Hebei Messi Biology Co., Ltd. stated that magnesium oxide is a key raw material in oriented silicon steel coating, mainly acting as an isolating agent to prevent the strip from sticking during the high-temperature annealing stage. At the same time, it will react with silicon dioxide on the surface of silicon steel to form an excellent magnesium silicate insulating bottom layer. The industrialization of oriented silicon steel products depends to a large extent on the breakthrough of the bottom layer formation technology, among which magnesium oxide plays a vital role, determining product quality, yield rate and cost competitive advantage. The formation of the bottom layer of thin-gauge high-grade low-temperature oriented silicon steel is the most difficult, and the requirements for magnesium oxide are also the highest.
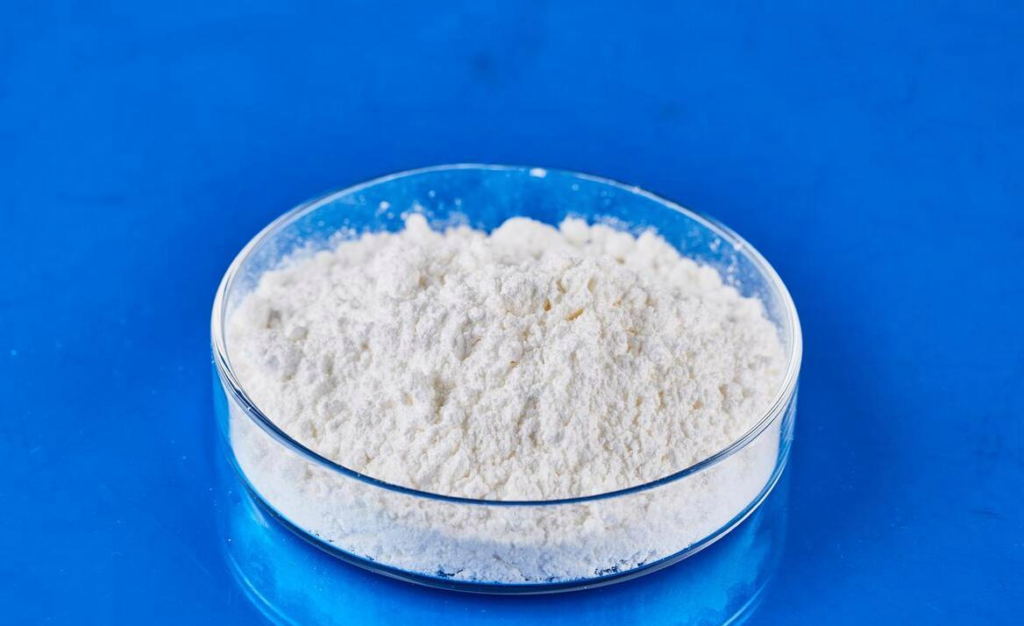
The method of forming a uniform glassy magnesium silicate bottom layer on the surface of oriented silicon steel sheets is to selectively oxidize the silicon steel sheets during the decarburization annealing process so that the silicon on its surface generates silicon dioxide flakes, namely ZFeO.Siq. Then, the magnesium oxide slurry is evenly coated on the surface of the steel sheet, and after drying, it is finally treated in a high-temperature annealing furnace to react with the silicon dioxide flakes on the surface of the steel sheet to form a glassy insulating film, namely the magnesium silicate bottom layer. The magnesium oxide slurry coated on the surface of the steel sheet is basically free of water after being dried in the drying furnace, but the combined water [Mg(OH)2] is brought into the bell-type furnace. When the furnace is heated, water is released. In order to fully remove the water in the furnace, it is necessary to keep it warm for a long time at a lower temperature, which prolongs the operation cycle and increases energy consumption. If the water is not removed at a low temperature, the steel plate will oxidize and cannot form a good bottom layer, or “dew crystals” or “speckled faces” will appear.
Fluctuation or high water content of magnesium oxide will cause fluctuation or increase of water content brought into the bell-type furnace. Under high temperature conditions, uneven evaporation of combined water or increased evaporation will lead to uneven accumulation of water in the narrow gap between the pot sheets, blocking the normal circulation of gas in the furnace, causing local over-oxidation or uneven vaporization of the steel sheet, and finally hindering the formation of glassy insulating film, thereby deteriorating the shape of the steel sheet and weakening the mechanical properties and magnetic conductivity. Therefore, the water content of magnesium oxide coating is closely related to the surface quality and production efficiency of oriented silicon steel.