Hebei Messi Biology Co., Ltd. stated that the metallization of alumina ceramics is mainly based on the activated Mo-Mn method. The activated Mo-Mn method is developed on the basis of the sintered metal powder (traditional Mo-Mn) method. Its essence is to add some activators that can form a glass phase during metallization, such as Al2O3, SiO2, MgO, CaO, BaO, porcelain powder, etc., to the Mo-Mn formula to expand the adaptability of the original Mo-Mn formula. At present, most units use the improved Mo-Mn formula, which mainly adds activators to the metallization formula to reduce the metallization temperature and obtain a higher metallization sealing strength. The main function of adding activators is to promote the generation of high-temperature liquid phase, that is, when the metallization temperature is reached, the activator becomes a liquid phase, part of it reacts with the ceramic component to form a liquid phase, and part of it reacts with the oxidized metal powder to form a liquid phase. These two situations generally occur at the same time. The generated liquid phases simultaneously infiltrate the metal powder and the ceramic surface, react with them, and form adhesion.
The activators in the metallization formula are Al2O3, SiO2, and MgO. The formula has been put into production for more than two years. The initial production conditions were good and the quality was relatively stable. However, there have been more and more quality problems with the cover after the first metallization recently. Therefore, this paper focuses on solving the outstanding problems in the first metallization process.
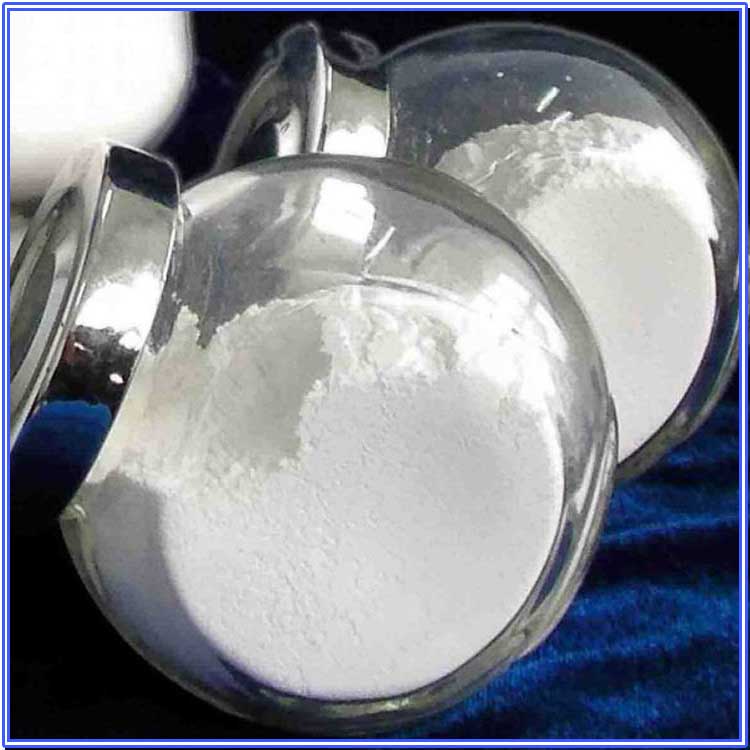
1. Problems after the first metallization sintering
(1) Serious cover spotting problem.
(2) A large number of cover bulges appear on the metallized surface after sintering, and some of the cover bulges fall off, resulting in porcelain exposure or peeling.
2. Cause analysis and test
2.1. Cover spotting problem
Analysis shows that there are two main reasons for the cover spotting: inaccurate powder ratio; changes in sintering process, that is, extending the heating time and insulation time and wet hydrogen temperature. Re-equip the powder and paste, and sinter without changing the existing sintering process. As a result, the cover spotting still exists. Sintering back to the original sintering process reduces the cover spotting, but it still exists.
A sample was selected and the speckled part of the cover was analyzed by spectroscopy. The conclusion was that in addition to the formula components, it contained trace amounts of Fe and Na. After analysis, it was believed that trace amounts of Fe and Na were not the cause of the cover speckles.
Only considering the change factor of magnesium oxide, two comparative tests were conducted: magnesium oxide (analytical purity) powder was selected to prepare metallized powder for metallization. Magnesium oxide in the original formula was removed for metallization. The conclusion was that the cover speckles still existed after sintering the formula containing magnesium oxide, and the cover speckles disappeared after removing magnesium oxide. It can be concluded that the direct cause of the cover speckles was magnesium oxide.
2.2. Cover bulges, porcelain exposure, and peeling
After experimental verification, the main reasons for the bulges were: ① The powder was damp, and the binder and powder were difficult to mix evenly; ② The sintering process heated up too quickly, resulting in the binder decomposing too quickly, generating bubbles and forming bulges; ③ The activator magnesium oxide was easy to agglomerate, resulting in uneven powder mixing, bulges or peeling after sintering.
3. Result analysis and solutions
Magnesium oxide is the direct cause of the cover mottling: ① The magnesium oxide is not fully mixed during the preparation of the paste, resulting in uneven dispersion of the glass phase of magnesium oxide during the sintering process; ② The temperature at which magnesium oxide forms the glass phase is low. Under the action of wet hydrogen, increasing the temperature or extending the insulation time will form more glass phases with lower viscosity, which diffuse to the surface of the metallized layer and form cover mottling.
Solution: Extend the mixing and grinding time of magnesium oxide, shorten the insulation time of metallized sintering, and reduce the wet hydrogen temperature.
Magnesium oxide is a major cause of cover bulges because magnesium oxide is stored for a long time and is not vacuum packed. It absorbs moisture in the air and reacts with CO2 to form basic magnesium carbonate, forming hard lumps that are difficult to grind and mix. In addition, magnesium oxide has a strong hydration ability, which increases with the decrease in particle size, and then lumps or powder forms, changing the formula ingredients and proportions. At the same time, it is difficult to apply the paste by hand and it is not easy to pull the pen. Especially in humid climates, it may also cause the metallized paste to freeze.
Solution: ① Reduce the one-time order quantity of magnesium oxide and shorten the storage period; ② Use anhydrous ethanol to wet-grind the mixed powder of aluminum oxide, SiO2 and magnesium oxide in proportion, pass through a 360-mesh sieve and dry to enhance the dispersibility of magnesium oxide; ③ Dry the metallized powder before preparing the paste to prevent the paste from agglomerating and difficult to mix and the paste from freezing.
4. Summary
Magnesium oxide is a common activator for medium-temperature metallization, which can effectively reduce the metallization sintering temperature, but there are the following problems in its metallization process:
(1) Magnesium oxide is easy to absorb moisture and deteriorate, resulting in inaccurate metallization formula ratio, agglomeration is difficult to grind, and it is not suitable for long-term storage after grinding.
(2) The prepared metallized powder is also easy to absorb moisture and agglomerate, resulting in difficulty in mixing the paste. The metallized cover printed or hand-painted has many quality problems, such as bulges, porcelain peeling, etc.
(3) As an activator, magnesium oxide has poor adaptability to the process and has high requirements for process conditions. It is prone to the problem of cover spots, which affects the bonding between the metallization layer and the nickel layer, thereby reducing the tensile strength of the seal.
(4) The preparation process of metallization powder is relatively complicated, which increases the labor of powder making and process equipment and containers. The quality of metallization powder is unstable and there are quality risks.
In short, the amount of magnesium oxide should be reduced during the metallization process. If it is used, the wet hydrogen temperature should be lowered and the insulation time of the high-temperature sintering zone should be shortened. The powder making, paste preparation and sintering processes should be well controlled to obtain stable metallization quality.