Hebei Messi Biology Co., Ltd. stated that a low-grade cobalt ore in the Democratic Republic of the Congo in Africa was used as raw material. The cobalt, manganese, iron, aluminum oxide and magnesium oxide contents of the low-grade cobalt ore were 0.26%, 0.51%, 1.73%, 6.37% and 5.54% respectively. The cobalt recovery rate of this method is >80%, and the cobalt content of the cobalt hydroxide product is >31%. In the industrial test of efficient recovery of cobalt from this low-grade cobalt ore, the following steps are included in sequence.
The first step is leaching: add water to adjust the ore to a pulp mass percentage concentration of 35%, then add concentrated sulfuric acid and a reducing agent, and react for 300 minutes under the conditions of a sulfuric acid mass concentration of 15g/l and a redox potential of 380mv to control the leaching process. After the reaction, solid-liquid separation is completed to obtain cobalt-containing liquid 1 and leached slag, which is sent to the slurry warehouse for storage.
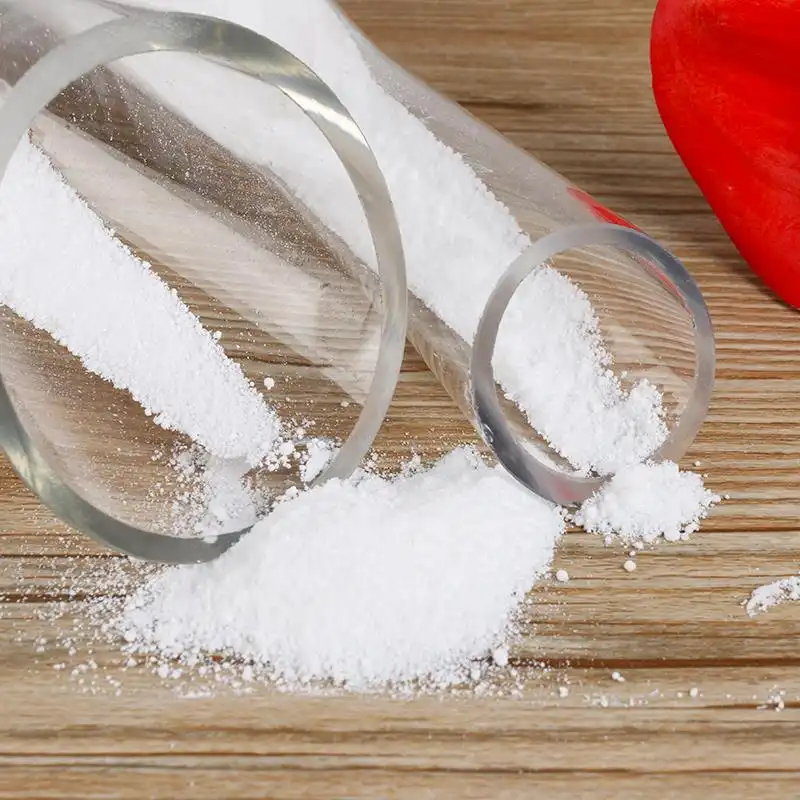
The second step is iron removal: add the subsequent second-stage cobalt precipitation slag to the cobalt-containing liquid 1, react for 30 minutes under air filling conditions, then add low-grade cobalt ore that is finely ground to -0.074mm and accounts for 80%, react for 60 minutes under air filling conditions, control the end point pH value of the iron removal reaction to 4.5, and the reaction is completed and solid-liquid separation is performed to obtain cobalt-containing liquid 2 and neutralization slag, and the neutralization slag is returned to the first step of leaching process.
The third step is manganese removal: add an oxidant to control the redox potential of the cobalt-containing liquid 2 at 1200mv, and the manganese removal reaction is performed for 90 minutes. After the reaction, solid-liquid separation is performed to obtain cobalt-containing liquid 3 and manganese removal slag, and the manganese removal slag is sent to the slag slurry storage for storage.
The fourth step is two-stage cobalt precipitation: one-stage cobalt precipitation, adding active magnesium oxide milk with a concentration of 8% to the cobalt-containing liquid 3, carrying out a first-stage cobalt precipitation reaction for 240 minutes under the condition of controlling the pH value to 8.10, and obtaining a cobalt hydroxide product and a cobalt precipitation liquid 1 after the reaction is completed by solid-liquid separation, and a second-stage cobalt precipitation, adding lime milk to the cobalt precipitation liquid 1, carrying out a second-stage cobalt precipitation reaction for 90 minutes under the condition of controlling the pH value to 8.50, and obtaining a second-stage cobalt precipitation slag and a cobalt precipitation liquid 2 after the reaction is completed by solid-liquid separation, and the second-stage cobalt precipitation slag is returned to the second step of the iron removal process, and the cobalt precipitation liquid 2 is discharged after being treated to meet the standards.