Hebei Messi Biology Co., Ltd. stated that the particle size of magnesium oxide has a significant effect on the suspension and coating properties of magnesium oxide. Silicon steel grade magnesium oxide is generally made into spherical particles, which are easy to roll, have low resistance to movement between particles, and have good fluidity. The coating is characterized by good filling between particles and dense and uniform coating. In addition, magnesium oxide must have a certain particle size distribution to ensure the circulation of moisture and annealing environment gas during high-temperature annealing of silicon steel grade steel coils. Generally, the particle size below 5μm is required to reach 70%.
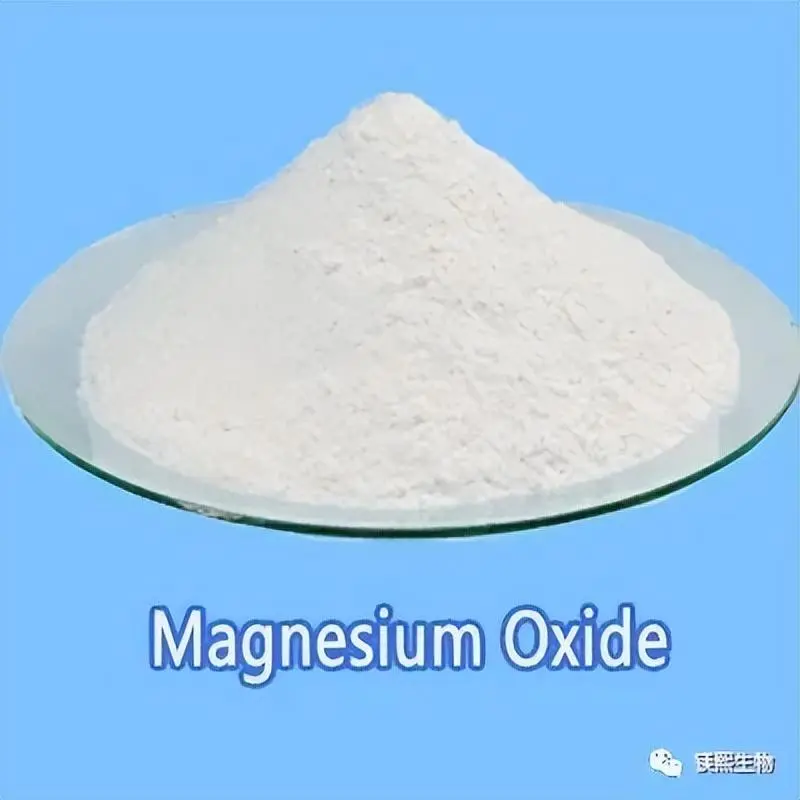
In the preparation process of silicon steel grade magnesium oxide, particle size control has always been a difficult problem. Since magnesium oxide is prepared by calcining intermediates, it is first necessary to control the particle size morphology of magnesium hydroxide or basic magnesium carbonate intermediates. Studies on crystal morphology have shown that when the temperature is too low, the crystal formation is incomplete and it is easy to agglomerate into larger grains. When the temperature is too high, the rate of nucleation formation decreases, the rate of crystal growth increases, and large grains are easily formed. In addition, the thermal motion of particles at high temperatures intensifies, and it is also easy to collide to form larger particles.
In the preparation of basic magnesium carbonate intermediates, the reaction temperature is generally controlled at 70~80℃ to obtain a more suitable particle size of basic magnesium carbonate. If the thermal decomposition temperature is higher than 85℃, the product particles will increase significantly, and the average particle size of magnesium oxide will be >5μm; if the thermal decomposition temperature is lower than 55℃, the decomposition in the decomposer will be incomplete, resulting in a lower yield. The particle size of magnesium oxide is not only determined by the particle size of the intermediate, but also has a great influence on it during the calcination process. At high temperatures, magnesium oxide may agglomerate, resulting in excessively large particle sizes. Studies have found that when roasting the basic magnesium carbonate intermediate, gradually increasing the temperature from low temperature can effectively avoid product sintering and ensure that the particle size of magnesium oxide is small.