Hebei Messi Biology Co., Ltd. stated that the method of using magnesite to smelt light magnesium oxide includes: calcining magnesite into magnesium oxide; placing magnesium oxide on a mill, adding water to finely grind it; passing the slurry through a mesh screen Continue to stir, add a separating agent to stir and separate calcium and magnesium. The slurry is filtered to obtain the filtrate and precipitate. The filtrate is heated and evaporated and then ground to obtain calcium chloride; add water to the precipitate to make the slurry; put the above slurry into the carbonization tower for use During calcination, the carbon dioxide gas in the kiln enters the carbonization tower through the air compressor and pipeline, carbonizing the slurry and reducing it to magnesium carbonate; the above magnesium carbonate is precipitated and filtered and then put into the acid solution; after filtering to remove impurities such as iron hydroxide Add soluble magnesium hydroxide to the above solution, and add ammonia salt water at the same time, and precipitate the magnesium hydroxide generated in the solution; filter the precipitated magnesium hydroxide, and then burn or dry it to make a light oxide. magnesium.
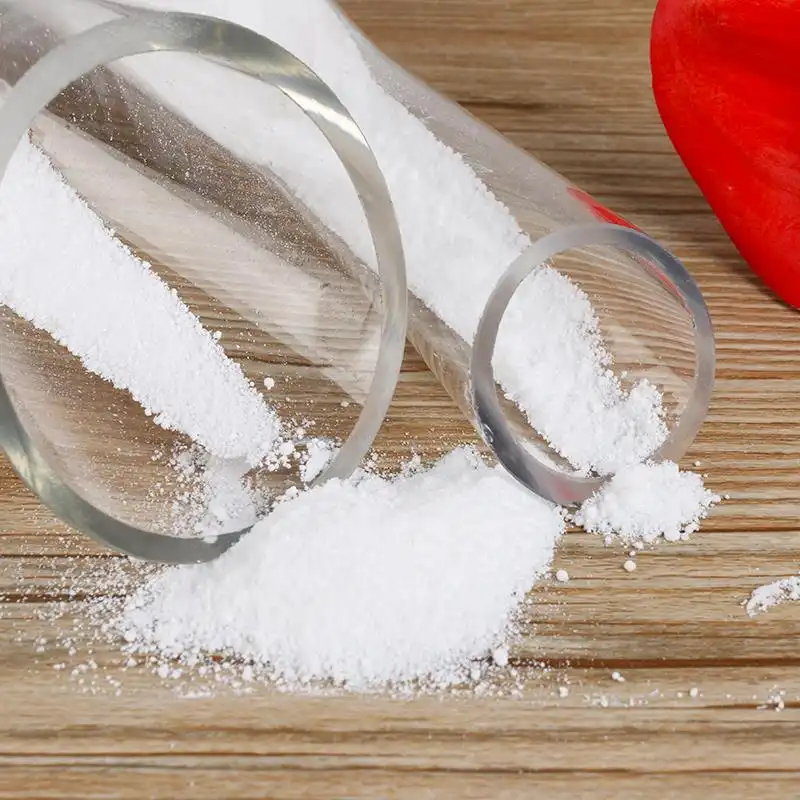
The method of the invention can obtain high-quality light magnesium oxide and has a simple process. It is characterized by including the following steps:
- Put magnesite as raw material in a carbonization kiln and calcine it into magnesium oxide;
- Place the magnesium oxide on the mill, add water and grind it until it passes through a 200-mesh sieve. At this time, the temperature of the magnesium oxide is between 100 and 150°C;
- Control the temperature of the slurry after passing through the mesh screen at 80~90°C and continue stirring and digesting it for 1.5#3h. Add a separating agent and stir to separate calcium and magnesium. The slurry is filtered to obtain the filtrate and precipitate. The filtrate is heated and evaporated and then powdered. Grind to obtain calcium chloride; add water to the precipitate to make slurry, and control the temperature at 20°C;
- When the above slurry is put into the carbonization tower for calcination, the carbon dioxide gas in the kiln enters the carbonization tower through the air compressor and pipeline, so that the slurry is carbonized and reduced to magnesium carbonate;
- After precipitation and filtration, the above magnesium carbonate is put into an acid solution with a concentration of 80°95°. After acid hydrolysis into soluble magnesium hydroxide, an oxidant is added to the mixed acid solution to react. After the reaction, the above solution The ferrous iron is oxidized to ferric hydroxide;
- After filtering to remove impurities such as iron hydroxide, add soluble magnesium hydroxide to the above solution, and at the same time add ammonia salt water with a concentration of 25#28% to allow dilution and pyrolysis for 1#3 hours.