Hebei Messi Biology Co., Ltd. stated that nickel-cobalt metal has excellent special properties such as excellent energy storage, corrosion resistance, wear resistance, high temperature resistance and high strength. It is a key raw material for stainless steel, rechargeable batteries, electroplating, high-temperature alloys and other industries. It is an important strategic material for the development of the national economy. Therefore, the magnesium oxide precipitation nickel-cobalt industry has a bright future and a good situation.
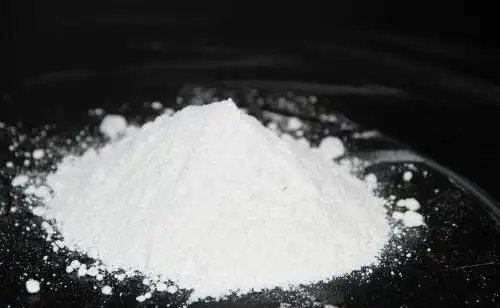
With the depletion of nickel sulfide ore resources, it is increasingly urgent to efficiently develop laterite nickel ore, which accounts for 60% of the global nickel-cobalt resources. The hydrometallurgy of laterite nickel ore generally adopts sulfuric acid leaching to extract metals such as nickel, cobalt, manganese, aluminum, and magnesium into the solution, and then obtains a preliminary purified nickel sulfate solution through a series of impurity removal processes; at present, sodium hydroxide is generally used for precipitation of nickel recovery in nickel sulfate solution, but the alkalinity of sodium hydroxide is too high, which is easy to cause over-alkalinity in the precipitation tank in actual production. Most of the impurities are precipitated into the product, reducing the main content of nickel in nickel hydroxide. At the same time, there are the disadvantages of small precipitate particle size and difficult filtration. In the prior art, there are reports of using magnesium oxide for precipitation to produce nickel hydroxide and cobalt hydroxide, but the high cost of magnesium oxide leads to high production cost of nickel hydroxide, which is not conducive to industrial application.
In order to solve the problem of high cost of nickel hydroxide precipitated by magnesium oxide, Hebei Messi Biology Co., Ltd. provides a method for preparing nickel hydroxide, including: high-pressure acid leaching of laterite nickel ore to obtain nickel sulfate solution; wet grinding of low-activity magnesium oxide using a ball mill to obtain magnesium oxide slurry, the ball-to-material volume ratio (30-50): 1, liquid-to-solid volume ratio (2-5): 1, wet grinding time 0.5-3.0h; adding magnesium oxide slurry to nickel sulfate solution to react to obtain nickel precipitation slurry; separating the nickel precipitation slurry from solid and liquid to obtain nickel precipitation liquid and nickel hydroxide filter cake; drying the nickel hydroxide filter cake to obtain nickel hydroxide. Preferably, the low-activity magnesium oxide has an activity of 60 or 40.