Hebei Messi Biology Co., Ltd. stated that in order to solve the problem of high filling of magnesium hydroxide in polymer matrix leading to decreased mechanical properties of composite materials, the following two research schemes were proposed for the first time: Scheme 1: Magnesium hydroxide powder is first modified with vinyl silane A-172 to make it vinylized, and then vinyl acetate monomer is polymerized and grafted to magnesium hydroxide vinylized by silane. Scheme 2: First, silane-vinyl acetate copolymer is prepared and then used to modify magnesium hydroxide. Through direct and indirect characterization, the optimal process conditions were preliminarily determined, and the possible modification mechanism was explored. The specific experimental results are as follows:
(1) The most suitable modification process conditions for vinyl acetate grafted modified magnesium hydroxide powder: the dosage of silane coupling agent A-172 is 3wt%; the modification temperature is 80℃; the modification time is 60min; the molar ratio of silane to vinyl acetate is 3:1; the grafting modification temperature is 65℃; the grafting modification time is 5h. Under the modification process conditions, the tensile strength and elongation at break of the modified MH/EVA composite material reach 7.28MPa and 199% respectively.
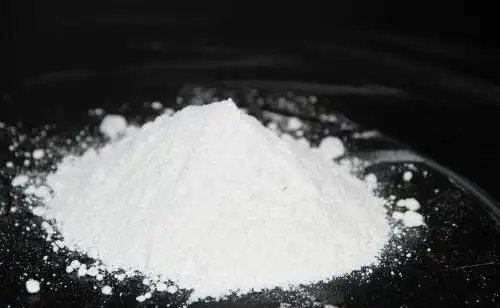
(2) The best modification process conditions for homemade silane-vinyl acetate copolymer modified magnesium hydroxide powder:
(a) Wet modification of silane-vinyl acetate copolymer: the molar ratio of silane to vinyl acetate is 3:1; the dosage of modifier is 3wt%; the modification temperature is 65℃; the modification time is 60min.
(b) Dry modification of silane-vinyl acetate copolymer (number average molecular weight = 1361): the molar ratio of silane to vinyl acetate is 3:1; the amount of copolymer is 3wt%; the modification time is 6min.
Under the above suitable wet modification process conditions, the tensile strength and elongation at break of the modified MH/EVA composite material reached 7.84MPa and 249% respectively; the tensile strength and elongation at break of the dry modified MH/EVA composite material reached 8.0MPa and 274% respectively, the tensile strength is equivalent to that of the American company’s products, and the elongation at break is 6.2% higher than that of the American company. The flame retardant grade of the vertical combustion test of the above modified MH/EVA composite material samples is V-0, which fully meets the requirements of industrial application.