The entire cobalt industry chain involves four parts: ore mining, cobalt concentrate/intermediate supply, refined cobalt supply and downstream terminal applications. The upstream is the mining of copper-nickel associated ores of cobalt mines, the midstream is the smelting and processing of cobalt mines, and the downstream is mainly consumed by batteries.
As the largest producer of smelting and processing, China has a huge import volume. The Democratic Republic of the Congo is China’s main source of cobalt raw material imports. In recent years, the proportion of refined cobalt output in China’s smelting has increased year by year in the world’s total output, and China’s imports of cobalt mines and cobalt-related products have also increased year by year. In terms of cobalt-related categories, since 2017, China has shifted from mainly importing cobalt mines to mainly cobalt hydrometallurgical intermediate products.
Hebei Messi Biology Co., Ltd. stated that at present, the intermediate products of cobalt hydrometallurgy are basically crude cobalt hydroxide, which is precipitated by the activated magnesium oxide cobalt precipitation process. We try to determine the output of crude cobalt hydroxide by tracking the current process cobalt precipitation materials and output ratio and the export volume of activated magnesium oxide, and then make a prediction on the price of cobalt raw materials. In the current magnesium oxide cobalt precipitation process, the final cobalt salt product with a cobalt concentration of 2g/L-10g/L cobalt precipitation pre-liquid has a Co content of 39.65%, a cobalt recovery rate of more than 99%, and 1t of magnesium oxide can precipitate 3.98t of crude cobalt hydroxide; the quality of the cobalt precipitation product is relatively unstable for a solution of 1g/L-2g/L, and the cobalt grade in the obtained cobalt hydroxide is relatively low, with a cobalt content of about 33%, a cobalt recovery rate of more than 94%, and 1t of magnesium oxide can precipitate 3t of crude cobalt hydroxide.
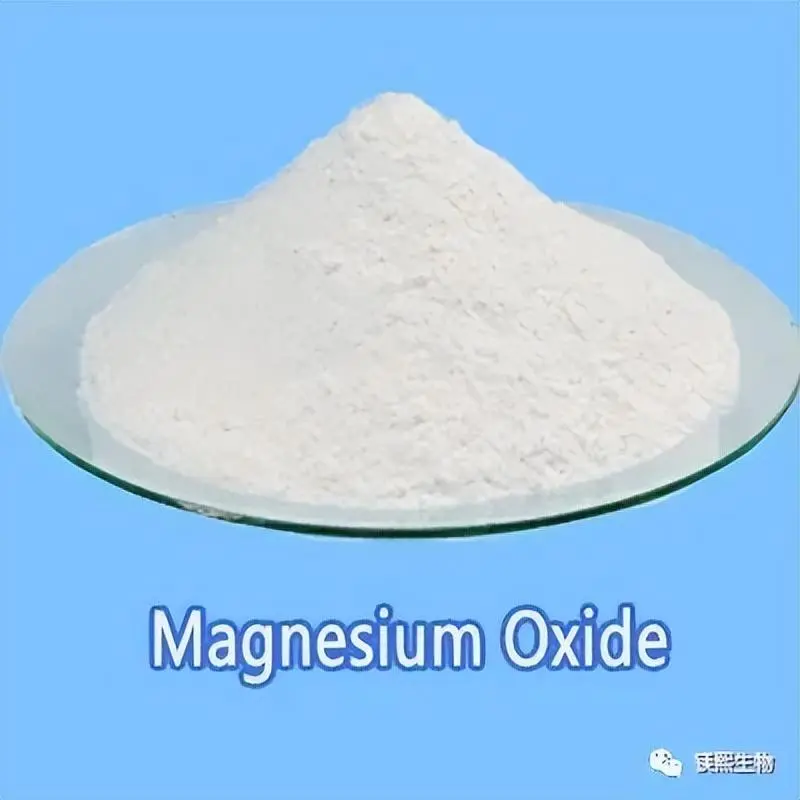
Unfortunately, active magnesium oxide is not listed separately in China’s import and export data, only the export volume of magnesium oxide is listed. However, the wide range of uses of magnesium oxide makes it difficult to determine its specific use in the Democratic Republic of the Congo. In addition, the monthly distribution of magnesium oxide exports has been different since 2017, and the export volume data of active magnesium oxide is unavailable, making it difficult to estimate the cobalt production in the Democratic Republic of the Congo. However, it is believed that when the export amount is stable and available, it is expected that this method can be used to make timely and accurate predictions of cobalt production.
Finally, we estimate the cobalt production of the Democratic Republic of the Congo in each month of 2022 based on the data of China’s cobalt imports from the Democratic Republic of the Congo in 2022 and the proportion of the Democratic Republic of the Congo’s cobalt exports to China in 2021, and then estimate the annual cobalt production of the Democratic Republic of the Congo in 2022 to be 14,000 tons. We predict that as the magnesium oxide cobalt precipitation process matures, the quality of intermediate products will improve and the proportion of cobalt ore imports will be further narrowed, which can effectively reduce the transportation cost of cobalt products and have a certain downward impact on cobalt prices.
1. Introduction to the entire cobalt industry chain
The entire cobalt industry chain involves four parts: ore mining, cobalt concentrate/intermediate supply, refined cobalt supply and downstream terminal applications. The upstream is the mining of copper-nickel associated ores of cobalt mines, the midstream is the smelting and processing of cobalt mines, and the downstream is mainly consumed by batteries.
In terms of mining, cobalt is mostly mined from associated ores, with copper-cobalt mines accounting for the majority. On the raw material side, 98% of cobalt is mined as a by-product, and 2% is mined from primary cobalt mines in Morocco and Canada. At present, the raw materials at the mine end are mainly copper-cobalt associated, accounting for 60%, and nickel-cobalt associated as a supplement. On the production capacity side, the concentration of cobalt mine production is relatively high, mainly concentrated in the Democratic Republic of the Congo. In 2021, the output of the Democratic Republic of the Congo accounted for 70.59% of the total global cobalt mine production.
In terms of imports, China, as the largest producer of smelting and processing, has a huge import volume. The Democratic Republic of the Congo is China’s main source of cobalt raw material imports. In recent years, the proportion of refined cobalt output in China’s smelting has increased year by year, from 3.7% in 1998 to 75.29% in 2021. At the same time, China’s imports of cobalt mines and cobalt-related products have also increased year by year. From January to October 2022, China’s annual imports accounted for 76% of the Democratic Republic of the Congo’s exports, and 97.48% of China’s cobalt products were imported from the Democratic Republic of the Congo. In terms of cobalt-related categories, since 2017, China has shifted from mainly importing cobalt mines to mainly importing cobalt hydrometallurgical intermediate products, and the import volume has grown rapidly. According to the latest data from the customs website, from January to October 2022, the proportion of cobalt hydrometallurgical intermediates in China’s cobalt raw material imports reached 83.36%.
In terms of downstream terminals, with the rapid development of new energy vehicles and 3C, batteries have become the largest cobalt consumption sector, accounting for 87% in 2021, of which consumer electronic batteries account for the majority. Among them, the 3C field is still the main sector for the battery industry to use cobalt. Since then, with the continuous improvement of the penetration rate of new energy vehicles, it is expected that power batteries will gradually become dominant after 2025. The second largest demand area for cobalt is high-temperature alloys and cemented carbides, accounting for about 20%, mainly used in aerospace, military industry, mechanical processing, etc.
2. Activated magnesium oxide cobalt precipitation process
Since 2017, China’s cobalt imports have changed from cobalt ore to cobalt hydrometallurgical intermediates (crude cobalt hydroxide). Its import proportion has increased rapidly. As the largest producer of smelting and processing, China has a huge import volume. Research on the production process of crude cobalt hydroxide is conducive to further estimating the cobalt production in the Democratic Republic of the Congo. One of the processes is activated magnesium oxide cobalt precipitation.
The Democratic Republic of the Congo is China’s main source of cobalt raw material imports. In the past, local companies would extract cobalt through sodium carbonate to save costs, but the finished cobalt carbonate has many impurities and contains a large amount of sodium salt, which will also cause great damage to the environment. In recent years, activated magnesium oxide has been widely used as a cobalt precipitation agent. It has low cost and can save logistics and storage costs. It is also an environmentally friendly solution for producing cobalt products. We tried to determine the output of crude cobalt hydroxide by tracking the current process of cobalt precipitation materials and output ratio and the export volume of activated magnesium oxide, and then make a prediction on the supply of cobalt raw materials.
The main process of magnesium oxide cobalt precipitation process is impurity removal-first stage cobalt precipitation-second stage cobalt precipitation-filtration washing-flash drying process to prepare high-grade crude cobalt hydroxide products.
1) In the current magnesium oxide cobalt precipitation process, the cobalt concentration of the pre-cobalt precipitation solution is relatively high, generally 2g/L-10g/L. Next, we use the low-copper cobalt sulfate solution obtained after grinding, leaching, extraction and other processes of a copper-cobalt mine in the Democratic Republic of the Congo as the production raw material, and industrial-grade quicklime, sodium pyrosulfite, magnesium oxide, and compressed air as auxiliary materials to explore the cobalt content of crude cobalt hydroxide after cobalt precipitation.
The treatment process mainly consists of impurity removal and cobalt precipitation. Impurity removal is achieved by adding a certain proportion of sodium pyrosulfite slurry and compressed air to the low-copper cobalt-containing raffinate to adjust the reaction redox environment, oxidize the difficult-to-hydrolyze precipitated Fe2+ into Fe3+ that is easier to hydrolyze and precipitate, and at the same time, introduce quicklime slurry to adjust the pH value of the solution to achieve the purpose of removing most of the iron ions. In addition, impurity ions such as Cu and Mn can also be partially removed during the impurity removal process. Cobalt precipitation is mainly achieved by adding active magnesium oxide slurry, controlling the reaction pH value, so that the Co ions in the solution are precipitated as Co(OH)2 precipitates, and then through the filter press slurry washing, flash drying and other processes to obtain a cobalt hydroxide dry material product with a water content of about 8%.
Under the optimized impurity removal conditions of 15% quicklime concentration, 5h reaction time, pH=4.5, and potential 420mV, the iron removal rate is 99.5%; under the optimal conditions of pH=8.0, 6h reaction time, and 1.0 magnesium oxide addition (tMgO/tCo), the Co grade of cobalt hydroxide reaches 45.6%; the optimized process conditions for the second stage cobalt precipitation are: reaction time 3h, pH=9.0, and the Co content of the second stage cobalt precipitation slag obtained under this optimized condition reaches 34.2%, and all the second stage cobalt precipitation slag is returned to the first stage cobalt precipitation as a reaction seed, and the final cobalt salt product Co content reaches 39.65%, and the cobalt recovery rate reaches more than 99%. According to calculations, under this condition, 1t magnesium oxide can precipitate 3.98t of crude cobalt hydroxide.
2) For solutions with a cobalt concentration of 1g/L~2g/L, the quality of the cobalt precipitation product is relatively unstable, and the cobalt grade in the obtained cobalt hydroxide is low. However, a recent study shows that by improving the process conditions such as magnesium oxide configuration concentration, a period of cobalt precipitation reaction time, reaction temperature, and reaction end pH value, 1-2g/L low-cobalt liquid can produce a cobalt content of about 33% and a cobalt recovery rate of more than 94%. Under this condition, 1t of magnesium oxide can precipitate 3t of crude cobalt hydroxide.
3. Exploration of the amount of active magnesium oxide
With the output ratio of the current mature process of magnesium oxide precipitation cobalt, we will predict the amount of active magnesium oxide. First of all, magnesium oxide in the Democratic Republic of the Congo is basically imported from China. The application of magnesium oxide in the cobalt precipitation process can be known by the ratio of magnesium oxide export volume and magnesium oxide use in the Democratic Republic of the Congo. Unfortunately, the export volume of active magnesium oxide is not listed separately in China’s known import and export data. There is no further classification of active magnesium oxide under the 251990 sub-item of fused magnesia; sintered magnesia; other magnesium oxide (hereinafter referred to as magnesium oxide), so the export volume of active magnesium oxide cannot be obtained.
Secondly, magnesium oxide has a wide range of uses and can be divided into three categories: industrial-grade magnesium oxide, pharmaceutical-grade magnesium oxide, and food-grade magnesium oxide. Active magnesium oxide is a type of industrial-grade magnesium oxide. In addition, there are dozens of other types, such as lightweight magnesium oxide, magnesium oxide for magnesium stearate, and thermally conductive plastic magnesium oxide. Therefore, it is difficult for us to determine its specific use in the Democratic Republic of the Congo.
Finally, the current monthly distribution of magnesium oxide exports varies. Considering that the impact of the epidemic on magnesium oxide exports since 2020 has been suppressed, or overseas companies may have inventory reserves, resulting in intermittent exports in the month. In summary, it is difficult to estimate the cobalt production in the Democratic Republic of the Congo based on the export volume of active magnesium oxide, but I believe that one day, when the export amount is stable and available, an accurate prediction of cobalt production can be made.
4. Congolese production in 2022
So far, we have explored a method for Congolese cobalt production, using the activated magnesium oxide cobalt precipitation process to infer cobalt production based on the export volume of activated magnesium oxide, but due to the unavailability of data, we have to come to an end. However, we believe that when the export amount is stable and available, this method can be used to make timely and accurate predictions of cobalt production.
Finally, we estimate the cobalt production of Congolese in each month in 2022 based on China’s 2022 cobalt import data from Congo (DRC) and the proportion of Congolese cobalt exports to China in 2021, and then estimate the annual cobalt production of Congolese in 2022 to be 14,000 tons. It is worth noting that the current import of cobalt hydrometallurgical intermediates is calculated at a grade of 30%, and the grade of magnesium oxide cobalt precipitation process under good experimental conditions is nearly 40%. We predict that as the magnesium oxide cobalt precipitation process matures, the grade of intermediates will increase and the proportion of cobalt ore imports will further narrow, which can effectively reduce the transportation cost of cobalt products and have a certain downward impact on cobalt prices.