Hebei Messi Biology Co., Ltd. stated that magnesium hydroxide flame retardant is one of the most widely used varieties of halogen-free flame retardants. Since magnesium hydroxide has the characteristics of smoke suppression, thermal stability, promoting carbonization of substrates and acid removal ability while being flame retardant, it is widely used in plastics, elastomers and rubber materials such as polyvinyl chloride (PVC), polypropylene (PP), polyethylene (PE), vinyl acetate (EVA), polystyrene (PS), polyamide (PA). The ideal magnesium hydroxide flame retardant added to the polymer requires high purity and suitable particle size distribution. Because magnesium hydroxide as a flame retardant requires a high filling amount, if the particles of magnesium hydroxide used are large, the composite material prepared by adding it to the matrix is easy to form cracks between magnesium hydroxide and the matrix, thereby affecting the overall performance of the material. The purity of magnesium hydroxide is one of the determining factors of the electrical performance of composite materials, so the ideal magnesium hydroxide as a flame retardant filler has high requirements for its product purity, element content, particle size range, etc.
At present, there are two main methods for producing magnesium hydroxide: one is the direct crushing method of brucite; the other is the reaction conversion method of magnesium-containing raw materials. Since the purity of natural brucite is low, adding it to polymer materials as a flame retardant often leads to a decrease in the electrical performance of the composite material. The magnesium-containing raw material conversion method can prepare magnesium hydroxide flame retardant products of different specifications by controlling different reaction conditions, so it has become the main method for producing magnesium hydroxide flame retardant at present.
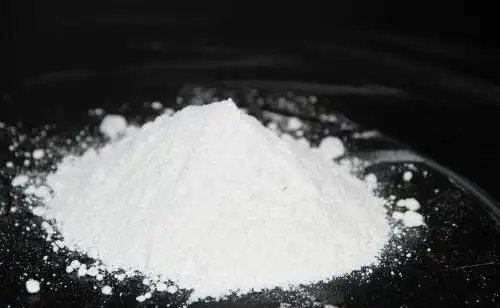
The main precipitants used in the prior art using the magnesium-containing raw material conversion method are sodium hydroxide, ammonia water, and lime milk. Since the cost price of the obtained product is high when sodium hydroxide and ammonia water are used as precipitants alone, people are increasingly inclined to use lime milk, which is easy to obtain as a precipitant, to prepare magnesium hydroxide products.
In one prior art, magnesium hydroxide products with a purity of more than 98.5% and a calcium oxide content of less than 0.2% are prepared using magnesium chloride and lime milk as raw materials. This preparation method uses a single lime milk as a precipitant. Due to the properties of calcium hydroxide itself, it is difficult to accurately control some process parameters in the reaction process in actual production, which brings certain difficulties to the production operation, thereby affecting the final quality of the product. In another prior art, a saturated lime solution is used to react with refined brine to produce a magnesium hydroxide product. Due to the low solubility of calcium hydroxide, there are disadvantages of low yield and high cost in actual production.
Aiming at the problems that the purity of the product obtained by the preparation method of the magnesium hydroxide flame retardant in the prior art is not high enough and the preparation cost is high, the present invention provides a method for preparing a magnesium hydroxide flame retardant with a sufficiently high purity of the obtained product and a magnesium hydroxide flame retardant with a sufficiently high purity and low preparation cost.
The present invention provides a method for preparing a magnesium hydroxide flame retardant and a magnesium hydroxide flame retardant prepared by the preparation method. The preparation method of the magnesium hydroxide flame retardant comprises the following steps: first, adding magnesium chloride to a reactor to form a magnesium chloride solution, and heating it to a set temperature T accordingly; then, adding a composite precipitant formed by mixing calcium oxide, magnesium oxide, sodium hydroxide and water to the reactor; then, after the composite precipitant is completely added, continuing the isothermal reaction at the set temperature T, and then washing and filtering the chloride ions in the reactor; further, re-slurrying the magnesium hydroxide filter cake; finally, physically crushing the re-slurryed magnesium hydroxide filter cake to obtain a magnesium hydroxide flame retardant. The purity of magnesium hydroxide in the magnesium hydroxide flame retardant prepared by the preparation method of the magnesium hydroxide flame retardant of the present invention is greater than or equal to 99.0%.