Hebei Messi Biology Co., Ltd. stated that the world’s nickel reserves are estimated to be 57 million tons, of which more than 80% are distributed in Cuba, Canada, the former Soviet Union, South Africa, Greece, Australia, New Caledonia, the Philippines, Yugoslavia, Brazil, China and the Dominican Republic.
Nickel and cobalt are generally obtained by processing sulfide and laterite ore concentrates using hydrometallurgical processes. The nickel matte obtained by roasting and smelting is further cleaned by electrometallurgical, steam and hydrometallurgical refining methods. A portion of the rough surface is baked to obtain commercial nickel oxide agglomerates. 99.9% pure nickel can be obtained by electrolytic refining process. The purest nickel (99.97%) is obtained by gas phase metallurgy. In this process, also known as the Mond process, a mixture of nickel and copper sulfide is converted into oxides and then reduced by heating with water vapor at 350–400°C. The obtained nickel active form is treated with carbon monoxide to obtain volatile nickel carbonyl [Ni (CO) 4]. The latter reaction is reversible. Heating produces pure nickel and carbon monoxide.
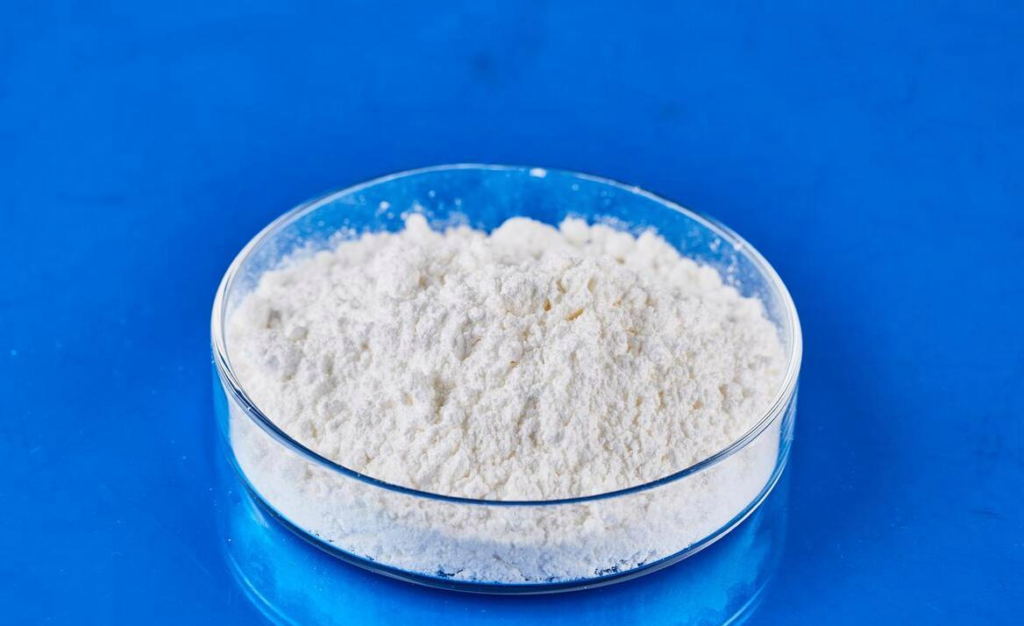
The method for selectively extracting nickel, cobalt and iron from laterite nickel ore comprises: crushing the laterite nickel ore, adding sodium fluoride and water and mixing them thoroughly to obtain a mixture; spraying concentrated sulfuric acid into the mixture and activating it under autothermal conditions to obtain an activated material; subjecting the activated material to atmospheric pressure water leaching to obtain a leached slurry; subjecting the leached slurry to dense separation to obtain a leaching solution and a leaching residue; washing the leaching residue to obtain iron slag; neutralizing the leaching solution with magnesium oxide to precipitate nickel and cobalt to obtain a neutralized separation solution and nickel and cobalt hydroxides; subjecting the neutralized separation solution to precipitation defluorination and evaporation crystallization in sequence to recover magnesium sulfate. The present invention can realize the efficient selective leaching of nickel and cobalt under mild conditions without external heating and pressurization, and the leaching rate can reach more than 90%, while the leaching rate of iron is as low as less than 1%. Therefore, the present invention well realizes the efficient selective separation of nickel, cobalt and iron in laterite nickel ore.