Hebei Messi Biology Co., Ltd. stated that magnesium hydroxide has excellent flame retardant, filling, and smoke suppression functions, and is non-toxic and non-corrosive. It can produce synergistic flame retardant effects with other flame retardants. It has become the most important inorganic flame retardant and is applied to various materials and various fields.
As a flame retardant, magnesium hydroxide is often added in an amount of more than half of the total amount of the composite material to have a significant flame retardant effect. Moreover, it is an inorganic material, which is very different from organic polymers in physical and chemical form. The affinity between the two is very poor. If magnesium hydroxide is directly filled, uneven particle size will form stress collection points, causing composite interface defects. When the amount added is large, it will affect the mechanical properties of the composite material. Therefore, nano- and ultra-fine magnesium hydroxide particle size is an effective way to solve this problem, which can improve the problem of excessive addition in polymers.
But at the same time, it is a polar inorganic material with hydrophobic and lipophilic properties. It has poor compatibility with organic polymers. After ultrafine processing, its particle size is small, the surface energy is high, and it is easy to produce particle agglomeration, which affects its dispersibility in composite materials. For this reason, it can be surface modified by surfactant treatment or coupling agent modification, so that the obtained organic polymer composite material has both good flame retardant properties and excellent mechanical properties.
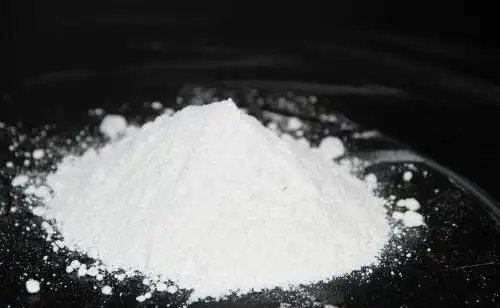
Modification mechanism of magnesium hydroxide
The surface modification of magnesium hydroxide refers to the adsorption or coating of another one or more substances on its surface to form a complex with a core-shell structure. Its surface modification is mainly manifested as organic modification, and the modification methods can be divided into two categories. The physical method refers to the use of surfactants such as higher fatty acids, alcohols, amines, esters, etc. to coat the surface to increase the particle spacing, hinder the agglomeration between particles, and at the same time improve the affinity between magnesium hydroxide and organic polymers, increase flame retardant properties, improve processing technology, and further improve the impact resistance of organic polymers. The chemical law refers to the use of coupling agents to modify the surface of magnesium hydroxide, and the modification effect is achieved by reacting the groups of its molecules with the surface of the modified powder to form chemical bonds. Since the coupling agent molecules have an affinity for organic matter, they can react with organic polymers, making them tightly combined with organic polymers, thereby improving the performance of the composite material.
How to perform surface modification
01 Surface modifiers
- (1) Surfactants
Common modifiers of this type include sodium dodecylbenzene sulfonate, sodium stearate and silicone oil. The modification mechanism is that the polar group at one end of the molecule reacts chemically or physically adsorbs with the inorganic material and is coated on its surface, while the other end of the molecule is a long-chain alkyl group that has a similar structure to the polymer and has extremely strong compatibility.
- (2) Coupling agent
The modification mechanism of the coupling agent is that part of the functional groups in its molecules are chemically combined with ultrafine inorganic materials. In addition, some carbon chains are combined with polymer materials in a physical or chemical way, so that inorganic materials and organic polymer materials are closely connected. Common coupling agents are as follows:
Silane coupling agents can be represented by the general formula Y-R-Si-X3, where X is a group that can undergo hydrolysis and generate silanol (-OH), Y is a group that can react with organic polymers, and R is a carbon bond that can connect Y to Si. Its modification mechanism is to form microcapsules to encapsulate magnesium hydroxide, which can be applied to polyolefin matrices with less polarity.
Titanate coupling agents can be divided into four categories: monoalkoxy type, chelate type, pyrophosphorus type and coordination type, which can be represented by the general formula (RO)MTi-(OX-R1-Y)N, where (RO)M represents the group coupled with inorganic fillers and pigments, 1≤M≤4; N is the number of non-hydrolyzable groups, M+N≤6; X represents the group connecting the titanium center, generally N, S, C, P and other elements; R1 is a long-chain alkane group; Y is a reactive group such as amino, hydroxyl, double chain and epoxy.
Aluminate coupling agent, a new type of coupling agent that can be represented by the general formula (RO)X-AL(-Dn)-(OCOR1)m, where RO represents the group that reacts with inorganic powders; Dn represents the coordination group, such as O, N, etc.; COR1 is the group that reacts with organic polymers.
Stearic acid, whose structural formula can be expressed as CH3(CH2)16COOH, has a hydrocarbon group and a long-chain alkyl group at both ends of the molecule. It is widely used because of its convenience and low capital.
02 Modification method
At present, the surface modification is mainly carried out by dry modification and wet modification. The dry modification is characterized by placing the powder raw material and the modifier or dispersant into a specific device, adjusting the appropriate speed for stirring and mixing, and coating the modifier on the surface of the magnesium hydroxide powder. This method is suitable for mass production. Wet modification refers to the method of adding the modifier to the magnesium hydroxide slurry with a certain liquid-solid ratio prepared in advance, and fully stirring and dispersing it at a certain temperature for modification. This method is characterized by complex operation, but the surface coating is uniform and the modification effect is good.