Magnesium oxide for plate glass refers to magnesium oxide used in plate glass production. In the production process of plate glass, magnesium oxide is mainly used in the following aspects:
① As a flux, it lowers the melting point of glass, increases the fluidity of glass, and improves the processing performance of glass.
② As a crystal nucleating agent, it promotes the crystallization of glass and improves the strength and wear resistance of glass.
③ As a filler, it increases the density and hardness of glass and improves its optical properties.
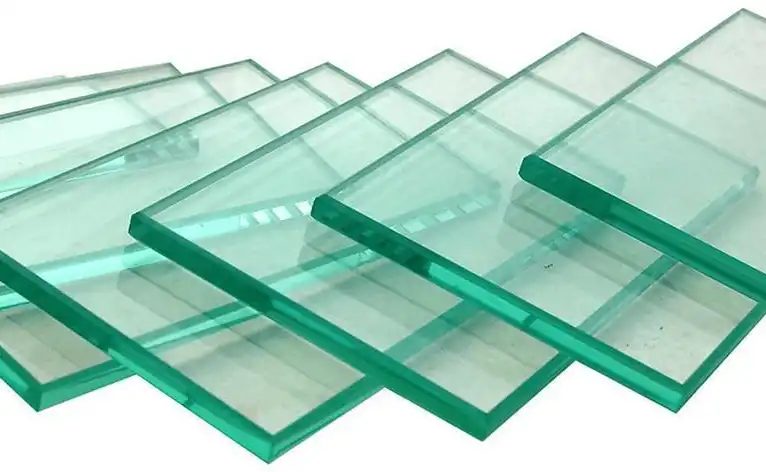
Magnesium oxide for plate glass generally has the following characteristics:
① High purity and low impurity content to avoid affecting the performance of the glass.
② The particle size is uniform, which is beneficial to the melting and crystallization of glass.
③ Low hygroscopicity so as not to affect the quality of the glass.
There are two main methods for producing magnesia for plate glass:
① Electric fusion method: Melt magnesite or dolomite in an electric arc furnace to generate magnesium oxide slag, and then cool and crush the slag to obtain magnesium oxide powder.
② Chemical method: React magnesite or dolomite with sodium hydroxide or sodium chloride to generate magnesium hydroxide or magnesium chloride, and then calcine magnesium hydroxide or magnesium chloride to generate magnesium oxide.
The dosage of magnesium oxide specially used for plate glass is generally 2%-3% of the weight of the glass. The specific dosage depends on the type and performance requirements of the glass.
Magnesium oxide for plate glass is an important raw material for plate glass production, and its quality directly affects the performance of the glass. Therefore, when choosing magnesium oxide for plate glass, you should choose products with qualified quality and stable performance.
The following are common indicators of magnesia for plate glass:
Purity: above 98%
Particle size: <10μm
Hygroscopicity: <0.1%
The price of magnesia for plate glass is generally RMB 2,000-3,000 per ton.