Hebei Messi Biology Co., Ltd. stated that the specific use of magnesium oxide in silicon steel is that after the oriented silicon steel is decarburized and annealed in a continuous furnace, the upper and lower surfaces of the strip need to be evenly coated with magnesium oxide coating liquid. Magnesium oxide mainly acts as an isolating agent to prevent the strip from sticking during the high-temperature annealing stage. At the same time, it can remove impurities such as nitrogen and sulfur in the steel. In addition, it reacts with silicon dioxide on the surface of silicon steel to form an excellent magnesium silicate insulation bottom layer. Therefore, the coating quality of magnesium oxide coating liquid on the surface of oriented silicon steel plays a vital role in the quality of silicon steel products. At present, magnesium oxide coating liquid is applied by a two-roll coating machine.
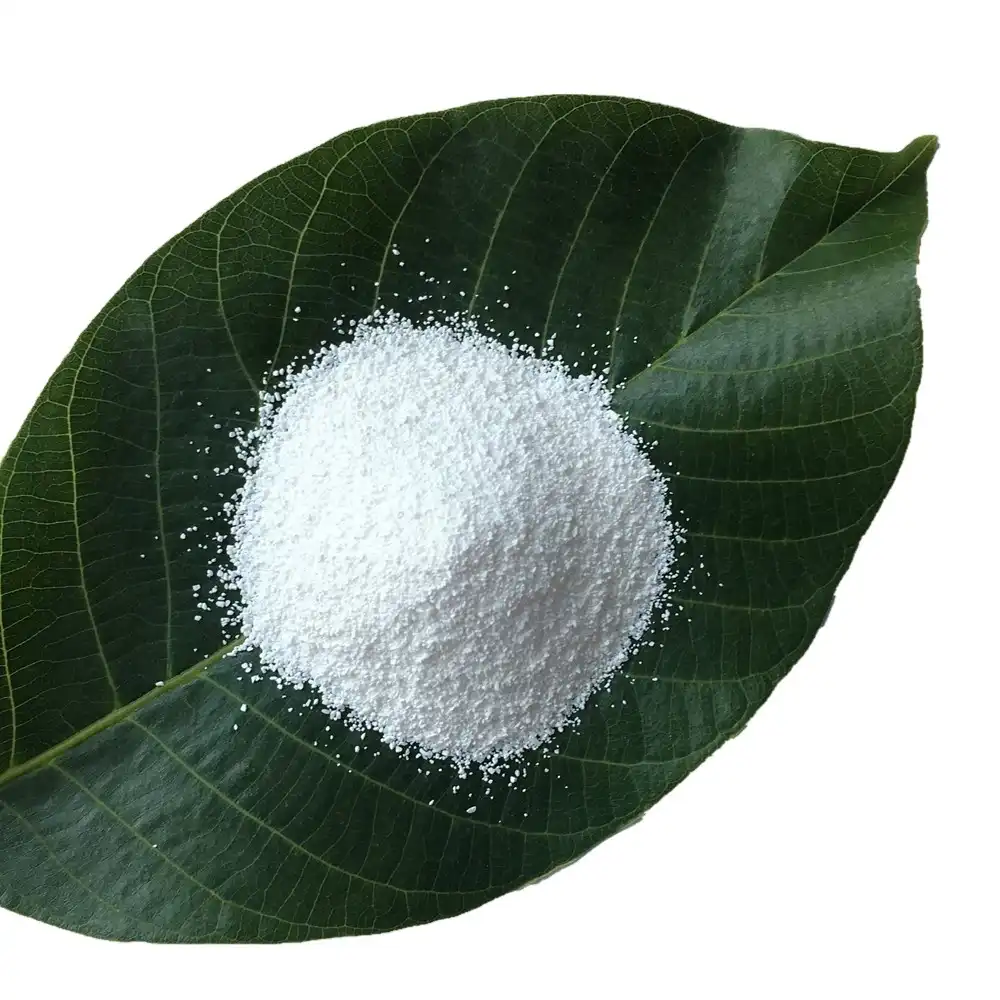
The two-roll coating machine includes an upper coating roller, a lower coating roller, a tray, a magnesium oxide coating liquid circulation device, and a nozzle that sprays the magnesium oxide coating liquid in the magnesium oxide coating liquid circulation device onto the upper surface of the strip; the lower coating roller is immersed in the tray, and the magnesium oxide coating liquid sprayed by the nozzle onto the upper surface of the strip overflows into the tray, and the lower coating roller uses the magnesium oxide coating liquid in the tray to coat the lower surface of the strip. However, during the coating cycle of the magnesium oxide coating liquid, the magnesium oxide solution in the tray does not flow smoothly, and the magnesium oxide reacts with water to form magnesium hydroxide precipitation. The magnesium hydroxide combines with carbon dioxide in the air to form magnesium carbonate that is easy to precipitate.
The fluidity of magnesium carbonate and magnesium hydroxide is very poor, and it is easy to produce agglomeration and deposition. Therefore, the fluidity of the coating liquid in the tray is not high. As time goes by, the coating liquid is prone to accumulation and scaling, resulting in poor coating quality of the lower coating roller, and batches of double lines of varying widths and numbers appear along the strip rolling plate surface, and the lower coating roller is worn, directly causing product quality defects. In severe cases, it is also necessary to stop the machine to replace the coating roller, clean the blockage of the circulation pipeline, and deal with the scaling of the tray. These unfavorable factors greatly increase the labor intensity of employees on the one hand, and interfere with the continuous production on site on the other hand, directly affecting the production efficiency. At the same time, since the solidified magnesium oxide coating liquid is bonded to the tray and cannot be used, it is not only difficult to clean, but also causes waste of magnesium oxide. In addition, due to the liquid throwing off the edge of the coating roller, the coating quality is affected, and the work of the coating machine is interfered with, causing scaling on the edge of the coating roller, resulting in uneven coating on the edge of the strip.