Cellulose diacetate flakes (referred to as vinegar flakes) are a kind of modified regenerated cellulose in the form of white powder or strips. It is the main raw material for the production of cellulose acetate tows for cigarettes. So what does it have to do with magnesium oxide?
The production of vinegar flakes uses natural cellulose such as high-purity wood pulp or cotton pulp as raw materials, uses acetic anhydride as the acetylating agent, acetic acid as the solvent, and acetylates the natural cellulose under the action of the catalyst sulfuric acid. After pretreatment, acetification, hydrolysis, precipitation, washing, dehydration, drying and other processes, the natural cellulose is modified and becomes a spinnable cellulose diacetate material that is soluble in organic solvents such as acetone. Cellulose diacetate tow is made from natural cellulose such as wood pulp or cotton pulp, which is acetified into cellulose diacetate sheets and processed through production processes such as dissolution, filtration, spinning, curling, and drying. A food-grade precision filter material, mainly used to make cigarette filters. The tow is a kind of regenerated cellulose fiber, which has the characteristics of good moisture absorption and adsorption. The cross-section shape of the monofilament fiber is Y-shaped. The specific surface area of the fiber is large, and it has good adsorption and interception effects on harmful components in cigarette smoke.
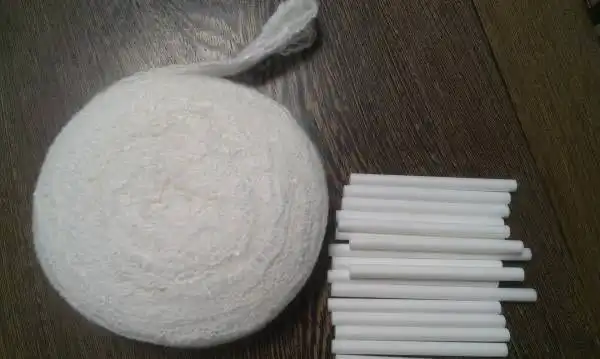
The fiber of cellulose acetate raw material needs to be dissolved. It cannot be dissolved in ordinary solvents, but it is soluble in magnesium acetate. This requires the reaction of magnesium oxide and acetic acid. At the same time, sulfuric acid is needed as a catalyst during the entire reaction process, and magnesium oxide is required at the end of the reaction. Make a terminator. The addition ratio of magnesium oxide is about 4%, and some of the indicators of magnesium oxide are: MgO≥95, Fe≤0.2, Ca≤1, SiO≤1.5, Cl≤10PPM, and the particle size is 70-80μm. At the same time, the activity of magnesium oxide has a great relationship with the reaction temperature and time. The influencing factors are specific surface area, pore size distribution, and surface roughness. The technology of cellulose diacetate tablets comes from foreign countries, and its requirements for magnesium oxide are also high. At first, domestic manufacturers imported brine-based magnesium oxide, but in order to reduce costs, localization is needed. Due to the current domestic brine production of oxidation The magnesium chloride content is relatively high and the calcium content of the dolomite method is relatively high. Only serpentine calcination can meet the requirements.