Hebei Messi Biology Co., Ltd.. stated that cobalt, nickel and magnesium often coexist in the sulfuric acid leaching solution of nickel oxide ore. The saponification P507 process is usually used to separate cobalt and nickel. This process has problems such as the introduction of impurity ions, long process flow and wastewater discharge. The magnesium oxide precipitation method is used to separate cobalt, nickel and magnesium from the sulfuric acid solution, and then the P507-N235 saponification-free extraction system is used to separate cobalt and nickel. The influencing factors and process conditions of cobalt, nickel and magnesium precipitation separation and cobalt and nickel extraction separation are studied, as well as the cobalt and nickel precipitation mechanism, magnesium oxide recovery and water phase loss during the extraction process, and the extraction and separation effects of cobalt and nickel by the P507-N235 system and the sodium saponification P507 system are compared.
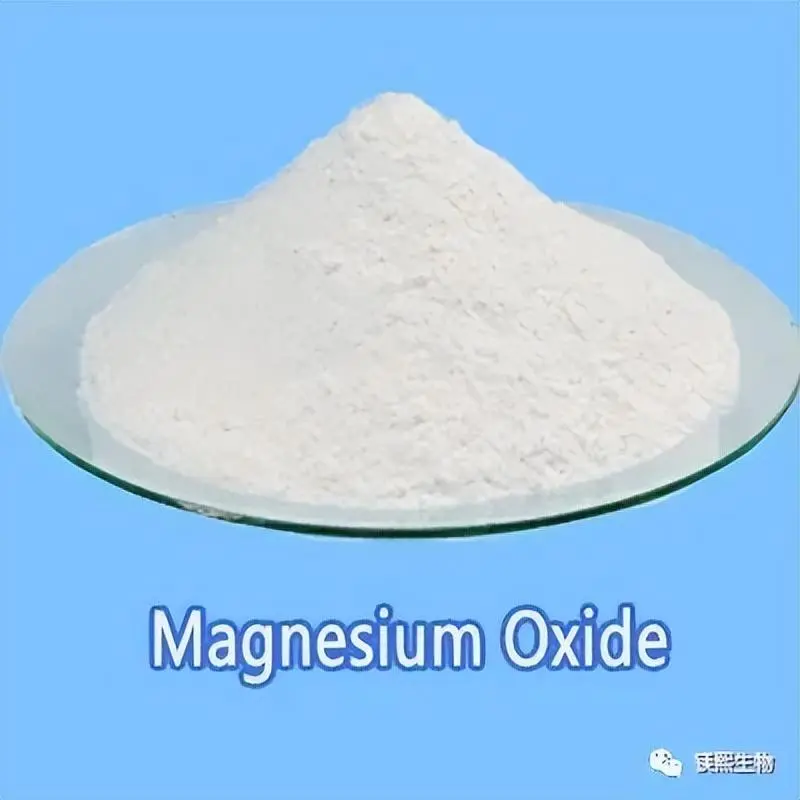
The main research contents and results of the full text are as follows:
(1) The sodium saponification P507 system separates cobalt and nickel. Compared with O/A=2:1, the phase separation effect is better, but cobalt and nickel are almost completely extracted, and it is difficult to separate cobalt and nickel; when O/A decreases from 2:1 to 1:30, the extraction rates of cobalt and nickel both decrease, but the nickel extraction rate decreases more significantly, so β(Co/Ni) gradually increases; under O/A≤1:1, the extraction phase separation time is longer, all greater than 1h. Compared with O/A of 1:30, β(Co/Ni) is 119.6, which can achieve the preliminary separation of cobalt and nickel; the loaded organic phase is washed with 0.05mol/L sulfuric acid at O/A of 3:1 for three stages, and the co-extracted nickel can be completely washed off; the washed loaded organic phase is stripped with 0.25mol/L sulfuric acid at O/A of 2:1 for two stages, and the cobalt can be stripped completely. The extraction rates of cobalt and nickel decreased with the increase of Mg2+ concentration in the feed solution. The sodium saponification P507 system separated cobalt, nickel and magnesium. The extraction rates of cobalt, nickel and magnesium decreased with the decrease of O/A, but the extraction rates of nickel and magnesium decreased greatly, so β(Co/Ni) and β(Co/Mg) gradually increased.
(2) The extraction rate of cobalt increased with the increase of feed solution pH value, but the increase gradually decreased, while the increase of nickel was smaller. With the increase of O/A, the extraction rates of cobalt and nickel increased gradually, but the increase of cobalt extraction rate was greater than that of nickel extraction rate. The equilibrium pH value of the aqueous phase increased first and then remained almost unchanged with the increase of feed solution pH, but did not change with the change of O/A. With the increase of organic phase P507 dosage (the amount of kerosene decreased accordingly), the cobalt extraction first increased gradually and then decreased, and the nickel extraction rate increased slowly. The extraction separation time was prolonged with the increase of P507 dosage and O/A, and was prolonged first and then shortened with the increase of N235 dosage. In sulfuric acid medium, N235 does not participate in the extraction reaction of Co and Ni, but can extract H+ released by P507 and the original H+ in sulfuric acid medium, so N235 can be used to adjust the acidity of the aqueous phase. The loss of aqueous phase in the extraction process increases with the decrease of the initial pH value of the feed liquid, the increase of O/A and the amount of N235, but the influence of the amount of N235 is relatively large.
The suitable conditions for the separation of cobalt and nickel in the P507-N235 system are: the initial pH of the feed liquid phase is 4.6, the phase O/A is 2:1, the organic phase composition is P507 30%, N235 15%, and sulfonated kerosene is 55%. The extraction rate of cobalt in the first stage is 41.5%, that of nickel is 1.6%, and the separation coefficient β (Co/Ni) is 42.53. After five-stage cross-current extraction, the extraction rate of cobalt reaches 97.1%, and that of nickel is 15.9%. Water was used as the washing solvent for the organic phase, O/A was 4:1, and the washing time was 2 min. After two-stage washing, nickel could be completely washed, and the loss rate of Co was 2.45%. 0.05 mol/L sulfuric acid was used as the stripping solvent for the organic phase, O/A was 2:1, and the stripping time was 5 min. After two-stage stripping, the cobalt stripping rate was close to 100%. The E-pH curve of the P507-N235 system was different from that of the saponified P507 system. The cobalt extraction rate of the P507-N235 system was high in the equilibrium pH range of 4-4.8, and the cobalt extraction rate did not increase but decreased after the equilibrium pH was 4.6. The pH range with high nickel extraction rate was above pH 4.9. The cobalt extraction rate and cobalt-nickel separation coefficient β(Co/Ni) of the P507-N235 system were lower than those of the saponified P507 system, but the extraction phase separation time was shorter, and the acidity required for washing and stripping was lower. Magnesium has a significant effect on the separation of cobalt and nickel in the P507-N235 system. In order to avoid the influence of Mg2+ on the separation of cobalt and nickel, the concentration of Mg2+ in the feed solution should be controlled to be no more than 0.1g/L.
(3) The magnesium oxide precipitation method recovers cobalt and nickel from the sulfuric acid solution containing cobalt, nickel and magnesium. The equilibrium pH, magnesium oxide dosage and temperature are the main influencing factors. Increasing the temperature and reducing the magnesium oxide dosage can reduce the magnesium content in the precipitated product. The suitable conditions for the separation of cobalt, nickel and magnesium are: magnesium oxide dosage nMgO: (nNi + nCo) is 2.0, reaction time is 2h, reaction temperature is 60℃, stirring speed is 300rpm. Under these conditions, the cobalt precipitation rate is 99.5%, the nickel precipitation rate is 97.2%, and the magnesium precipitation rate is 0.2%. The equilibrium pH of the solution after the reaction is 8.9.
(4) The recovery of cobalt and nickel by magnesium oxide precipitation may involve two types of reactions, namely, the reaction of magnesium oxide with hydrogen ions in the solution and the hydrolysis reaction of metal ions; the higher the equilibrium pH (the more magnesium oxide is used), the more magnesium oxide is entrained in the precipitation product. The cobalt-nickel precipitate can be dissolved with 0.05 mol/L sulfuric acid, and the pH value of the resulting solution is 4.7, with metal ion content: Co0.11 g/L, Ni0.99 g/L, Mg5.2 mg/L. The sulfuric acid leaching solution of the cobalt-nickel precipitate can be extracted and separated from cobalt and nickel using the P507-N235 system (composition P507 30%, N235 15%, sulfonated kerosene 55%), and the separation effect is the same as that of the cobalt-nickel solution without magnesium. Therefore, the magnesium oxide precipitation method and the P507-N235 system can be used to separate cobalt, nickel and magnesium from the sulfuric acid solution. The process is pollution-free, with less loss of cobalt and nickel, no consumption of alkali solution and no wastewater discharge.