Hebei Messi Biology Co., Ltd. stated that it prepared and modified flaky magnesium oxide powder and used it as an inorganic filler. Through experimental and simulation research, the purpose is to improve the room temperature and high temperature energy storage density of PVDF-based and PEI-based composite materials. The paper makes a preliminary analysis of the reasons for the performance improvement. The main research contents are as follows.
Flake magnesium oxide powder was prepared by hydrothermal synthesis combined with calcination treatment. With the breakdown field strength of the composite material as the target, the single factor test method was used to optimize the optimal hydrothermal time and ammonia concentration for preparing flaky magnesium oxide powder, which were 24h and 20wt.%, respectively. The prepared magnesium oxide powder was flaky, with a lateral size of about 400nm and a thickness of about 40nm. When the powder addition amount was 2.8wt.%, the room temperature energy storage density of the prepared flaky magnesium oxide/PVDF composite material reached 16.9J/cm3, exceeding 80% of the PVDF matrix, indicating that flaky magnesium oxide helps to improve the material energy storage density. Taking PEI as the matrix, the effect of adding flake magnesium oxide powder on the energy storage density of PEI-based composite materials with temperature was studied. The results show that with the increase of temperature, the energy storage density of the composite material decreases. When the addition amount is 3.4wt.% magnesium oxide, the energy storage density of magnesium oxide/PEI composite materials at 25℃ and 150℃ is better, which are 5.54J/cm3 and 3.79J/cm3 respectively. Because magnesium oxide has poor compatibility with PEI matrix, the breakdown field strength decreases significantly with the increase of temperature.
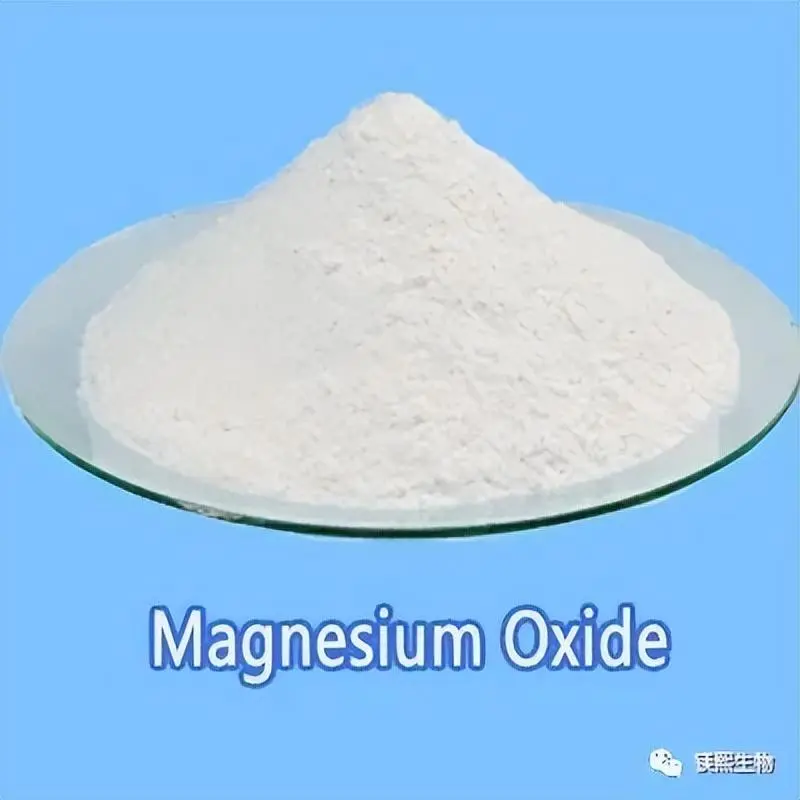
To this end, silane coupling agent KH550 was used to modify the surface of flaky magnesium oxide powder. The optimal content of the modifier was determined to be m(KH550):m(magnesium oxide)=3:100 by single factor test method. When the addition amount of modified flaky m-magnesium oxide was 3.0wt.%, the energy storage density of m-magnesium oxide/PEI composite materials at 25℃ and 150℃ could reach 6.10J/cm3 and 5.18J/cm3, which were 10% and 8% higher than those before modification, respectively. This shows that KH550 is an effective modifier for improving the energy storage density and temperature stability of magnesium oxide/PEI composite materials. The reason is that -NH2 and -OC2H5 of KH550 form hydrogen bonds with the hydroxyl groups on the surface of magnesium oxide and PEI molecules, respectively, which enhances the compatibility of organic and inorganic two-phase materials.
Finite element simulation method was used to visualize the electric field distribution inside the flaky magnesium oxide/PVDF composite material with the help of COMSOL multiphysics software. The influence of the amount and size of flaky magnesium oxide as well as its orientation and dispersion in the PVDF matrix on the electric field distribution inside the composite material was studied. The results show that with the increase of the amount of flaky magnesium oxide powder, the breakdown field strength of the flaky magnesium oxide/PVDF composite material increases first and then decreases, and there is an optimal amount of powder added; the larger the lateral size of the flaky magnesium oxide powder and the thinner the thickness, the stronger the high-voltage resistance of the composite material; when the flaky magnesium oxide filler is distributed parallel to the electric field direction, the high-voltage resistance of the composite material is weak; the more uniform the dispersion of the flaky magnesium oxide filler in the PVDF matrix, the better the high-voltage resistance of the composite material. The simulation conclusion confirms the experimental research results of the flaky magnesium oxide/PVDF composite material.