Hebei Messi Biology Co., Ltd. said that silicon steel grade magnesium oxide needs to meet the quality technical indicators of MgO>98%, CaO<0.5%, and Cl<0.02%. The impurity CaO will be hydrated into Ca(OH)2 in the slurry and then coated on the surface of the steel plate to absorb CO2 in the air to form CaCO3. When entering the annealing furnace, it is easy to increase the carbon content of the steel strip and cause the magnetic properties to deteriorate; Cl reacts with water at high temperature, and the HCl produced will seriously corrode the surface of the steel strip. In addition, metal impurities such as iron will affect the whiteness of magnesium oxide and product quality, and these harmful impurities need to be removed.
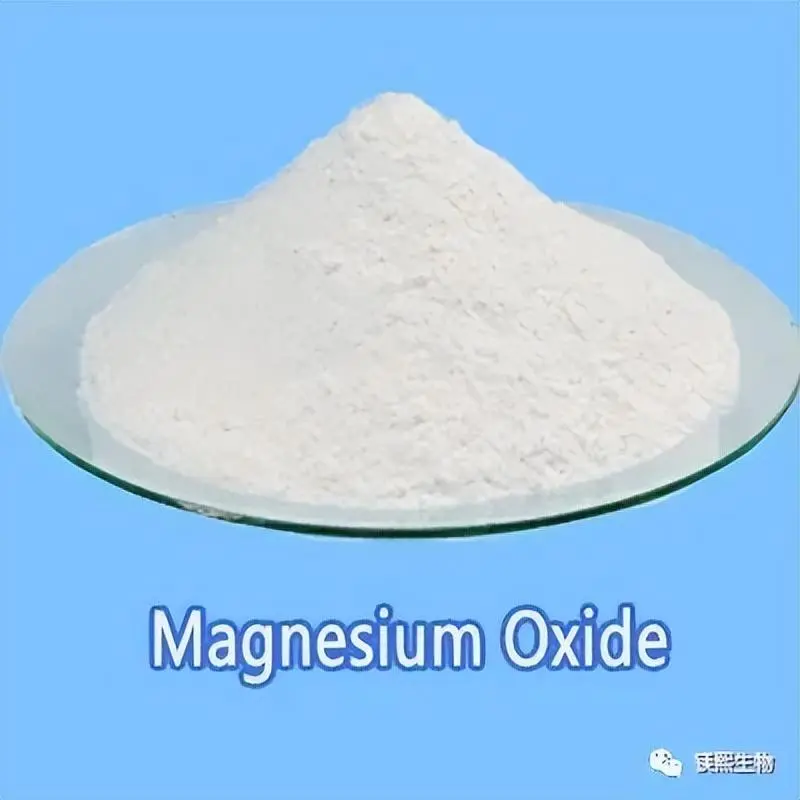
The removal of impurities in the process of preparing silicon steel grade magnesium oxide by carbonization was studied. Lightly burned magnesium oxide powder was used as the raw material, and heavy magnesium water was obtained by digestion and carbonization. The impurities calcium and iron in the heavy magnesium water were complexed and masked by a complexing agent, and then basic magnesium carbonate was obtained by pyrolysis. Magnesium oxide with low calcium and iron impurity content can be obtained by calcination. Studies have shown that the use of triethanolamine as a complexing agent alone, or oxalic acid and citric acid as complexing agents in combination, can form a stable complex between iron and calcium ions in heavy magnesium water, and no impurities are precipitated during the thermal decomposition of heavy magnesium water, thus achieving the purpose of purifying basic magnesium carbonate and magnesium oxide.
The impurities that are easily introduced when using brine as a raw material to prepare magnesium oxide are chloride ions, sulfate ions, carbonate ions, boron, silicates, alkali metals and heavy metal ions. In addition to chloride ions, other impurities can generally be removed by precipitation. First, CaCl2 solution is added to the brine to precipitate sulfate and carbonate ions into CaSO4 and CaCO3, and then the sulfate ions in the brine are further purified by adding an appropriate amount of barium chloride. Then, an appropriate amount of ammonia water is added to adjust the pH value of the solution, and a small amount of Mg (OH) 2 can be generated, a colloidal precipitate. The precipitate has a huge specific surface area and can adsorb and encapsulate various impurities such as Fe (OH) 3, Al (OH) 3, etc. At the same time, it may be isomorphously replaced by Fe, Ni, Mn and other ions to form a solid solution, which plays a role in purifying brine. The control of chloride ions in the product can be achieved by controlling the magnesium chloride content in the brine.
Studies have found that the initial concentration of the reactants has a great influence on the chloride ion content in the product. When the concentration of magnesium chloride is low, the product purity is high, which can reach more than 99%, while the content of impurities such as chloride ions and boron is very low. As the concentration of magnesium chloride increases, the purity of the product gradually decreases, and the impurity content increases, especially the Cl content. In actual production, the concentration of brine is more suitable to be 1~1.5mol/L.