Hebei Messi Biology Co., Ltd. stated that high-purity magnesium oxide is a magnesium oxide with a mass fraction of magnesium oxide higher than 98%. It has a wide range of uses. For example, in the field of rubber and plastic polymers, it is mainly used as an activator, vulcanizer, stabilizer, etc. In the manufacture of ceramic products, high-purity magnesium oxide can be used for special porcelain crucibles, electrical insulation products and capacitors. Due to its excellent optical, electrical mechanical and chemical properties, it has application potential in optical transparent materials, high-temperature resistant devices, laser materials, etc.
The main methods for preparing high-purity magnesium oxide are: magnesium ore carbonization method, brine ammonia method, carbon ammonium method, brine pyrolysis method, etc., but each process has its own advantages and disadvantages. The magnesium ore carbonization method is affected by impurities such as calcium in the raw materials, so it is difficult to improve the purity of the product. At the same time, the production process has the characteristics of high energy consumption and high production cost. The brine ammonia method is easy to form colloids during the production process, and the calcination process is difficult to control, resulting in local sintering, low activity, low recovery rate and prominent environmental protection problems, so the process significance is not great.
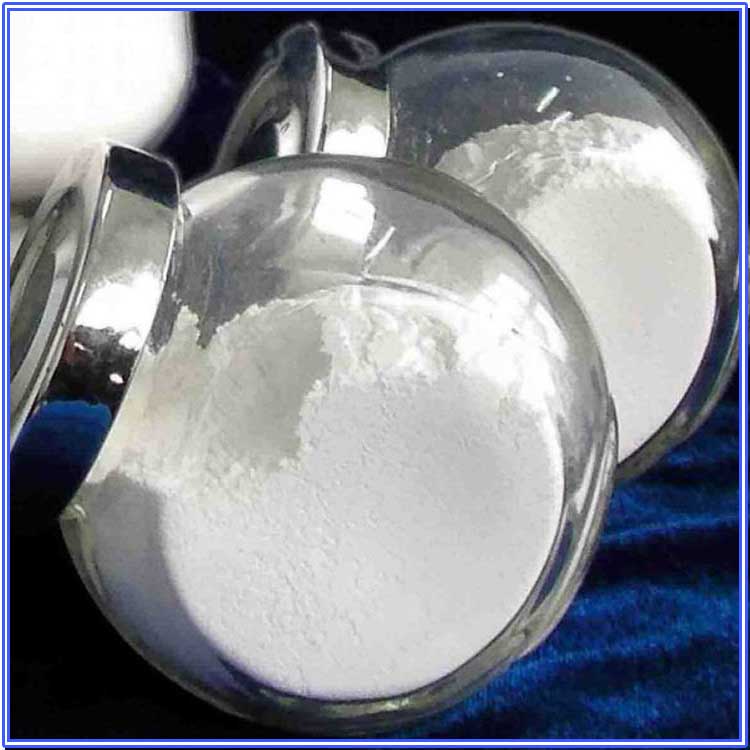
At present, there are three main sources for the production of high-purity magnesium oxide: magnesium ore (magnesite and dolomite, etc.), brine, and seawater. my country’s magnesite resources are extremely rich, with proven industrial reserves of 3 billion tons, accounting for 1/3 of the world’s total reserves. The process of producing magnesium oxide from magnesite is simple, with low investment, low production cost, high product quality, small waste emissions, and relatively economical, so it has strong competitiveness. This method has been valued by industry insiders. Magnesite is mainly used to prepare magnesium refractory raw materials and products, refine metal magnesium, and make heat-proof, thermal insulation, and sound-proof building materials, etc., and has a large development space in the future.
The main process of producing magnesium oxide from magnesite is: carbonization, acid dissolution and ammonium leaching. The carbonization process is simple, non-corrosive, stable product quality, simple equipment, but low leaching rate, low ore utilization rate, large energy consumption, so it cannot be applied to industrial production at present. The acid dissolution leaching rate is high, but the method needs a large amount of concentrated sulfuric acid, which is highly corrosive, has a large consumption of reagents, a low rate of recovery, and high cost, so this method is also not applicable to industrial production. The ammonium leaching method obtains a high product purity, but the process is difficult, corrosive, and a large amount of ammonium bicarbonate is used during precipitation, close to 1 ton plus 6 tons of ammonium bicarbonate, and the raw material consumption is large, and the rate of recovery is low. Obtaining ammonium sulfate does not achieve recycling, and the cost is high and is not widely used.