The dry granulation process of pharmaceutical and food grade magnesium oxide refers to mixing magnesium oxide powder prepared by wet method with auxiliary agents such as binders, dispersants, lubricants, etc. under anhydrous or low-moisture conditions, and then granulating the powder through granulation equipment. A method of producing particles of a certain particle size and shape. This process has the advantages of high granulation efficiency, stable product quality, and less environmental pollution.
The specific process of pharmaceutical and food grade magnesium oxide dry granulation process is as follows:
① Raw material preparation: Weigh magnesium oxide powder, binder, dispersant, lubricant and other auxiliary agents and mix them evenly.
② Granulation: The mixture is fed into the granulation equipment and made into particles of a certain size and shape through extrusion, calendering, rolling, etc.
③ Drying: Send the granulated particles to drying equipment to remove the moisture in the particles.
④ Screening: Screen the dried particles to remove particles that are too large or too small.
⑤ Packaging: Pack the screened particles as required.
In the dry granulation process of pharmaceutical and food grade magnesium oxide, granulation equipment is the key equipment. Commonly used granulation equipment includes extrusion granulator, drum granulator, fluidized bed granulator, etc. The extrusion granulator extrudes the mixture through an extrusion die. The granulation efficiency is high, but the product particle size distribution is uneven. The drum granulator rolls the mixture into shape in a drum. The granulation efficiency is low, but the product particle size distribution is uniform. The fluidized bed granulator rolls and granulates the mixture in a fluidized bed. It has high granulation efficiency and uniform product particle size distribution.
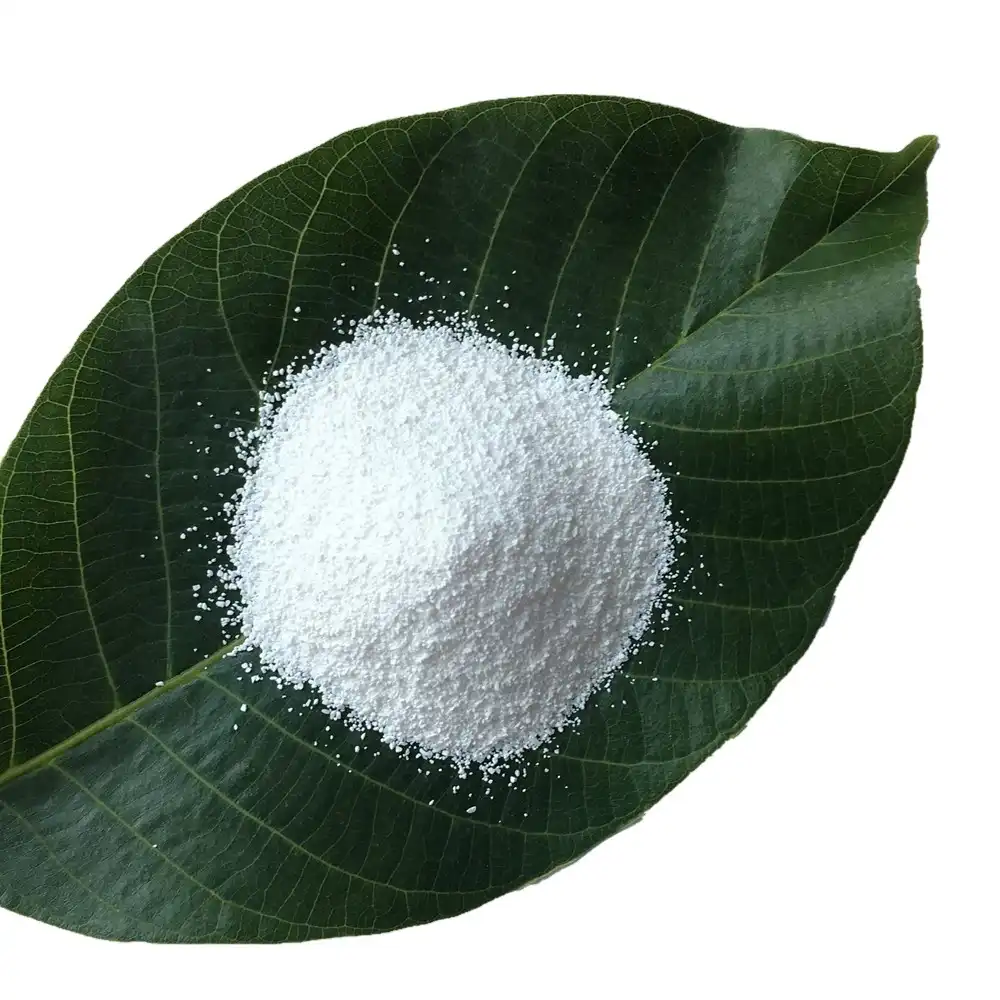
The main control parameters of the pharmaceutical and food grade magnesium oxide dry granulation process are:
① Raw material ratio: The raw material ratio directly affects the performance and quality of the product.
② Granulation pressure: The higher the granulation pressure, the higher the granulation efficiency, but the smaller the product particle size.
③ Drying temperature: Drying temperature that is too high will cause product discoloration and deterioration.
④ Screening particle size: The screening particle size should be determined according to the specific requirements of the product.
The dry granulation process of medical and food grade magnesium oxide is the main method for producing medical and food grade magnesium oxide. This process has the advantages of high granulation efficiency, stable product quality, and less environmental pollution.