Hebei Messi Biology Co., Ltd. stated that a low-grade cobalt ore was used as raw material, and the contents of CO, Mn, Fe, Al2O3 and MgO in the low-grade cobalt ore were 0.41%, 0.36%, 2.53%, 9.28% and 3.64% respectively. In the industrial test of high-efficiency recovery of cobalt from active magnesium oxide of low-grade cobalt ore, the following steps are included in sequence:
The first step is leaching: add the supernatant of the slurry reservoir to adjust the leached ore to a slurry concentration of 30%, then add concentrated sulfuric acid and reducing agent, control the sulfuric acid mass concentration of 8g/l and the redox potential of 340mv in the leaching process, react for 360min, and separate the solid and liquid after the reaction to obtain cobalt-containing liquid 1 and leaching slag, which is sent to the slurry reservoir for storage;
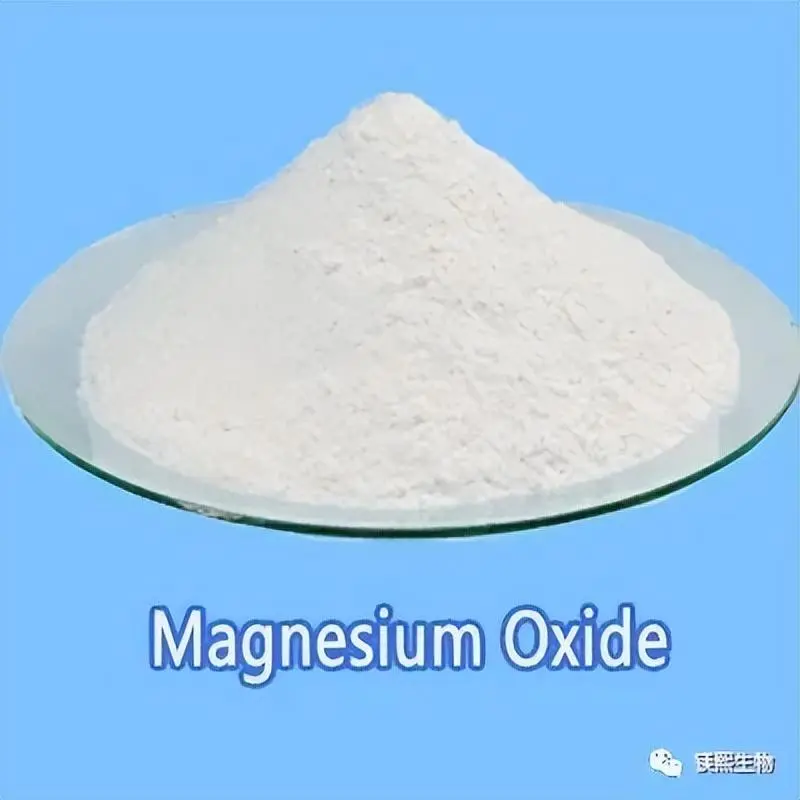
The second step is iron removal: add the second-stage cobalt precipitation slag to the cobalt-containing liquid 1, react for 20min under air filling conditions, then add the low-grade cobalt ore with a mass percentage of 80% of the particle size of -0.074mm, and react for 90min under air filling conditions, control the end point pH value of the iron removal reaction to 4.2, and separate the solid and liquid after the reaction to obtain cobalt-containing liquid 2 and neutralization slag, The neutralized slag is returned to the first leaching process;
The third step is manganese removal: add a special oxidant to the cobalt-containing liquid 2, control the redox potential to 1250mv, and remove manganese for 60min. After the reaction, the solid-liquid separation is completed to obtain the cobalt-containing liquid 3 and the manganese-removing slag, and the manganese-removing slag is sent to the slag slurry for storage;
The fourth step is two-stage cobalt precipitation: one-stage cobalt precipitation, add 10% active magnesium oxide milk to the cobalt-containing liquid 3, and carry out a cobalt precipitation reaction for 270min under the condition of controlling the pH value to 7.95. After the reaction, the solid-liquid separation is completed to obtain the cobalt hydroxide product and the cobalt precipitation liquid 1, the second stage cobalt precipitation, add lime milk to the cobalt precipitation liquid 1, and carry out the second stage cobalt precipitation reaction for 120min under the condition of controlling the pH value to 8.60. After the reaction, the solid-liquid separation is completed to obtain the second stage cobalt precipitation slag and the cobalt precipitation liquid 2. The second stage cobalt precipitation slag is returned to the second step of iron removal process, and the cobalt precipitation liquid 2 is discharged after the treatment meets the standards.