Hebei Messi Biology Co., Ltd. stated that magnesium oxide tablets are used in many aspects as medical laxatives and mineral supplements. Generally, tablets are manufactured by compressing raw material into a tablet shape. The process of performing this compression molding is called a tableting process. In the tableting process, the compression operation is performed continuously and at high speed. Under such conditions, the pressure and density will disperse inside the tablet, resulting in uneven internal structure, easy cracking, delamination, and gray and black edges. In particular, white tablets with a magnesium oxide ratio higher than 80% are more prone to tablet delamination and gray and black edges. In view of the above situation, it is hoped to develop a food-grade granular magnesium oxide product that can be suitable for medicine or food additives, has high purity, and can reduce tablet compression problems and abnormal quality characteristics of tablets.
In order to solve the existing problems in the prior art in the tableting process of granular magnesium oxide, a food-grade granular magnesium oxide for tableting and its preparation method are provided, so that the obtained magnesium oxide particles have moderate hardness and particle size distribution. Good, a preparation method of magnesium oxide particles for white tablets and multi-dimensional tablets with simple preparation and low energy consumption is obtained.
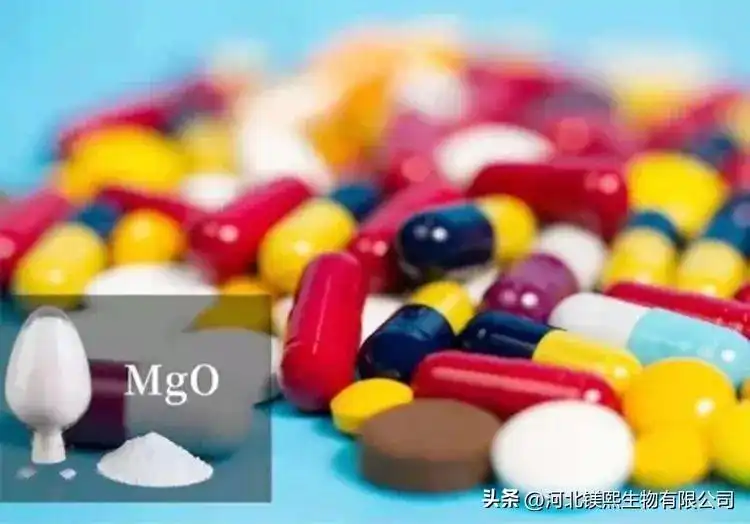
A preparation method of food-grade granular magnesium oxide for tableting, comprising the steps of:
(1) Send the magnesium hydroxide raw material into the swirl dynamic rotary kiln;
(2) Carry out indirect heating and calcining to it at a high temperature of 650-950 degrees, and the magnesium oxide generated is cooled by dehumidification;
(3) Enter impurity removal, particle size treatment, enter granulation, compression molding;
(4) Particle mixing.
It is characterized in that the mass fraction of magnesium hydroxide in the step (1) is 98%-99%, the particle size is D502-56 microns, D906-97 microns, and the bulk density is 1-0.2 g/ml. It is characterized in that, in the step (2), when heating and calcining, the preheating front section is controlled within 650°C, the heating time is controlled within 10 minutes, the calcining section is controlled at 850-950°C, and the time is controlled within 15 minutes; the cooling section is controlled within Below 550, the time is controlled at 20 minutes, the BET value is controlled at 30-60, and the crystal shape is approximately spherical. It is characterized in that, in the step (3), impurities are removed by jet classification, and the processed powder is firstly spherically granulated by a 0.3-0.5cm spherical groove roller machine, and then subjected to secondary compression by a linear roller Break up. It is characterized in that it is prepared by adopting any one of the above-mentioned claims 1-4.