Hebei Messi Biology Co., Ltd. stated that magnesium hydroxide is an important inorganic material and is widely used in daily life. Magnesium hydroxide can be used to neutralize acidic wastewater, adsorb heavy metals in water, act as a decolorizer for wastewater and absorb sulfur dioxide in flue gas. As a green inorganic flame retardant, magnesium hydroxide has received widespread attention at home and abroad. But to make the material achieve the ideal flame retardant effect, the addition of magnesium hydroxide is usually as high as 60%. When its compatibility with organic matter is poor, it will affect the mechanical properties and mechanical properties of the material. The sample has good dispersibility in dry state, which is the prerequisite for good dispersion in organic matter.
The effect of filling conventional magnesium hydroxide and hexagonal flaky magnesium hydroxide on the mechanical properties of ethylene-vinyl acetate copolymer (EVA) was studied, and it was found that the conventional magnesium hydroxide greatly reduced the elongation at break of the material while the hexagonal flaky Magnesium has less of an effect. Highly dispersed hexagonal flaky magnesium hydroxide was prepared by using magnesium chloride and ammonia combined with hydrothermal method, and it was found that the hexagonal flaky product had good compatibility with EVA. Therefore, the preparation of hexagonal flake products with good morphology and dispersion can increase the dispersion and compatibility of magnesium hydroxide in other composite materials, and can also reduce the impact on the mechanical properties and processing properties of materials.
The article studies the effect of the preparation method on the crystal morphology and crystal plane growth. Magnesium hydroxide was synthesized in a microchannel reactor, and the effect of precipitant on crystal morphology and crystal facet growth was explored. Then, coupled with the hydrothermal reaction, the effect of the hydrothermal reaction on the crystal morphology and crystal plane growth was studied, and the process route for preparing magnesium hydroxide for flame retardancy was explored.
1 Experimental materials and preparation methods
1.1 Materials
Sodium hydroxide, ethanol and triethylamine, ammonia, brine.
1.2 Reaction device and preparation method
The activated carbon is used to absorb the pretreated brine as the source of magnesium, and the device for preparing magnesium hydroxide using a reactor is shown in Figure 1. Its preparation process is as follows: (1) prepare three kinds of precipitants respectively, wherein the molar ratio of magnesium chloride and precipitant is 1:2; (2) pour the raw material products into the raw material storage tank respectively, and set the constant temperature circulating water bath to 25°C; open The power switch of No. 1 peristaltic pump and No. 2 peristaltic pump, set the same feed flow rate of 50mL/min; (3) Turn on the inlet and outlet switches of the reactor, and after turning on the peristaltic pump, mix the two reactants in the reactor and collect the product (4) After the reaction, the solid sample obtained by centrifuging the slurry was washed three times with deionized water and ethanol; (5) Collect the washed and dried samples for further characterization tests.
Direct hydrothermal preparation process: (1) The solid slurry after one-step reaction is injected into a 50mL hydrothermal reaction kettle with a filling capacity of 70%, and quickly placed in a blast drying oven at 180°C for 6 hours; (2) Rapidly cool to room temperature, centrifuge the solid product obtained by washing with deionized water and ethanol three times respectively, collect the washed and dried product for characterization test.
Indirect hydrothermal preparation process: (1) The solid slurry after the one-step reaction is centrifuged and washed 3 to 5 times with deionized water. The filling amount in the reactor is 70%, and the solid content in the mineralizer is 7%. Put it into a blast drying oven at 180°C for 6 hours; (2) quickly cool down to room temperature, and wash the solid product obtained by centrifugation with deionized water and ethanol three times respectively, and collect the washed and dried product for characterization test.
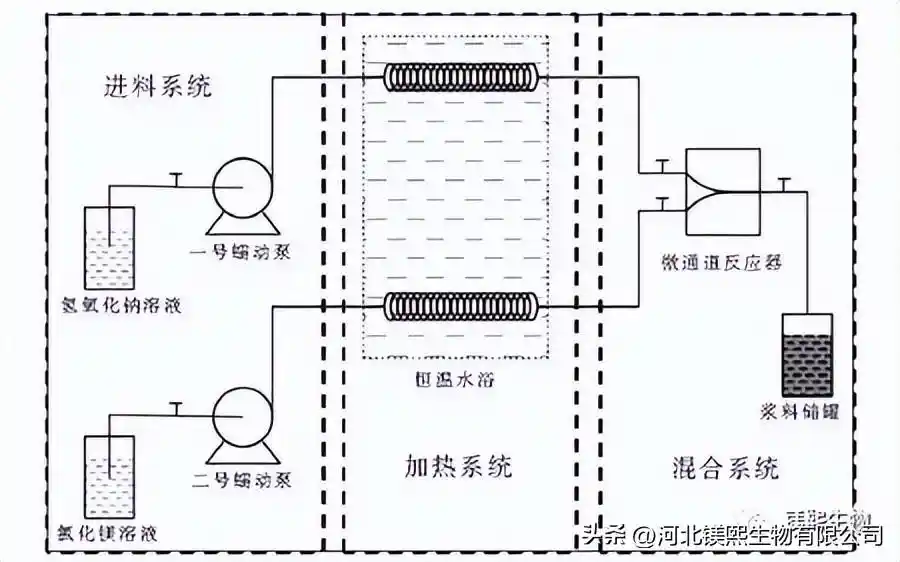
1.3 Experimental instruments and characterization equipment
Field emission high-resolution scanning electron microscope (FESEM), X-ray diffractometer, using a self-designed reactor.
2 Experimental results
2.1 Effect of precipitant on crystal morphology (Figure 2, Figure 3, Table 1)
Using the purified brine as raw material, the process route for preparing hexagonal flaky magnesium hydroxide was explored using a new reactor designed by ourselves. The effects of conventional precipitation, direct hydrothermal and changing hydrothermal bottom solution on crystal morphology were compared.
In Figure 2, sodium hydroxide, ammonia water and triethylamine were used as alkali source precipitants to explore the influence on the morphology of samples. However, studies have shown that the larger the ratio of I(001)/I(101) and I(001)/I(110) in the XRD test of the sample, the better the dispersion of the sample in the dry state, the less polarity of the crystal surface, and the combination of The better the material compatibility [10]. Among them, the samples prepared with sodium hydroxide as the precipitant had a nano-sheet structure and the samples were seriously agglomerated, while the samples prepared with ammonia water and triethylamine had an irregular sheet-like structure. From the XRD figure and Table 1, it can be seen that the strength ratios of sodium hydroxide, ammonia water and triethylamine (001) crystal plane and (101) crystal plane are 0.49, 0.53 and 0.52 respectively, indicating that ammonia water and triethylamine can promote Weakly polar (001) crystal plane grows, and the samples prepared by different precipitants have no XRD peaks, indicating that the prepared samples are of high purity. At room temperature, the agglomeration of samples prepared by strong alkali will seriously affect the application performance of the product. Ammonia and triethylamine can prepare flake products with relatively good dispersion.
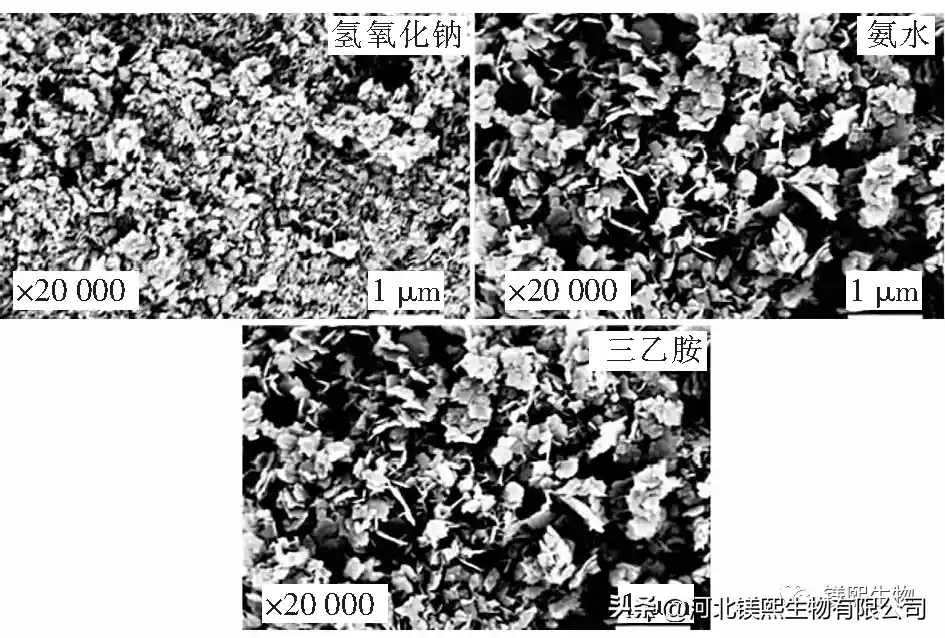
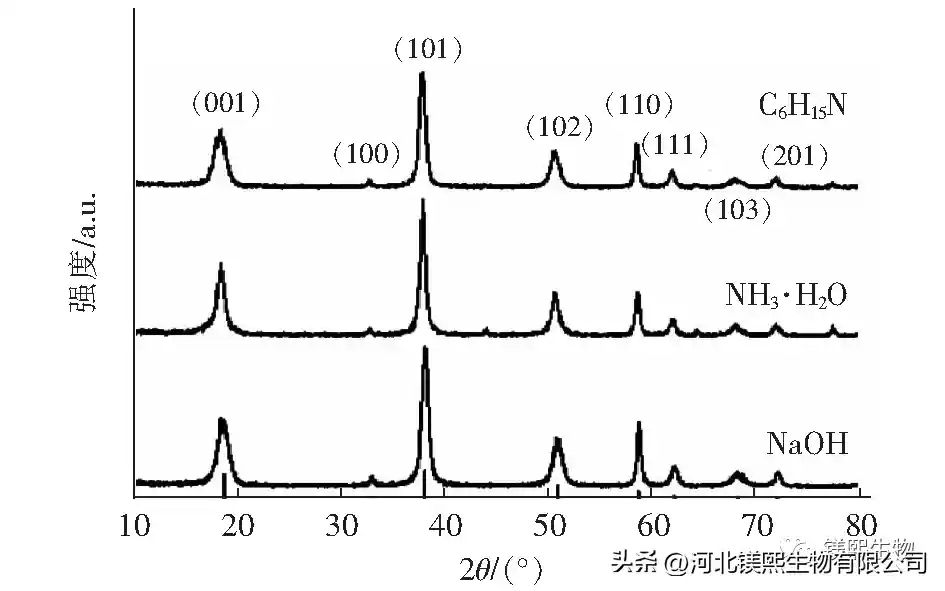
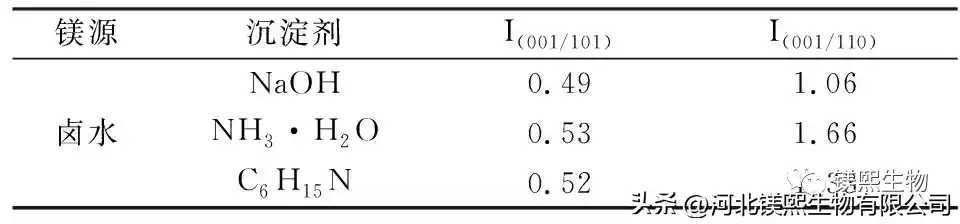
2.2 Effect of direct hydrothermal reaction on crystal morphology (Figure 4, Figure 5, Table 2)
Using sodium hydroxide, ammonia water and triethylamine as precipitants respectively, the reacted slurry was directly injected into a 50mL hydrothermal reaction kettle with a filling capacity of 70%, and reacted at 180°C for 6h to explore the effect of direct hydrothermal reaction on the sample shape. influence of appearance. It can be seen from Figure 4 that the samples prepared with sodium hydroxide as the precipitant are in the form of nanoparticles, while the samples prepared with ammonia water and triethylamine have a sharp-edged sheet structure and the sample dispersibility is greatly improved. In the XRD graph (Figure 5), the peak intensity of the samples prepared after hydrothermal treatment increased and the peak width narrowed, indicating that the hydrothermal reaction can effectively promote the growth of crystals and improve the crystallinity of samples. Compared with the conventional preparation method, the sample I(001)/I(101) increased after hydrothermal treatment. The edges and corners of the samples prepared by triethylamine became more distinct after hydrothermal reaction, and triethylamine was selected as the precipitating agent to explore the effect of changing the composition of the hydrothermal bottom solution on the morphology of magnesium hydroxide.
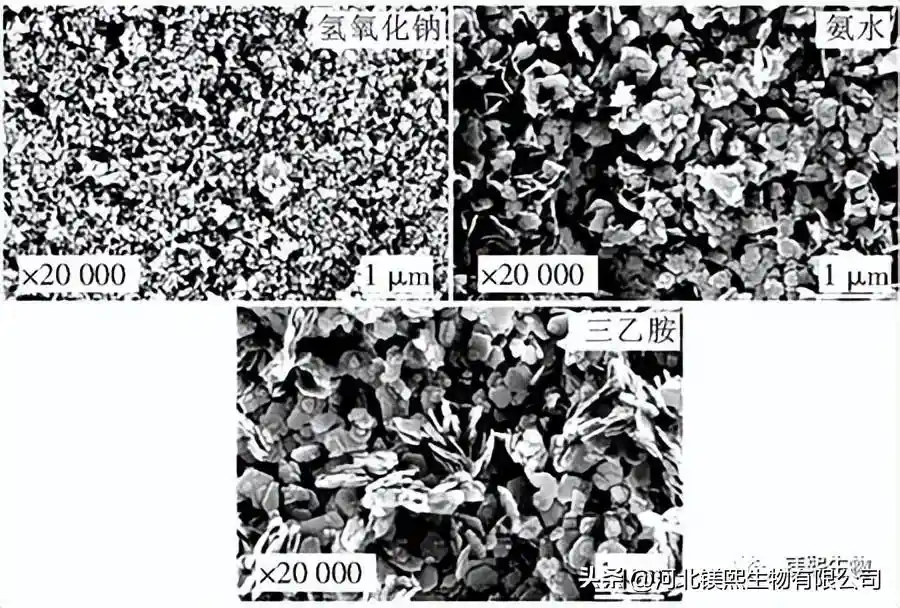
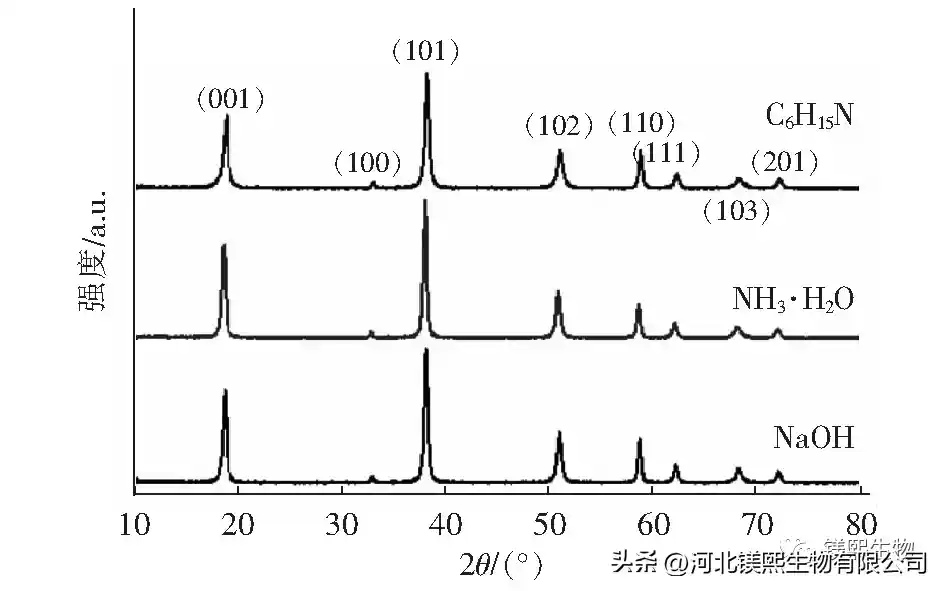
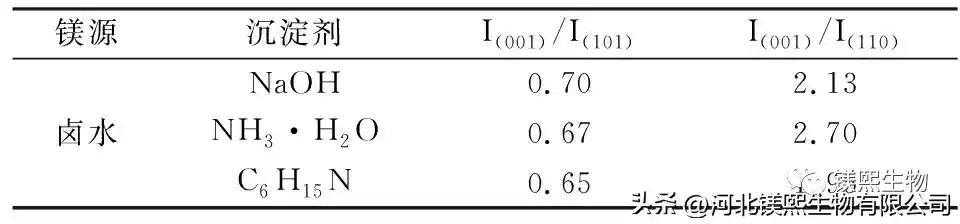
2.3 Effect of indirect hydrothermal reaction on crystal morphology (Figure 6, Figure 7, Table 3)
Figure 4 shows the sample prepared by the direct hydrothermal method, that is, the solid slurry after the reaction is directly injected into the hydrothermal reactor kettle. Due to the complex composition of the brine, in order to reduce the influence of other impurity ions in the brine on the sample morphology, the reacted solid slurry was centrifuged and washed 3 to 5 times with deionized water. The filling capacity of the reactor was 70%. The content is 7%, and the effect of the composition of the bottom solution on the sample morphology is further explored. The bottom solvents were 50% methanol, 50% ethanol, 50% isopropanol and the same amount of water, and heated at 180°C for 6 hours to explore the influence of the bottom organic solvent on the morphology of the samples. In Fig. 6, the adhesion between the samples prepared with methanol as the solvent is serious, the samples prepared with ethanol and isopropanol are irregular flake products, and the aqueous solution at the bottom of the kettle is a sharp-edged flake structure. It can be seen from Figure 7 and Table 3 that the use of organic solvents can inhibit the growth of (001) crystal planes.
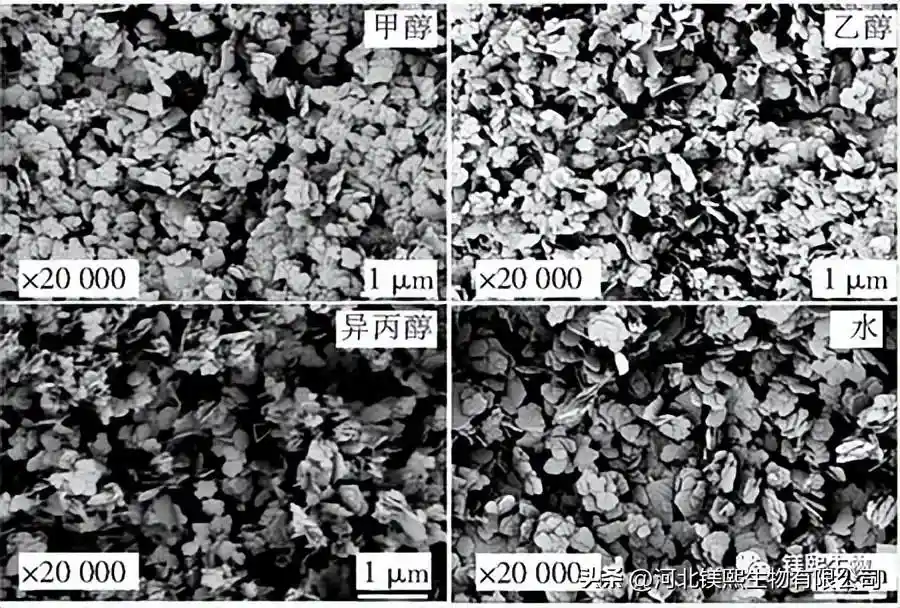
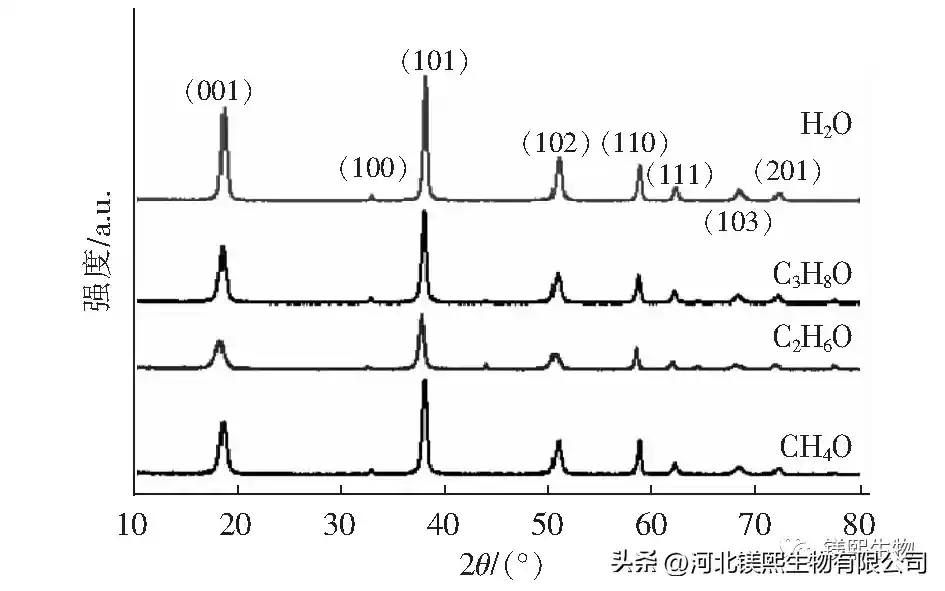
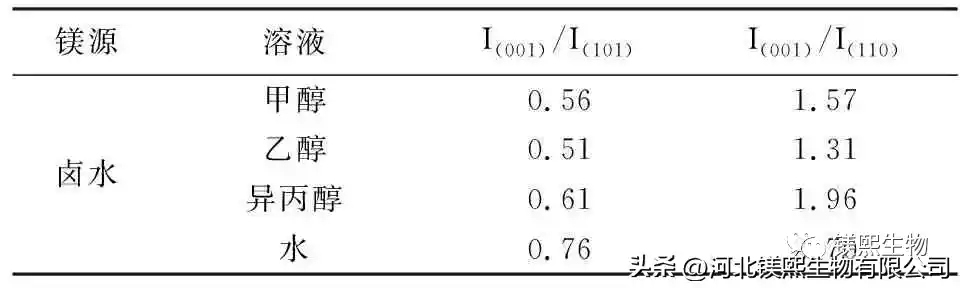
2.4 Effect of mineralizer on crystal morphology (Figure 8, Figure 9, Table 4)
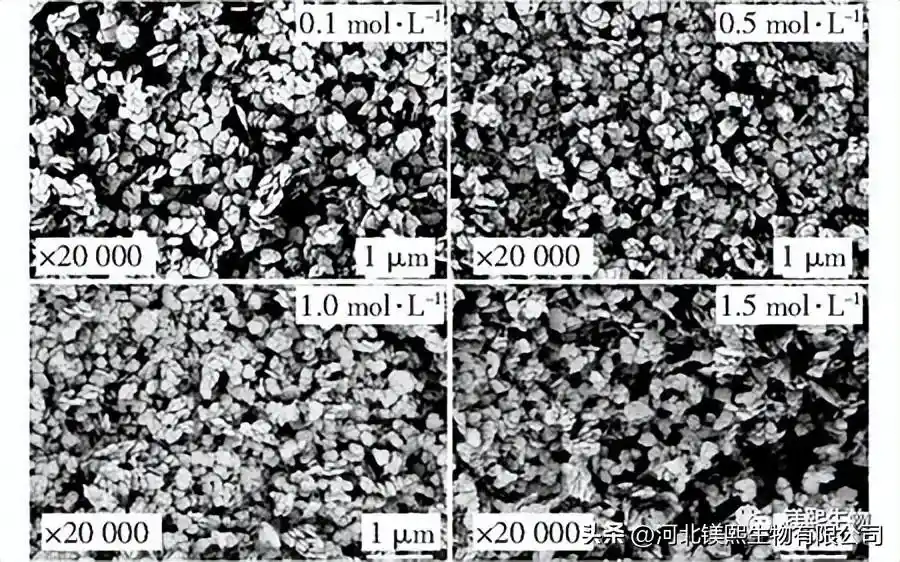
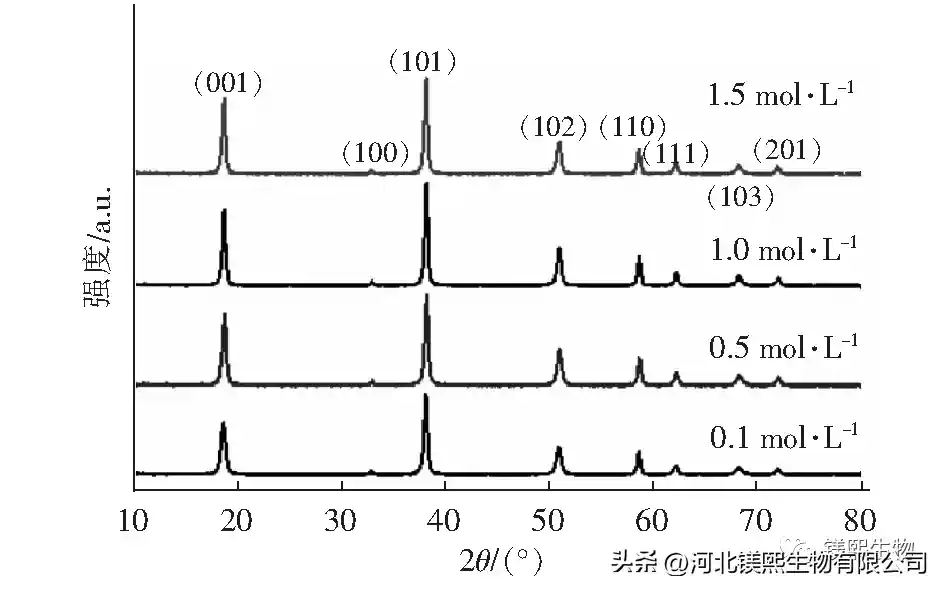
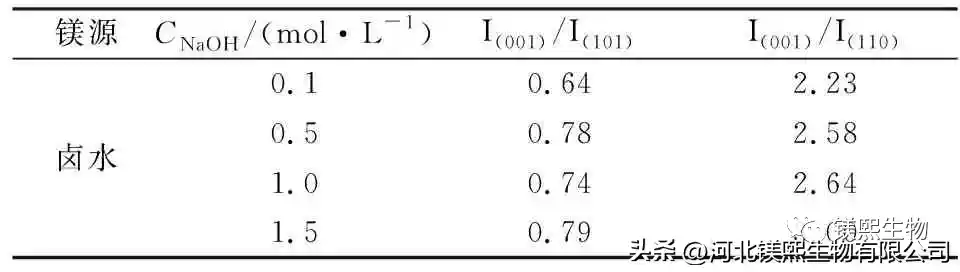
2.5 Formation mechanism of magnesium hydroxide (Figure 10)
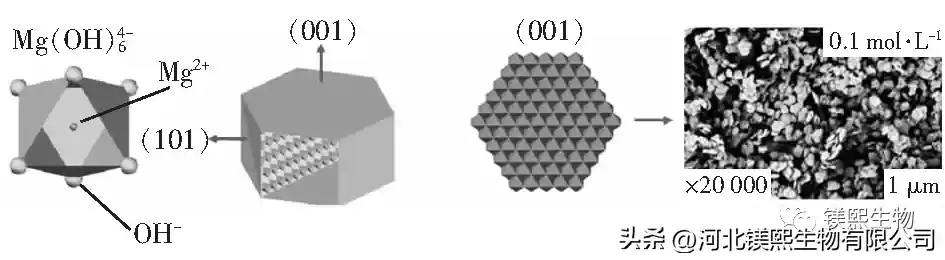
2.6 Comparison of Industrial Magnesium Hydroxide and Magnesium Hydroxide for Flame Retardant (Table 5)
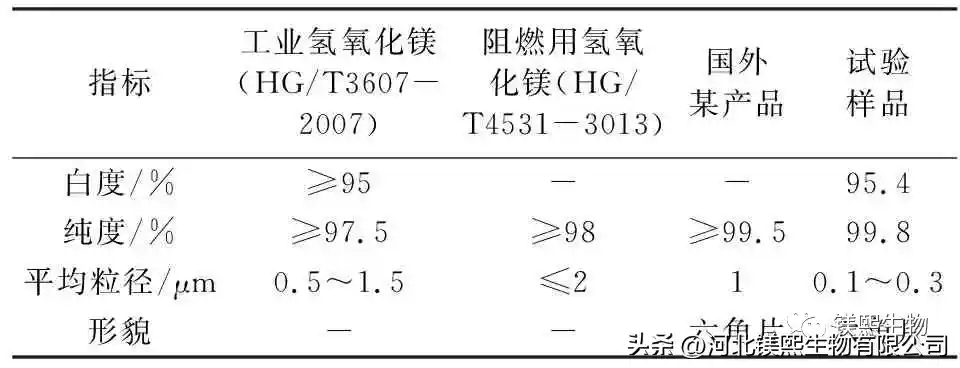
Comparing the whiteness, purity, and particle size indicators of industrial magnesium hydroxide and flame-retardant magnesium hydroxide, 0.1mol/L sodium hydroxide solution is used as the mineralizer at the bottom of the kettle, and the whiteness of the sample prepared by hydrothermal reaction at 180°C for 6 hours can reach 95.4%, the purity can reach 99.8%, and the particle size is 0.1μm~0.3μm. Comparing with imported hexagonal flaky magnesium hydroxide for flame retardant, after optimizing the process route, this scheme prepared nano-hexagonal flaky magnesium hydroxide. This study is of great significance for the comprehensive utilization of brine resources and the vigorous development of the magnesium hydroxide industry.
3 Conclusion
The article prepared magnesium hydroxide through a microchannel reactor, and the synthetic product was coupled with hydrothermal reaction to prepare flaky magnesium hydroxide with good dispersion. The following conclusions were drawn:
1) Using the reactor at room temperature, the magnesium hydroxide sample prepared with sodium hydroxide as the alkali source was seriously agglomerated, while the magnesium hydroxide prepared with ammonia water and triethylamine as the alkali source had relatively good dispersion and was irregular flakes. The XRD diffraction peaks of the sample coincided with those on the standard card, indicating that magnesium hydroxide with higher purity was prepared.
2) During the hydrothermal preparation process, the organic solvent at the bottom of the kettle will inhibit the growth of the (001) crystal plane. The choice of sodium hydroxide solution at the bottom of the kettle can promote the formation of growth bases, and can prepare nano-hexagonal flaky magnesium hydroxide. The whiteness, purity and particle size of the sample meet the flame-retardant magnesium hydroxide index.