Hebei Messi Biology Co., Ltd. stated that polypropylene (PP) is a general-purpose plastic widely used at home and abroad, but polypropylene is easy to become brittle at low temperatures, is sensitive to notches, has a large molding shrinkage rate, and is easy to age, so it cannot be used as a structural material, which limits its application. Therefore, it is usually necessary to modify polypropylene through copolymerization, blending, filling, and reinforcement technologies to improve its performance. Among them, the filling and reinforcement modification of polypropylene is currently the most promising and widely used modification method.
From the perspective of filling mineral powder fillers to reinforce polypropylene, ultrafine (micro-nano) magnesium carbonate trihydrate, basic magnesium carbonate, anhydrous magnesium carbonate and other magnesium carbonate powders have many advantages such as light weight, low density, high thermal stability, flame retardant and smoke suppression, non-toxic and pollution-free, a wide range of raw material sources for preparation, and low price. It is an important new type of environmental mineral material. It has been proved in practice that magnesium carbonate filler can be used as a reinforcing agent, filler and flame retardant for high polymers such as plastics, coatings, and building materials. It can increase volume and reduce costs. It has wide application value in many fields such as plastics, rubber, coatings, medicine, food, separation and metallurgy.
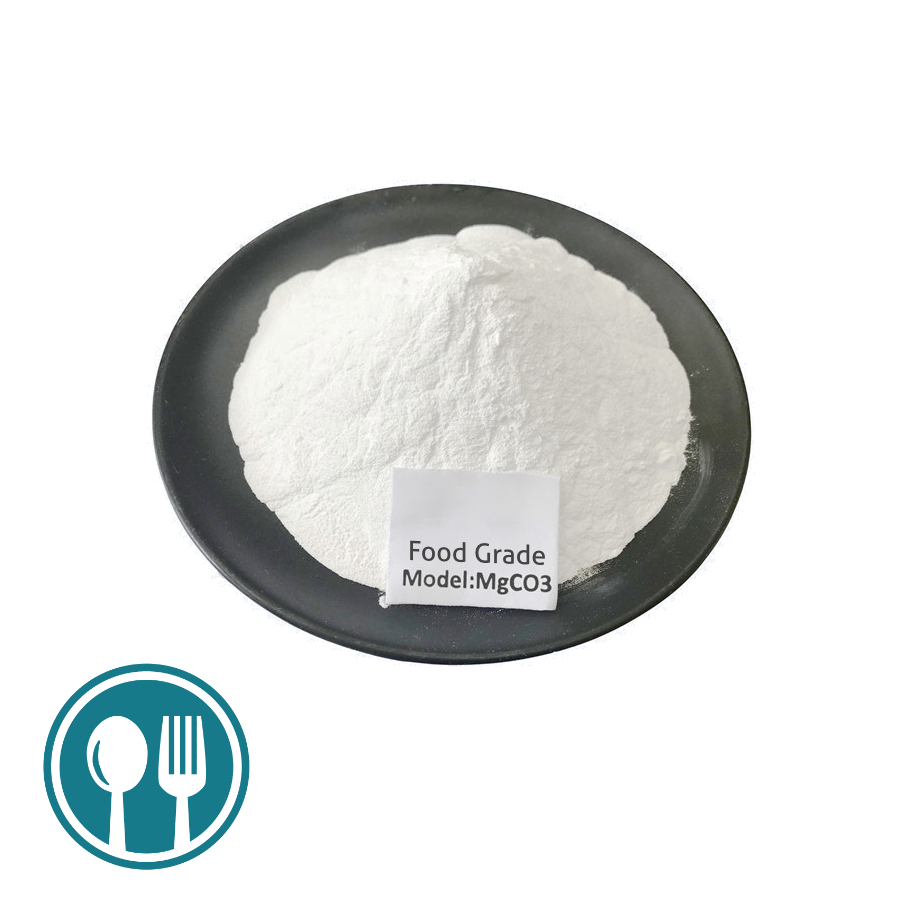
1. Micro/nano hydrated magnesium carbonate
Micro/nano hydrated magnesium carbonate, with a molecular formula of 3MgCO3·Mg(OH)2·3H2O and a white powder appearance, is a new type of high-function fine inorganic material born with the development of nanomaterials. Because the modified hydrated magnesium carbonate has thermal, optical, electrical, mechanical and chemical properties different from those of the main material, it is widely used in rubber, coatings, plastics, papermaking, food, medicine and other fields.
2. Magnesium carbonate modification
Inorganic powders such as magnesium carbonate have more surface atoms, higher surface energy and stronger polarity. Their surface properties are quite different from those of non-polar or weakly polar organic polymers, and the two have poor compatibility. Therefore, when they are directly used as fillers for polymers, it is easy to cause the mechanical processing properties of composite materials, such as impact strength and elongation, to decrease. Therefore, the filler must be surface modified to improve its physical properties and enhance its compatibility with the organic matrix, thereby broadening its application range.
There are four main theories on the surface modification of inorganic powders: chemical bond theory, surface wetting theory, deformable layer theory and constrained layer theory.
(1) The chemical bond theory believes that the coupling agent contains two chemical functional groups, one of which can form chemical bonds with the surface protons of the filler and the other can bond with the polymer molecules, resulting in a stronger interface bond and improving the mechanical properties of the filled composite material.
(2) The surface wetting theory believes that the good wettability of the polymer matrix to the filler has a significant impact on the performance of the composite material. If the filler can be completely infiltrated, the physical adsorption of the resin on the high-energy surface will provide a bonding strength higher than the cohesive strength of the organic resin.
(3) The deformable layer theory believes that the surface of the filler modified by the coupling agent may preferentially become a complexing agent in the adsorbed resin. The uneven curing of the interphase region may lead to a flexible resin layer that is much thicker than the monomolecular layer of the coupling agent between the polymer and the filler, namely the deformable layer. It can relax the interfacial stress and prevent the expansion of the interfacial cracks, thereby improving the bonding strength of the interface.
(4) The constrained layer theory believes that in the interfacial region between the high modulus powder and the low modulus resin, if its modulus is between the two, the stress can be transmitted most evenly.
3. Application of modified magnesium carbonate in polypropylene (PP)
(1) Toughening of polypropylene (PP)/light magnesium carbonate composites
Polypropylene (PP)/light magnesium carbonate composites were prepared by melt blending. The study found that after the two were compounded, the crystallinity of the composite system decreased, the impact strength decreased, and β spherulites were produced, which enhanced the toughness of the composite system.
(2) Aluminum hydroxide and magnesium carbonate compound for polyethylene flame retardant materials
Adding aluminum hydroxide and magnesium carbonate compound to linear low-density polyethylene widens the flame retardant temperature range of the system. When the addition amount is 50% and the ratio of aluminum hydroxide to magnesium carbonate is 4:1, the oxygen index of the system is 26, which is better than the case of using aluminum hydroxide alone.
In addition, the decomposition temperature of basic magnesium carbonate is 200~550℃, which is larger than the decomposition temperature range of iron hydroxide and aluminum hydroxide. When the composite material burns, basic magnesium carbonate can decompose and absorb heat, releasing crystal water and CO2, preventing combustion.