Hebei Messi Biology Co., Ltd. stated that adding magnesium carbonate to lithium batteries can improve the conductivity of the battery, prolong the service life of the battery, slow down the self-discharge of the battery, improve the storage performance, and increase the utilization rate of the active material of the battery. However, the performance of battery materials has a great relationship with the purity and fineness of magnesium carbonate, especially the content of magnetic substances such as iron, chromium and nickel in magnesium carbonate.
At present, the main method of preparing magnesium carbonate is “dolomite carbonization method”. The calcination process during the production of dolomite carbonization method needs to calcinate the ore to 900-1000°C, which consumes a lot of coal or natural gas, and the energy consumption is very large. Conducive to saving production costs. Moreover, the gas produced by calcination brings out a large amount of dust, not only the production environment is bad, but also the working environment cannot be guaranteed, which affects the health of employees. At the same time, it is difficult to produce high-purity and ultra-fine magnesium carbonate powder by dolomite carbonization, so it is difficult to improve the performance of battery materials.

The invention discloses a method for preparing high-purity ultrafine magnesium carbonate for battery materials, belonging to the technical field of magnesium carbonate preparation. The present invention first removes impurities in the ferromagnetic material in the raw material for the first time, which can remove the ferromagnetic impurities with larger particles in the raw material. The ferromagnetic impurities are removed to the greatest extent in the suspended state, and finally the third impurity removal is carried out after crushing, which can remove only a small amount of ferromagnetic impurities in the powder. Through these three impurity removal methods, the magnesium carbonate product can be effectively controlled. The content of magnetic substances in the battery can meet the requirements for preparing batteries; and through the reaction of the suspension, the original calcination process is replaced, so that the energy consumption in the entire preparation process is greatly reduced, which is conducive to saving production costs.
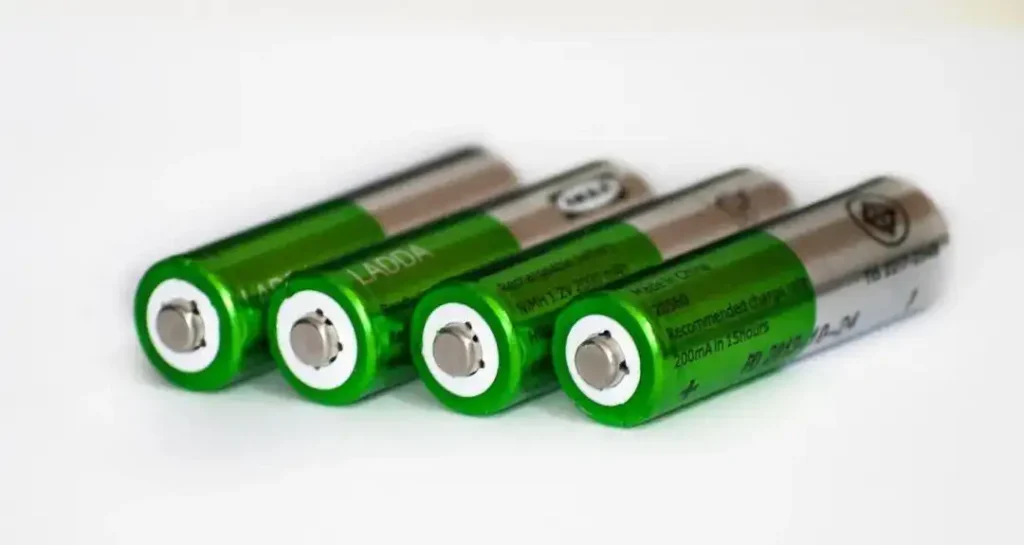
Include the following steps:
A. Grinding the raw material magnesium hydroxide or magnesium oxide, and sieving the first powder whose particle size is less than 5 μm;
B. Mix the first powder with water and stir to prepare a suspension, and further remove ferromagnetic impurities through a grid-type iron remover to form the first reaction liquid;
C. Introduce carbon dioxide into the first reaction liquid, turn on heating and stirring to form the second reaction liquid, and remove the ferromagnetic substances in the second reaction liquid through the grid type iron remover again, and then continue to introduce carbon dioxide And stirring, until the pH of the solution is constant, the third reaction solution is obtained;
D. Dehydrating and drying the third reaction liquid to obtain a filtrate, pulverizing the filtrate, and sieving the second powder with a particle size of no more than 10 μm;
E. Pass the second powder through a strong magnetic field to remove the ferromagnetic substance therein to obtain high-purity magnesium carbonate powder.