Hebei Messi Biology Co., Ltd. stated that the positive electrode material of lithium-ion batteries is a layered structure. Lithium ions are between the oxygen ion and metal ion layers. The entire process of charging and discharging is formed during the lithium ion deintercalation and embedding process. A classic method of improving positive electrode materials is to use other cations, such as trivalent aluminum ions and divalent magnesium ions, to replace the lithium ion part. After the lithium ion is deintercalated, these inert cations still play a supporting role in the structure, so doping is mainly an improvement method to improve stability at the structural level.
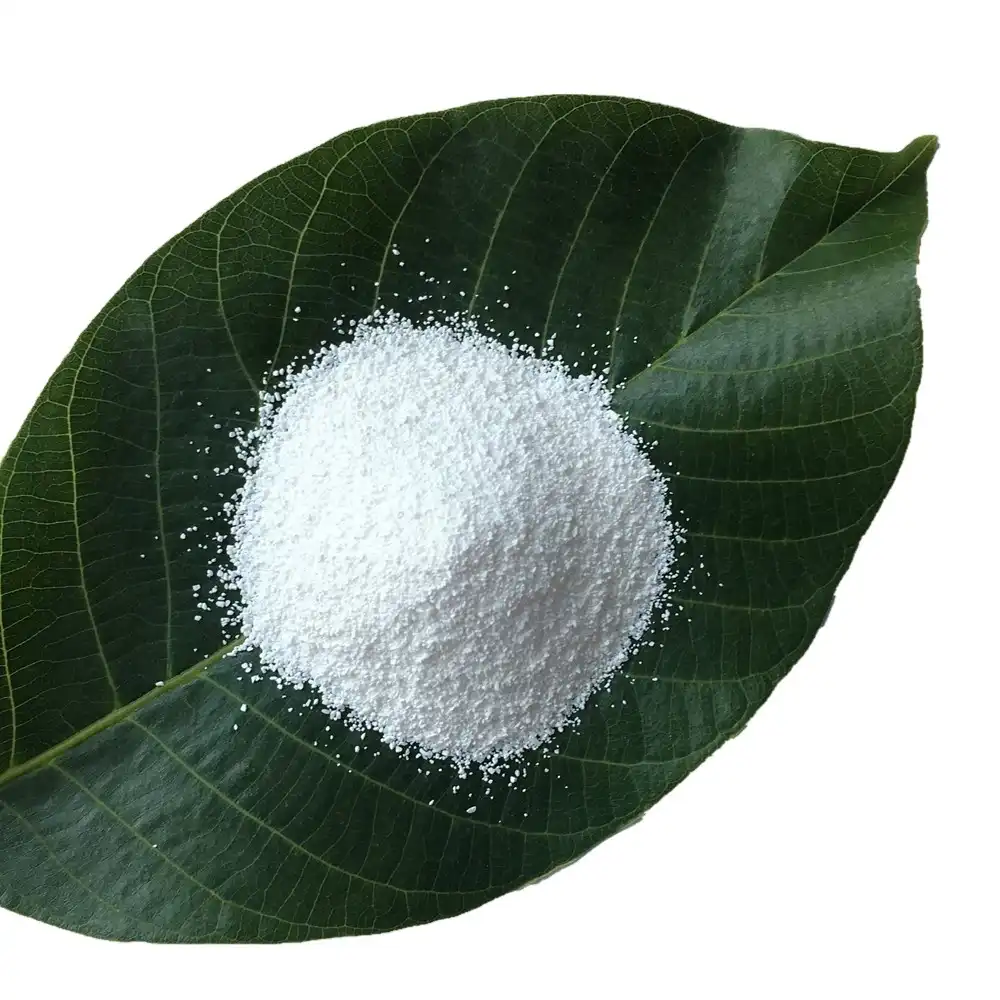
Another method is called coating. Before coating, the positive electrode material and the electrolyte will be in direct contact, because during the charging stage, the surface of the positive electrode material will exist at a high price. This high-valent cation will react with the organic solvent of the electrolyte or the side reaction of the electrolyte to form an irreversible SEI layer on the interface, resulting in increased impedance, loss of active lithium ions, and capacity attenuation.
If a layer of inert oxide is coated on the surface of the positive electrode, such as common aluminum oxide, zirconium oxide or magnesium oxide, the direct contact between the positive electrode material and the electrolyte can be isolated, reducing the increase in interface impedance. There are different ways to carry out coating in traditional technology. The simplest one is called dry coating, which is more popular in medium and low nickel materials. Some inert oxides, such as the aluminum oxide, magnesium oxide, and zirconium oxide mentioned above, are mixed with the positive electrode material, and then sintered at a low temperature between 300°C and 500°C to obtain a discontinuous coating structure on the surface. This coating effect is not particularly good and does not achieve complete coating.