Hebei Messi Biology Co., Ltd. stated that magnesium oxide films can be prepared by chemical vapor deposition, electron beam evaporation, laser pulse deposition, spray pyrolysis, sol-gel method, etc. In recent years, spray pyrolysis and sol-gel methods have been There are many studies on the sol-gel method.
Using magnesium acetate as raw material, a (100) oriented magnesium oxide film has been successfully prepared on a Si (100) substrate using a compressed air spray thermal decomposition method. In order to prepare a magnesium oxide film with (100) orientation, substrate temperature and spray rate are key factors. By controlling appropriate experimental conditions, a magnesium oxide film with (100) preferential orientation can be obtained at 600°C. The advantages of the spray pyrolysis method are simple equipment, no need for a vacuum system, high deposition rate and easy control of the composition of the film. The previous problems that atomization was limited by frequency, power, solvent, etc., as well as the problem of easy heat generation during atomization, have been improved or solved.
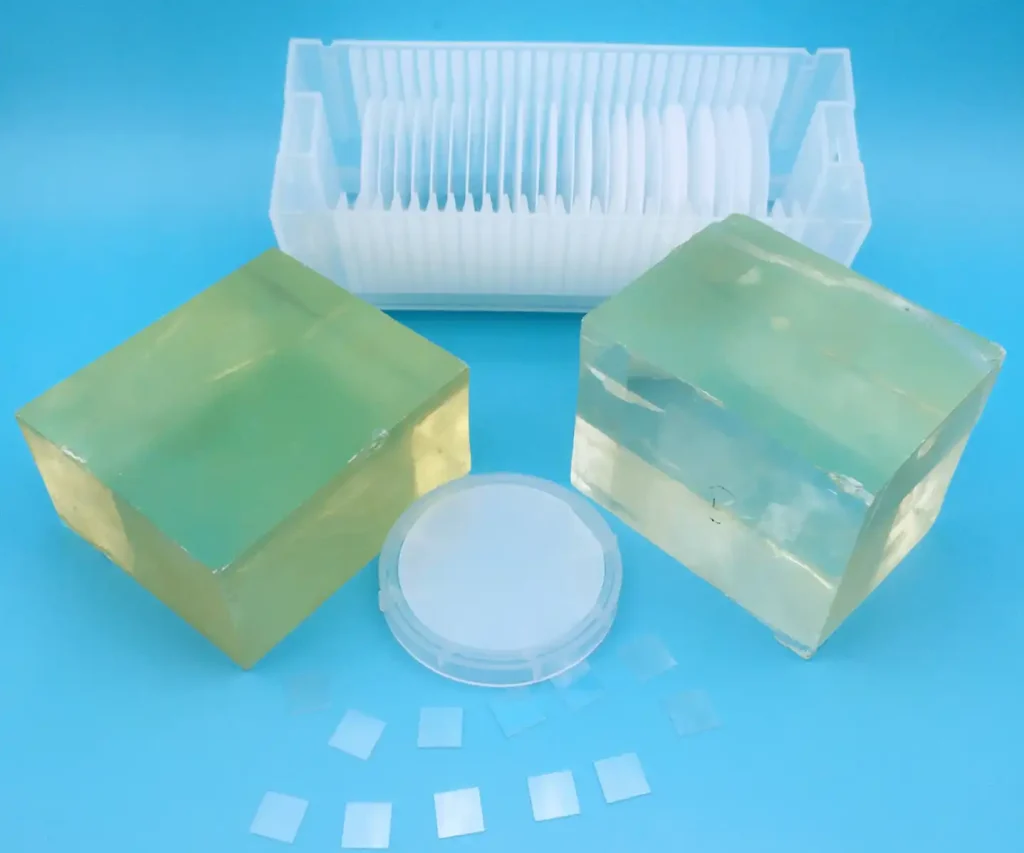
Using magnesium nitrate hexahydrate as the starting material and collodion liquid as the additive, magnesium oxide films can also be successfully prepared on Si (100) substrates through the sol-gel method. Dissolve magnesium nitrate hexahydrate in absolute ethanol, add an appropriate amount of collodion solution and stir to prepare a sol. Use Si (100) as the substrate and use the glue spinning method to form a film. The average glue speed is 3200r/min, and then at 480°C. Rapid heat treatment for 5 minutes, this process is repeated several times, and finally, the film is heat treated in the air at 600°C~900°C for 1 hour. Collodion liquid is the key component to form the sol. Under appropriate preparation conditions, the resulting film is dense and uniform in thickness. The boundary between the film and the substrate is clear, and there is basically no interdiffusion reaction.
Using magnesium nitrate hexahydrate as the starting material, using surfactant as the additive, and using the sol-gel dipping and pulling method, magnesium oxide films were also prepared on hydrophilic treated glass, mica, and single crystal silicon substrates. The magnesium oxide particle size in the film obtained by a single coating is about 12 nm, and the magnesium oxide particles in the film obtained by multiple coatings only have (200) and (220) crystallization orientations. The sol-gel method has a simple process and low preparation cost, but the films prepared by this method often have certain defects in uniformity and quality.
Magnesium Oxide Thin Films for Dielectric and Sacrificial Layer Materials
Hebei Messi Biology Co., Ltd. stated that magnesium oxide is an insulating solid inorganic material with a sodium chloride crystal structure, showing good chemical inertness, electrical insulation, optical transparency, high temperature stability, high thermal conductivity and secondary electron emission properties. . Making magnesium oxide into a thin film material can greatly increase its dielectric constant.
In the process of preparing high-performance integrated devices, there are great differences in physical and chemical properties between ferroelectric or superconducting materials and semiconductor substrate materials. If ferroelectric or superconducting films are directly deposited on the semiconductor substrate, some problems will arise. , such as diffusion reaction and lattice mismatch, resulting in dislocations at the interface and inside the ferroelectric or superconductor, affecting the electrical properties of the ferroelectric or superconductor. The difference in thermal expansion coefficient will generate stress, which will affect the ferroelectric or superconducting properties of the material. get worse.
Well-crystallized magnesium oxide films have good chemical stability, thermal conductivity and insulation. Magnesium oxide belongs to the cubic crystal system, Fm3m point group, lattice constant a0=0.4213nm, which is close to the lattice constants of commonly used semiconductor substrate materials Si, electrode materials Pt, and ferroelectric and superconducting materials. It is an excellent substrate. Materials that can be used to prepare stable barrier layers for high-temperature superconductors and ferroelectric films. Introducing a magnesium oxide film as a barrier layer can alleviate the differences in lattice constants and thermal expansion coefficients between the semiconductor substrate and ferroelectric or superconducting materials, while blocking the reaction between the two. At present, high-temperature superconducting films YBa2Cu3O7 and PbTiO3 ferroelectric films with excellent properties have been grown on magnesium oxide films with (100) or (111) orientation.
Magnesium oxide films can also be used as sacrificial layer materials. Sacrificial layer technology is a micro-machining technology used to prepare suspended structures and multi-layer structures. When selecting sacrificial layer materials, you must consider the subsequent processing technology, the impact of sacrificial layer removal on the material structure and performance, etc. Magnesium oxide, silicon oxide, photoresist , polyimide, etc. have been used as sacrificial layer materials. Considering comprehensive factors, magnesium oxide is a more suitable sacrificial layer material.
There are two types of sacrificial layer material removal: dry etching and wet etching. Dry etching uses gaseous atoms and molecules to react with the film to form volatile substances, or directly bombards the film surface to cause it to be corroded and removed. Dry etching uses Method etching can achieve anisotropic etching; wet etching uses the reaction solution to react with the sacrificial layer material to remove it. Wet etching equipment is simple and low-cost, and it is isotropic etching. Since magnesium oxide is difficult to react with other gaseous atoms and molecules, wet methods are used to remove the magnesium oxide sacrificial layer material. The research results of various acid solutions on magnesium oxide corrosion experiments show that the corrosion rate of phosphoric acid solution on magnesium oxide is moderate. The corrosion rate is related to the concentration and temperature of the phosphoric acid solution, so it is easy to control.