Hebei Messi Biology Co., Ltd. stated that the hydrometallurgical treatment process of nickel-cobalt laterite is relatively long, which includes a series of processes such as leaching, impurity removal, precipitation, dissolution, extraction (impurity removal and nickel-cobalt separation) and electrolysis. After the laterite was wet leached, a sulfate system solution containing 3~6g/L nickel and <1g/L cobalt was obtained. Along with the leaching of valuable metals, the iron, aluminum, manganese, and magnesium pen metal elements in the laterite also enter the above-mentioned leaching solution system in the form of ions, which requires the separation of these impurity ions from nickel-cobalt ions.
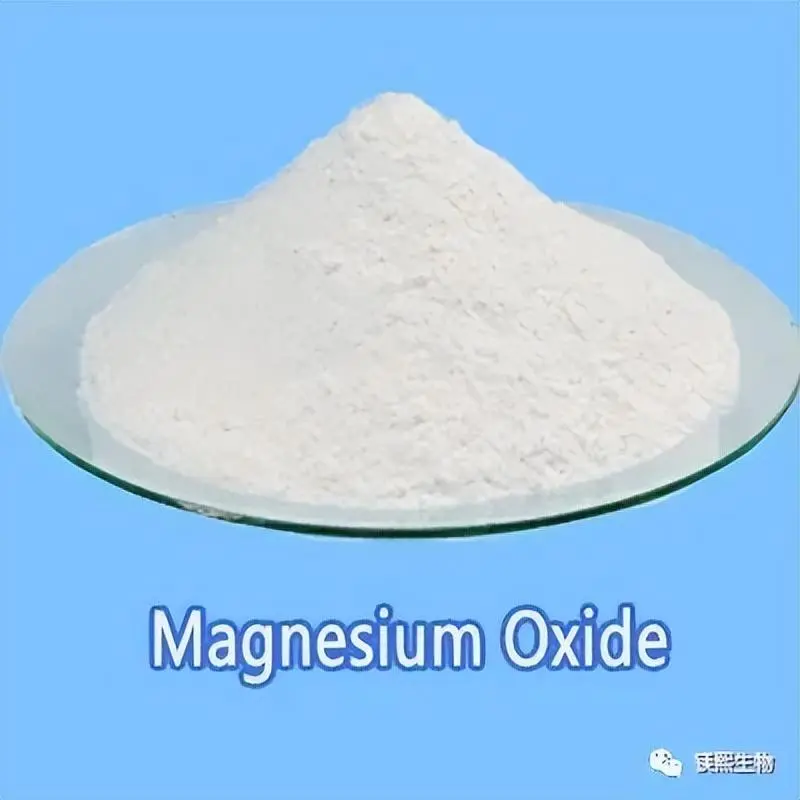
The traditional method adopts the impurity removal and nickel-cobalt precipitation process. This method first removes iron under low pH conditions (iron alum method, goethite method, neutralization precipitation method, etc.), and the pH of the liquid after iron removal is increased for deep purification to remove impurities such as iron and aluminum. The liquid after impurity removal is precipitated with a precipitant for nickel-cobalt precipitation to obtain a nickel-cobalt intermediate product, and finally the pH value is controlled before magnesium precipitation to separate magnesium from nickel-cobalt products. This method has a simple and practical process flow and low cost. Currently, this method is basically used in industry.
There are many types of nickel-cobalt precipitants: caustic soda, soda ash, magnesium hydroxide, magnesium oxide, sulfide, and lime milk. In actual industrial production, it can be selected according to the project process requirements, local precipitant types, prices, transportation conditions, etc.