- Salt Lake Brine Method
Qarhan Salt Lake is the largest symbiotic salt lake of potassium and magnesium salts in the world. In the process of extracting potassium chloride, the by-product magnesium chloride is 10 times that of potassium fertilizer. The preparation of magnesium oxide can utilize the by-product magnesium chloride in large quantities and at the same time alleviate the domestic demand for magnesia. The rational development and comprehensive utilization of Qinghai salt lake resources are of far-reaching significance. The main methods for preparing magnesium oxide from brine or chlorite include lime method, ammonium bicarbonate method, soda ash method, and chlorite direct pyrolysis method.
Lime method
The magnesium chloride solution reacts with calcined limestone (or dolomite) gray milk to form magnesium hydroxide precipitate, calcined magnesium oxide. The process of producing magnesium oxide from hydrocite limestone produces 1 ton of magnesia as a by-product of 2.76t CaCl2. If it cannot be effectively utilized, new waste piles will be generated, resulting in the inability to expand the production scale.
ammonium bicarbonate method
Ammonium bicarbonate (or carbon dioxide and ammonia) reacts with magnesium chloride solution to form basic magnesium carbonate, which is decomposed into magnesium oxide after calcination. This method uses ammonium carbonate as an auxiliary raw material, which requires a large amount of evaporated water and increases heat energy consumption, which will increase production costs. For example, using carbon dioxide waste gas emitted from ammonia synthesis plants and intermediate product ammonia as auxiliary raw materials, the production cost is low.
ammonia method
Precipitate magnesium by seeding hydrochlorite (or old brine) and liquid ammonia (or ammonia water), and the precipitate is washed, dried, and calcined to obtain a magnesium oxide product. The magnesium precipitation efficiency of the ammonia method for preparing magnesium oxide can reach 80%-85%, the ammonia conversion rate can reach 80%, the mass fraction of magnesium oxide in the product is above 90%, and the by-product NH4Cl can be used as a raw material for fertilizer and chemical industry, and there is no three industrial wastes. , basically no environmental pollution. If a special seed crystal core is added during the magnesium precipitation process, ultrafine magnesium oxide, magnetic magnesium oxide and air magnesium oxide can be produced.
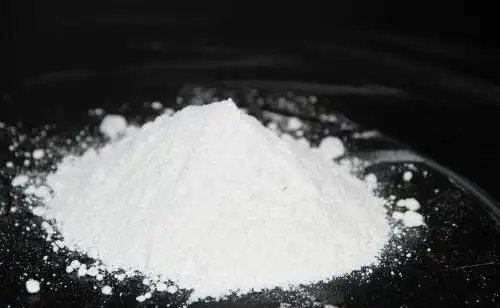
Soda ash method
React brine with soda ash to form basic magnesium carbonate precipitate, which is washed, dehydrated and calcined to produce magnesium oxide. The magnesium oxide product produced by this method has high purity, simple process and low energy consumption, but the use of soda ash will make the cost too high.
The above four methods all react in the liquid phase. Impurity ions are removed by adding precipitants, detergents and chemical refining methods to maintain the purity of basic magnesium carbonate or magnesium hydroxide. The final purity of high-purity magnesia can reach more than 99.9%. However, the cost of producing high-purity magnesia from brine is too high, the energy consumption is large, the process is complex, and there are many difficulties.
Hydrocite direct pyrolysis method
Hydrous magnesium chloride is heated in air (or hot air flow) and gradually loses crystal water as the temperature increases. The process of this method is relatively simple, does not require the consumption of any auxiliary raw materials, reduces production costs, and makes it easier to achieve high value and industrialization of magnesium. The current methods mainly include spray method and boiling furnace method. (1) Spray pyrolysis method sprays brine directly into the thermal decomposition reactor for thermal decomposition. After calcination, coarse magnesium oxide is obtained. It is washed with water multiple times to remove completely decomposed soluble chloride. The crude magnesium oxide is completely hydrated to form Mg( OH)2, calcined to light magnesium oxide, and then calcined to obtain high-purity magnesia, with a purity of more than 99%.
Process for preparing magnesium oxide by spray method
The manufacturer that uses this method to produce magnesium oxide on an industrial scale is an Israeli company. This process has a short pyrolysis time and low production cost. The hydrogen chloride tail gas is highly corrosive and requires high equipment. It is also very difficult to absorb and concentrate the hydrogen chloride tail gas.
boiling furnace pyrolysis
The raw materials are dehydrated, pyrolyzed and roasted in the boiling furnace, and the products are automatically overflowed from the discharge pipe into the collecting container for storage. The boiling furnace body dissipates large amounts of heat, and appropriate thermal insulation measures should be adopted to reduce heat dissipation and improve the effective heat utilization of the furnace.
- Preparation of magnesium oxide by ore method
Calcined magnesite method
Magnesite contains more than 90% magnesium carbonate, as well as a small amount of calcium carbonate and other trace impurities. Magnesium oxide with higher purity can be obtained by direct calcination. This method has simple process, low production cost and high product activity. However, the product contains impurities such as CaO, SiO2, Fe and B, which are difficult to separate. The content of magnesium oxide in the product can only be about 98%. There are many technical problems in further improving the purity. Solving these problems will greatly increase the production cost.
Carbonization method
Solid minerals such as magnesite are calcined into powder, digested, CO2 is introduced, carbonized, heated and hydrolyzed to produce basic magnesium carbonate, and then dried and burned to obtain light magnesium oxide. This method has low production cost, but the product purity is low, the production process is long, and the equipment investment is large. A series of efficient magnesium oxide production processes have been further optimized by the carbonization method, such as secondary carbonization method, pressure carbonization method, carbon ammonia double cycle method, etc.
Secondary carbonization method
The principle is the same as the carbonization method, except that the second carbonization is carried out to remove impurities, which relatively improves the purity of the product. In the process of preparing high-purity magnesium oxide by the secondary carbonization method, due to the secondary impurity removal, the mass fraction of magnesium oxide in the product can exceed the high purity requirement of 99.2%. In the pressure carbonization method, a more thorough pressure carbonization is performed after normal pressure carbonization, which greatly improves the efficiency of carbonization impurity removal and the purity of the magnesium oxide product.
Carbon ammonia double cycle method
Compared with the traditional carbonization method, this method has a short production cycle, low energy consumption, low production cost and stable product quality. The mother liquor, ammonia, carbon dioxide, etc. are all recycled to maintain minimal environmental pollution. The extraction rate of dolomite using this method can reach 60%-64%, and the purity of the product magnesium oxide is high.
Acid hydrolysis
It is mainly divided into six steps: acidolysis, calcination, calcium decomposition, acid dissolution, magnesium precipitation, and burning. The acid hydrolysis method to produce magnesium oxide has simple raw materials, low equipment investment, low energy consumption, and no industrial waste pollution. However, more impurity ions enter. Without multi-step post-processing, the purity of the product will be affected. Since this method consumes a lot of acid, if there is no suitable and cheap acid source, the production cost will be greatly increased.
ammonium sulfate method
Magnesite is crushed and reacted with ammonium sulfate. The generated magnesium sulfate absorbs ammonia and precipitates, and is calcined to obtain the product magnesium oxide. In the reaction with ammonium sulfate, impurities such as CaO, Fe2O3, Al2O3 and SiO2 are insoluble and are removed by filtration, resulting in a higher purity product.
Ammonium sulfate double salt method
The ammonium salt and magnesium salt are reacted in an aqueous solution to form ammonium magnesium carbonate tetrahydrate double salt with a fixed crystal lattice composition, which is thermally decomposed at 200-250°C to obtain magnesium carbonate, and then thermally decomposed at 500-600°C to obtain magnesium oxide product. In the process of generating this double salt with a specific composition, impurity ions such as K+, Na+, Ca2+, Cl-, NO3-, SO42- and [B(OH)4]- are excluded from the crystal and remain in the solution. The mass fraction of each substance in the product is (MgO) ≥ 98%, (CaO) ≥ 0.3%, (B2O3) ≤ 0.008%. This process is relatively simple, has low equipment investment, low heat consumption, and the resulting product has high purity. However, the process conditions for industrial production are not mature and have not been used in industrial production. Art overview