Hebei Messi Biology Co., Ltd. said that adding magnesium oxide during mixing can play a stabilizing role, prevent scorch during processing, and improve the scorch of the rubber material during storage, and also improves the scorch during plasticizing. It has the function of plasticizing rubber.
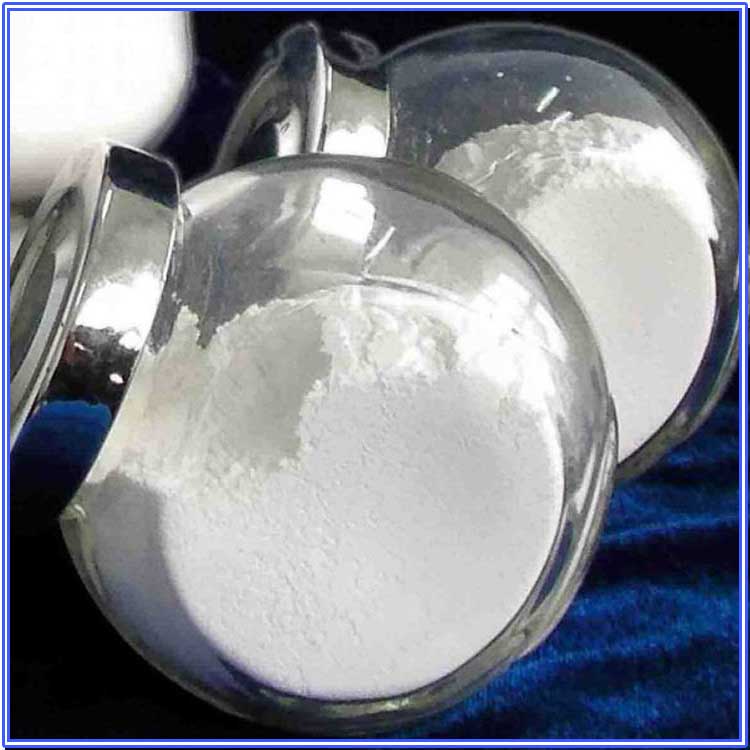
Adding magnesium oxide to the rubber at the beginning of mixing can prevent early cross-linking and cyclization of chloroprene and increase operational safety. During vulcanization, it becomes a vulcanizing machine, which acts as a hydrogen chloride acceptor, improves the concentration of the rubber material, and prevents hydrogen chloride from eroding the fiber tissue. Magnesium oxide can increase the setting stress of the rubber compound, improve heat and aging resistance, but lead to a decrease in elongation. The quality of magnesium oxide has a great influence on the processing and vulcanization of neoprene. When the amount of magnesium oxide is increased to 10 parts, the vulcanized rubber can have higher plasticity and better storage stability, but it can reduce the vulcanization speed.
Zinc oxide is mainly used as vulcanized rubber to make the vulcanization smooth. Although increasing the amount of zinc oxide can improve the heat resistance and aging resistance, the rubber is prone to scorch and reduces the storage stability of the rubber. Extensive use can also cause the rubber to harden and lose its plasticity. But it can increase the vulcanization speed, and also improve the degree of vulcanization and high temperature resistance. Hebei Xintao New Material Technology Co., Ltd. stated that generally magnesium oxide and zinc oxide are used at the same time, which solves the problem of easy scorching of vulcanized rubber, high degree of vulcanization and fast vulcanization speed, and the degree of cross-linking is much higher than when used alone.