Hebei Messi Biology Co., Ltd. stated that magnesium oxide plays an important role in the alkylation reaction of phenol and is an important catalyst. By optimizing the reaction conditions and improving the preparation method of the catalyst, the activity and selectivity of the MgO catalyst can be further improved, thereby producing more 2,6-DMP to meet the production needs of engineering plastics such as PPO.
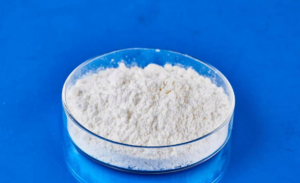
Phenol alkylation reaction
Reaction target: Phenol and methanol undergo gas-phase catalytic alkylation reaction, mainly used to synthesize 2,6-dimethylphenol (2,6-DMP). 2,6-DMP is an important monomer for the production of polyphenylene ether (PPO), which is one of the world’s top five general-purpose engineering plastics with excellent performance and wide application.
Catalyst selection: Magnesium oxide (MgO) is an important catalyst in the gas-phase alkylation reaction of phenol and methanol. Compared with other metal oxide catalysts, such as Al2O3, TiO2, CeO2, MnO2 and Fe2O3, MgO-based catalysts show higher activity and selectivity under specific reaction conditions.
Characteristics of magnesium oxide (MgO) catalyst
Reaction temperature: MgO catalysts are high-temperature catalysts, and the reaction temperature is usually around 450°C.
Activity and selectivity: Under appropriate reaction conditions, MgO catalysts can achieve a 100% conversion rate of phenol, and the selectivity of 2,6-DMP is around 84%.
Economic efficiency: MgO catalysts are easy to prepare, cheap, and economical.
Challenges and improvements
Sintering and carbon deposition: MgO catalysts are prone to sintering and carbon deposition, resulting in a short catalyst life. To solve this problem, researchers are exploring ways to improve the stability and life of the catalyst by improving the catalyst preparation method and adding additives.
Optimization of reaction conditions: The catalytic performance of MgO catalysts can be further improved by optimizing reaction conditions such as reaction temperature, pressure, and space velocity.