1. Brine-lime method
Preliminary purified and refined brine and lime milk made from digested and deslagging lime are precipitated in a sedimentation tank, and flocculants are added to the obtained slurry. After sufficient mixing, the slurry is separated in a sedimentation tank, and then filtered, washed, dried, and crushed to obtain the finished magnesium oxide.
2. Brine-ammonia method
Use brine that has been purified to remove sulfate, carbon dioxide, a small amount of boron and other impurities as raw material, and ammonia as a precipitant to carry out precipitation reaction in a reactor. A certain amount of seed crystals are added before the reaction and stirred thoroughly. The ratio of brine to ammonia is 1: (0.9-0.93), and the temperature is controlled at 40°C. After the reaction is completed, a flocculant is added, and the precipitate is filtered, washed, dried, and crushed to obtain the finished magnesium oxide. This test method needs to improve the yield, shorten the washing cycle, and improve and perfect the production process.
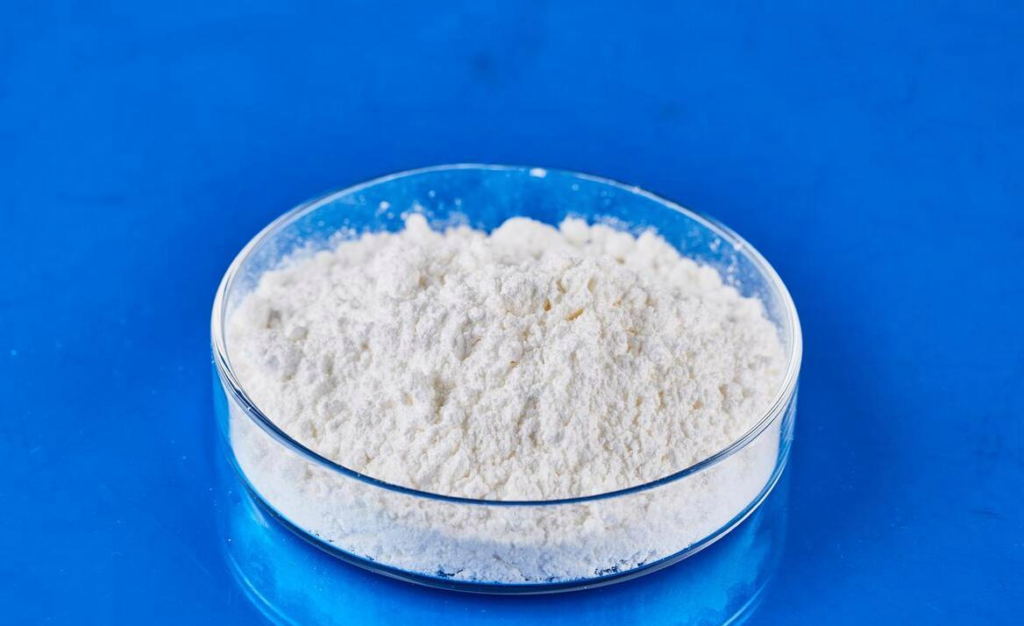
3. Magnesium-hydrochloric acid-ammonia method
Magnesium ore and anthracite or coke are calcined in a vertical kiln to produce magnesium oxide and carbon dioxide. Magnesium powder is mixed with water to form a slurry and reacted with hydrochloric acid of a specified concentration to prepare a magnesium chloride solution. The magnesium chloride solution reacts with a certain concentration of ammonia in a reactor, and the product is washed, settled, filtered, separated, dried, and crushed to obtain a magnesium oxide product. A surface treatment agent can be added for surface treatment as needed.
4. Microcrystalline magnesium oxide
Prepare a saturated MgCl2·6H2O solution at room temperature, and pass an excess of concentrated ammonia at 70°C under stirring, and magnesium oxide slowly precipitates.
Note 1: The distilled water and ammonia used must not contain CO2. The distilled water must be fully boiled, and the CO2 in NH3 must be removed by KOH. Device for preparing magnesium oxide Note 2: The reaction container should be made of hard glass to avoid the reaction of Mg(OH)2 with silicic acid. The obtained precipitate is allowed to stand in the mother liquor for two days, during which it can be heated several times, each time to 70°C, and then the precipitate is decanted and washed. Then it is placed in a nickel beaker coated with paraffin and centrifuged and washed with distilled water without CO2. The precipitation and decanting operations can be carried out in the device, and the obtained magnesium oxide is first vacuum dried on potassium oxide and then vacuum dried on phosphorus pentoxide.
5. Large-grained magnesium oxide.
Add 243mL of water to a wide-mouthed platinum container, then add 1375g of KOH and 485g of MgCl2·6H2O, heat to 210°C on an electric furnace, and clarify after about half an hour. Then slowly cool it to room temperature within 18h, that is, crystals with a diameter of about 0.2mL are precipitated, and dried at 100°C for 2h to obtain large-grained magnesium oxide.