Hebei Messi Biology Co., Ltd. gab an, dass die Rohstoffe für die Herstellung von Magnesiumoxid in Siliziumstahlqualität hauptsächlich Magnesit (MgCO₃), Dolomit (CaCO₃·MgCO₃), magnesiumhaltige Industrienebenprodukte, Meerwasser oder Salzlake (MgCl₂) usw. umfassen. Der Produktionsprozess lässt sich in die Magnesiumerzkarbonisierung, das Ammoniumcarbonatverfahren mit basischem Magnesiumcarbonat als Zwischenprodukt und die Solepyrolyse mit basischem Magnesiumchlorid als Zwischenprodukt unterteilen.
1. Herstellung von Magnesiumoxid in Siliziumstahlqualität aus Salzlake
Die Sole wird durch Auflösen und Filtrieren von salzsaurer Bischofit (MgCL₂ · 6H₂O) gewonnen, um feste Verunreinigungen zu entfernen. Anschließend wird mit Ammoniak reagiert, um Magnesiumhydroxid als Zwischenprodukt zu erhalten: MgCL₂ + 2NH₃ + 2H₂O = Mg(OH)₂ + 2NH₄Cl
Magnesiumhydroxid wird bei hohen Temperaturen kalziniert, um Magnesiumoxid zu erhalten: Mg(OH)₂ = Mg₅ + H₂O
2. Herstellung von Magnesiumoxid in Siliziumstahlqualität durch Magnesiumerzkarbonisierung
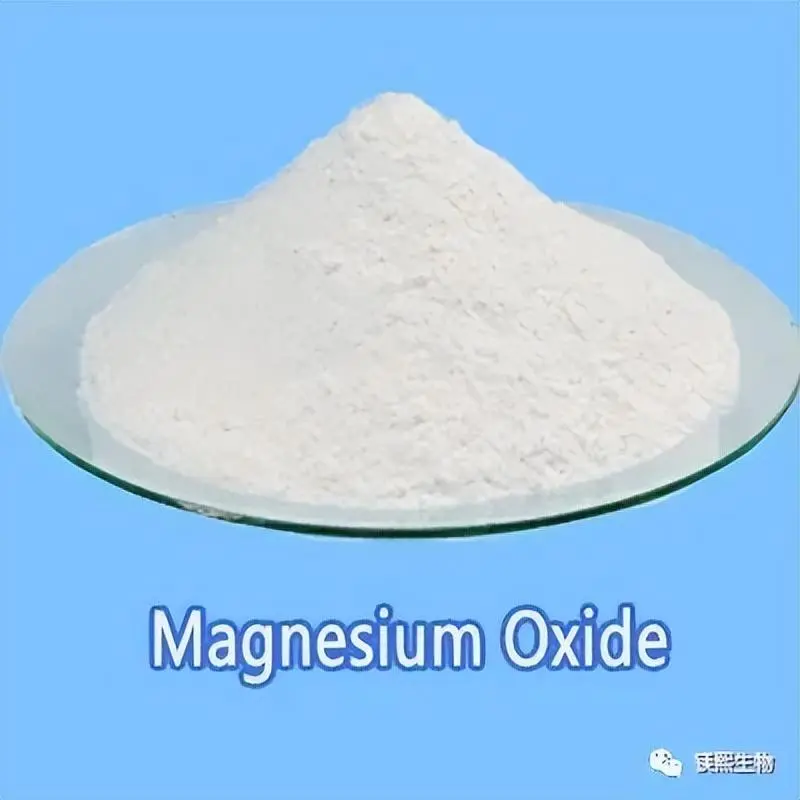
Bei der Magnesiumerzkarbonisierung (z. B. Dolomit, Magnesit) wird bei hohen Temperaturen kalziniert. Das kalzinierte Magnesiumoxid wird hydratisiert, karbonisiert und gefiltert, um Magnesium und Verunreinigungen vollständig abzutrennen. Das magnesiumhaltige Filtrat wird anschließend pyrolysiert, um basisches Magnesiumcarbonat zu erzeugen. Dieses wird gefiltert und kalziniert, um Magnesiumoxidprodukte zu erhalten.
Magnesiumoxid in Siliziumstahlqualität wurde durch Karbonisierung unter Verwendung von Salzsäurebischofit [3MgCO3·Mg(OH)2·3H2O] als Rohmaterial hergestellt. Die Rohmaterialien wurden in einen Rohrwiderstandsofen gefüllt und 1,5 Stunden bei 750 °C kalziniert. Die kalzinierten Materialien wurden 1 Stunde bei 90 °C hydratisiert, und pro 50 g Material wurde 1 l Wasser hinzugefügt. Das Filtrat wurde dann mit CO2 bei 40 °C, einem CO2-Partialdruck von 0,4–0,6 MPa und einem Endpunkt DH von 7 für die Karbonisierungsreaktion versetzt. Die karbonisierte Flüssigkeit wurde gefiltert. Das Filtrat wurde bei 90 °C pyrolysiert, um basisches Magnesiumcarbonat-Niederschlag zu erzeugen. Der Niederschlag wurde gefiltert und getrocknet und anschließend in einem Rohrwiderstandsofen eine Stunde lang bei 900 °C kalziniert. Dabei entstand Magnesiumoxid in Siliziumstahlqualität mit einer Hydratationsrate von <4 % (Massenanteil) und einer Suspension von 6 mm/h. Die Studie ergab, dass die Hydratationsrate und das scheinbare spezifische Volumen mit steigender Kalzinierungstemperatur des basischen Magnesiumcarbonats (800–1000 °C) abnahmen und die Suspension mit steigender Temperatur zunahm.
Dolomit und Anthrazit wurden in einem Hochtemperatur-Widerstandsofen kalziniert, und das kalzinierte Produkt wurde mit Wasser aufgeschlossen. Das Produkt wurde mittels einer Kombination aus Grobsiebung, zweistufiger Zyklonabscheidung und Vakuumsiebung gefiltert und das Filtrat karbonisiert. Die MgO-Massenkonzentration in der karbonisierten Flüssigkeit betrug 26–30 g/l, die CaO-Massenkonzentration 42–45 g/l. Die gefilterte wässrige Magnesiumlösung wird durch Pyrolyse in basisches Magnesiumcarbonat umgewandelt und anschließend bei 950–980 °C kalziniert. Nach Alterung, Waschen, Zentrifugaldehydratation und Trocknung entsteht Magnesiumoxid. Das erhaltene Magnesiumoxid in Siliziumstahlqualität mit einer Partikelgröße von ≤ 3 µm und einem Hydratationsgrad von 3,2 % (Massenanteil) übertrifft in allen Punkten den Unternehmensstandard.
Studien haben gezeigt, dass sich die Produktpartikel bei einer Pyrolysetemperatur über 85 °C deutlich vergrößern; bei einer Pyrolysetemperatur unter 55 °C ist die Zersetzung im Zersetzer unvollständig, was zu einer geringeren Ausbeute führt. Magnesiumoxid in Siliziumstahlqualität wird durch Magnesiumerzkarbonisierung aus Erz als Rohstoff hergestellt. Aufgrund von Verunreinigungen wie Calcium im Rohstoff kann die Produktreinheit den Standard nur schwer erfüllen. Gleichzeitig ergeben sich Nachteile wie ein hoher Energieverbrauch und hohe Produktionskosten. Obwohl die Niedertemperaturpyrolysetechnologie Durchbrüche bei der Reduzierung des Energieverbrauchs erzielt hat, ist die Produktreinheit dieses Verfahrens schwer zu erreichen und wurde bisher nicht in der industriellen Produktion eingesetzt.
3. Herstellung von Magnesiumoxid in Siliziumstahlqualität durch Ammoniumcarbonat-Verfahren
Bei der Ammoniumcarbonat-Methode werden Fällungsmittel wie Ammoniumcarbonat und Ammoniumbicarbonat mit einer raffinierten magnesiumhaltigen Lösung in einem Reaktor erhitzt und umgesetzt, um basische Magnesiumcarbonat-Zwischenprodukte zu erzeugen. Die Ausgangsflüssigkeit wird gefiltert, gewaschen, getrocknet, kalziniert, wärmebehandelt und weiteren Prozessen unterzogen, um Magnesiumoxidprodukte zu erhalten.
4. Herstellung von Magnesiumoxid in Siliziumstahlqualität durch Solepyrolyse-Verfahren
Bei der Solepyrolyse-Methode werden die Rohstoffe physikalisch und chemisch gereinigt. Anschließend wird die gereinigte Flüssigkeit in Luft oder Heißluft pyrolysiert, um allmählich Kristallwasser zu entfernen. Anschließend wird kalziniert, um Magnesiumoxid und Salzsäure zu erhalten.