Hebei Messi Biology Co., Ltd. stated that by using specific compounds to surface modify magnesium hydroxide, it can solve its shortcomings of high surface free energy, strong polarity, and easy agglomeration, making its surface hydrophobic and improving the interaction between magnesium hydroxide and magnesium hydroxide. Polymer compatibility. At present, the commonly used surface modification methods of magnesium hydroxide include ultrafine refinement, surface chemical coating and microencapsulation.
1. Magnesium hydroxide chemical coating modification
Chemical coating modification is the most commonly used modification method for surface modification of magnesium hydroxide. There are many types of modifiers available, such as surfactants, coupling agents, hyperdispersants and modifier compounds, etc.
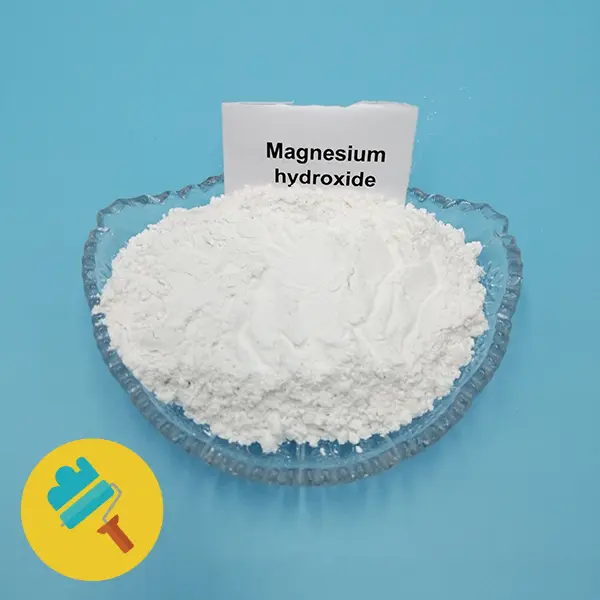
(1) Surfactant
Since the surface of magnesium hydroxide has a high positive charge, anionic surfactants are generally used, such as stearic acid, sodium stearate, zinc stearate, sodium oleate, and sodium dodecyl sulfonate. Zinc stearate is used to dry-modify magnesium hydroxide. When the modified magnesium hydroxide is added to PP, the dispersion becomes better, the viscosity of the composite material decreases, and the elastic modulus, impact strength and flame retardant properties are significantly improved. .
(2) Coupling agent treatment
Coupling agent treatment is currently the most commonly used modification method for surface modification of magnesium hydroxide, among which silane coupling agent is the most commonly used. In industry, both dry and wet processes for modifying magnesium hydroxide with silane coupling agents are used. N-phenyl-γ-aminopropyltrimethoxysilane coupling agent was used to conduct wet process on ultra-fine magnesium hydroxide. Modification, after modification, silane coupling was performed on the surface of magnesium hydroxide and the siloxane structure was grafted to the surface of magnesium hydroxide.
(3) Modifier compounding
The combination of different types of modifiers can give full play to their respective advantages and form complementarities. They can show good modification effects in practice and have good development prospects. Silane coupling agent (A-172) and stearic acid are compounded to modify magnesium hydroxide. After modification, silane and stearic acid form stable chemical bonds with the surface of magnesium hydroxide. The modified hydroxide is compounded with The dispersion and compatibility of magnesium in soft PVC are improved.
2. Magnesium hydroxide polymerization graft coating
Polymerization graft modification can significantly improve the dispersion and compatibility of magnesium hydroxide in the polymer, and the mechanical properties have also been improved to a certain extent. First use vinyl silane (A-172) to wet-modify magnesium hydroxide, introduce -C=C- on the surface of magnesium hydroxide, then use vinyl acetate as the monomer, ammonium persulfate as the initiator, and dodecane Using sodium sulfate as an emulsifier, polymerizing and grafting vinylated magnesium hydroxide, and adding the modified magnesium hydroxide to EVA, the mechanical properties and flame retardant properties of the prepared composite materials meet the requirements for industrial applications.
3. Magnesium hydroxide capsule modification
Encapsulated modified magnesium hydroxide can not only improve its compatibility with the polymer matrix, but also improve the mechanical properties, thermal stability and flame retardant properties of composite materials, making it a research hotspot in the field of flame retardancy. The disadvantage is that coating is difficult and requires strict control of experimental conditions. Magnesium hydroxide was microencapsulated and modified using urea-formaldehyde resin and melamine resin as wall materials respectively. The modified magnesium hydroxide has good thermal stability and has improved interfacial adhesion with low-density polyethylene matrix. Microcapsules are added The mechanical properties and flame retardant properties of composite materials prepared from magnesium hydroxide have been greatly improved.