Hebei Messi Biology Co., Ltd. said that if it wants to occupy a place in the fiercely competitive international electric heating market, it must produce high value-added electric heating tubes, which requires the use of magnesium oxide as the main material.
1. The definition of electrical grade magnesium oxide:
Refers to the fused crystalline magnesium oxide block that has been crushed and mixed with different particle sizes or numbers in a certain proportion, and used directly or modified in tubular electric heating elements as an insulating medium for heat conduction at high temperatures. .
2. Classification of electrical grade magnesium oxide:
According to the production method and main uses, it can be divided into the following four categories:
ordinary type, low temperature moisture-proof type, medium temperature moisture-proof type, high temperature type
3. Performance requirements of magnesium oxide;
① When magnesium oxide is at working temperature, it must have high thermal conductivity so that it can quickly transfer heat to the surface of the tube and bring the temperature of the resistance wire closer to the tube wall;
② When the working temperature is within 1100°C, magnesium oxide should have good insulation properties;
③ Magnesium oxide must have a certain particle size, and the shape is generally round instead of the flakes currently produced in my country, because the round shape has a high filling density, good fluidity, and a certain percentage of particles, and is not easily damaged and heated over time. silk to ensure filling without difficulty;
④ Magnesium oxide should not corrode heating wire materials and pipes at normal or high temperatures.
⑤ The water absorption rate of magnesium oxide shall not be higher than the following regulations: ordinary type ≤ 1.5%, low temperature moisture-proof type ≤ 0.05%, medium temperature moisture-proof type ≤ 0.10%, high temperature type ≤ 0.10%
4. Particle size analysis of electrical grade magnesium oxide;
Since magnesium oxide ore has different particle sizes after being crushed, it has the following advantages if it is mixed according to a certain number.
1) It can increase the density and reduce the working temperature of the resistance wire, thereby increasing the life of the electric heating element;
2) It can overcome the “sieving” effect and improve the utilization rate of magnesium oxide;
5. Analysis of the state of magnesium oxide when heated;
The porosity of magnesium oxide compressed in a tubular electric heating element is 15% under normal circumstances, that is, the density of magnesium oxide at this time is: the true density of magnesium oxide minus the porosity, that is, 3.85*(1-15%)=3.05 g/cm3. If the operating temperature of the electric heating element is sufficiently high, the oxygen in the pores will interact with the resistance wire and pipe. Due to this reaction, the partial oxygen pressure will decrease. The final partial oxygen pressure determines the oxygen and the metal parts of the element. affinity between. According to data, some oxygen pressures may drop to 10-13~10-19ata. Under such low oxygen pressure, the properties of the fine particles of fused magnesium oxide change, that is, the common magnesium oxide turns black. Under oxidizing conditions, magnesium oxide mainly evaporates in molecular form at high temperatures without decomposing. Under reducing conditions, Magnesium oxide may be partially reduced.
It can be seen that when the pressure in the electric heating element drops by 10-19~10-13 ata at 800~1000℃, magnesium oxide has the conditions for reduction and decomposition. Only by adding a “reducing atmosphere”, the necessary conditions are met for the sufficient reduction and decomposition of magnesium oxide. In this way, magnesium oxide begins to turn black. If the cross-sectional area of the electric heating element is affected, it will cause the insulation of the heating element to decrease and deteriorate. , so the leakage current increases. Some data also believe that this reaction is reversible. If annealed in air at 900°C, the original properties will be restored.
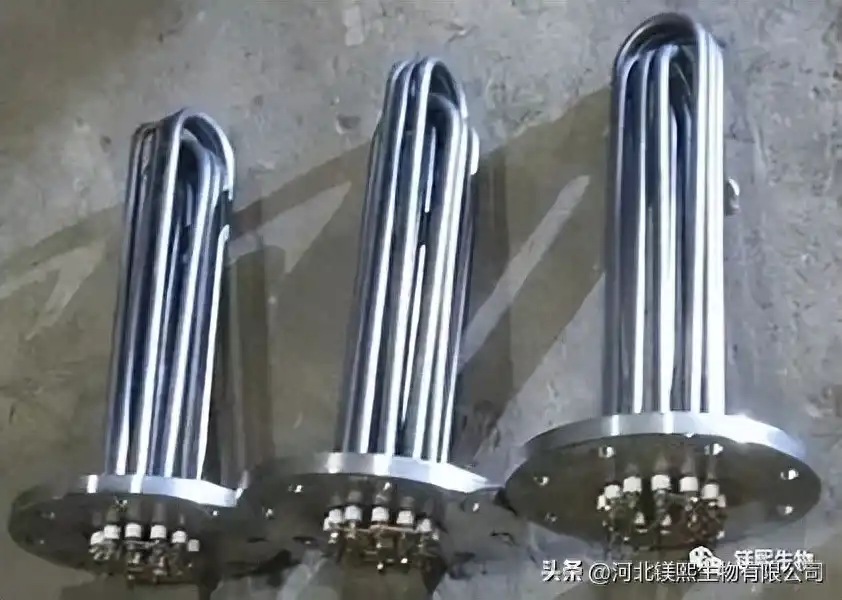
6. What issues should be paid attention to when using electrical grade magnesium oxide?
① For stainless steel components with relatively long tubes (such as 4 to 6 meters), they must be annealed at a high temperature of 900°C before bending. In this case, the resistance wire should use nickel-chromium wire instead of iron-chromium wire as much as possible. Because aluminum (Al) is particularly easy to snatch oxygen from magnesium oxide at 900°C (aluminum has a strong affinity with oxygen), resulting in partial reduction of magnesium oxide, that is, magnesium oxide turns into metal magnesium, which will make magnesium oxide black. Of course, using Nichrome wire is much better because chromium has a smaller affinity to oxygen and nickel has a smaller affinity to oxygen, so to reduce magnesium oxide, i.e. the reduction temperature is much higher.
② Increasing the compressed density of magnesium oxide can reduce the working temperature of the resistance wire, but this is meaningless for energized use and annealing (referring to stainless steel 900°C), because there is a temperature gradient in the former and the temperature of each point in the latter equal.
③ Reducing the thickness of the insulating layer of magnesium oxide can also reduce the working temperature of magnesium oxide and increase the life of the heating tube.
④ Prevent the generation of organic matter and rust spots on the inner wall of the pipe. Therefore, the pipes, especially the iron pipes, must be pickled, dried and rusted. After this process is completed, the pipes can be filled in quickly and must not be left for too long, especially This is done in seasons with higher temperatures to avoid rust.
⑤ Since magnesium oxide itself contains organic matter that will cause the magnesium to turn black, it is recommended that the magnesium oxide used be roasted before filling.
⑥ Magnesium oxide should not be exposed to the sun or night dew, nor should it be exposed to rain in the open air to avoid the infiltration of acid rain and harmful gases.