Hebei Messi Biology Co., Ltd. stated that the effect of magnesium oxide precipitation of cobalt under different conditions was studied for the neutralization and impurity removal of the copper raffinate containing cobalt in a local wet smelter in the Democratic Republic of the Congo. It was found that the best effect of using magnesium oxide slurry for cobalt precipitation was obtained at a temperature of about 50°C, a reaction time of 4h, and an end point pH value of 8.0. The grade of cobalt hydroxide obtained was higher than 36%, the cobalt recovery rate was greater than 99%, and the utilization rate of magnesium oxide could reach 91%.
The Zambia-Congo (Kinshasa) copper-cobalt ore belt in Africa is world-famous. It is the world’s third largest copper ore belt after the Andes Mountains in South America (Chile, Peru and Argentina) and the southwestern United States in North America-Mexico, and the cobalt reserves are highly concentrated in the Democratic Republic of the Congo, which is the world’s leader. At present, the copper ore mined and used in the Democratic Republic of Congo is mainly copper-cobalt polymetallic ore oxidized on the surface. Therefore, the production of copper mostly adopts wet process. In 2013, the wet smelting and sales output of the Democratic Republic of Congo has reached 940,000 tons. In recent years, with the further increase of investment in mining and metallurgical enterprises at home and abroad in the Democratic Republic of Congo, the output of wet copper smelting has a further substantial growth trend.
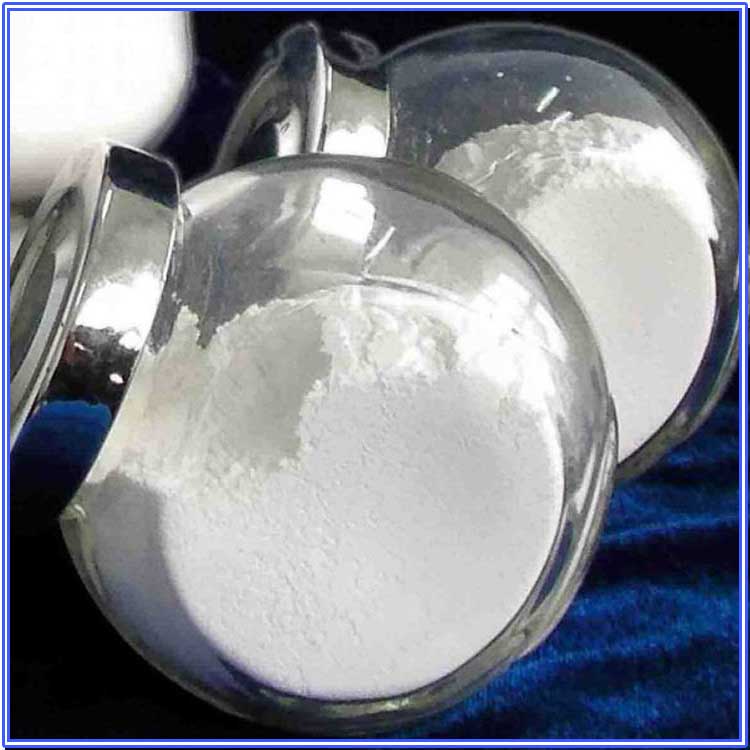
The wet production process of copper in the Democratic Republic of Congo is generally “ore leaching (heap leaching or stirring leaching)-extraction-electrodeposition”. In the process of leaching copper, sulfur dioxide or sodium sulfite is often used as a reducing agent to leach cobalt. The copper-cobalt-containing sulfuric acid solution is electrolytically produced after copper extraction to produce cathode copper, and the raffinate is neutralized and impurities are removed before cobalt precipitation.
Due to the very weak local industrial foundation in the Democratic Republic of Congo, except for some sulfuric acid, basically all auxiliary materials in the industry need to be imported. In order to save costs, the cobalt products produced locally are mostly made into phase-made cobalt compounds after simple impurities removal by the above process. The most common crude cobalt compound is to produce cobalt carbonate by using sodium carbonate to precipitate cobalt. However, the cobalt grade in crude carbonate diamond is low, mostly around 25%, which increases transportation costs and other expenses. In addition, the solution after sodium carbonate cobalt precipitation contains a large amount of sodium salt that is difficult to handle. Direct discharge will cause environmental pollution, and long-term circulation in the system will cause a large amount of sodium ions in the solution to be enriched, seriously affecting copper production. As the environmental protection policy for land extraction becomes increasingly stringent, many companies have begun to study more economical and environmentally friendly cobalt production processes, and magnesium oxide cobalt precipitation process is one of the directions.