Flüssig-Feststoff-Verhältnis) betrug 30 ml/g, die Temperatur betrug 25 °C, die Rührgeschwindigkeit 600 U/min, die Karbonisierungszeit 1 Stunde. Die Pyrolyse erfolgte 1 Stunde bei 90 °C.
Das Karbonisierungsverfahren weist eine hohe Selektivität auf, korrodiert die Ausrüstung nicht so leicht, ist leicht zu steuern, hat einen einfachen Prozess und eine stabile Produktqualität. Darüber hinaus ist das bei diesem Verfahren verwendete CO2 kostengünstig und verfügt über eine breite Quelle. Dieses Verfahren eignet sich für die industrielle Produktion und bietet hervorragende Entwicklungsperspektiven.