Hebei Messi Biology Co., Ltd. stated that there are two main technical routes for preparing spherical magnesium oxide: (1) using magnesium salt as raw material to first obtain the precursor for preparing spherical magnesium oxide, and heat treating the precursor to obtain spherical magnesium oxide; (2) After mixing the magnesium oxide powder with a solvent and a binder (the binder may not be used in some cases), the spherical magnesium oxide is obtained through mechanical molding, and the spherical magnesium oxide product is obtained through heat treatment.
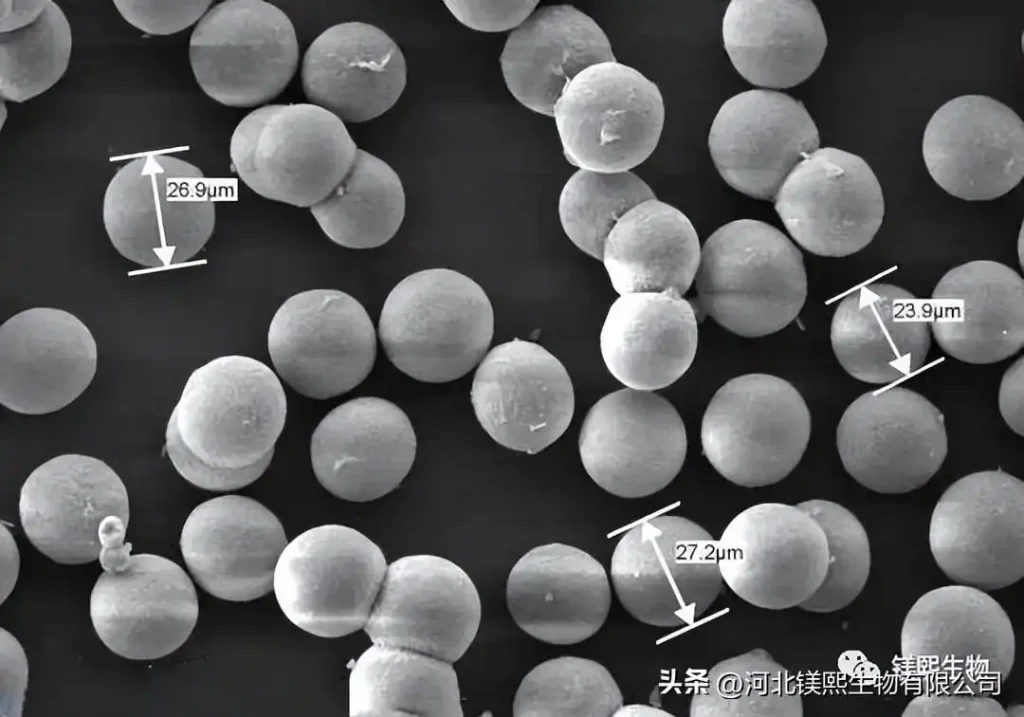
Using magnesium nitrate hexahydrate and potassium carbonate as raw materials, and a small amount of Mg5(CO3)4(OH)₂・4H₂O as crystallization inducer, the precursor for preparing spherical magnesium oxide was obtained through induced precipitation method, in the range of 573K~823K Calcination can produce spherical magnesium oxide with an average diameter of 9.5 μm, a specific surface area of 211.7 m2/g, an average pore diameter of 14.3 nm, and a pore volume of 0.76 mL/g. Using industrial magnesium sulfate and ammonium oxalate as raw materials and polyethylene glycol as an additive, basic magnesium oxalate is first prepared and calcined at 550°C to obtain ellipsoidal magnesium oxide with a particle size between 25nm and 32nm.
Hebei Messi Biology Co., Ltd. stated that magnesium oxide powder and water are mixed on a rotating disk and reacted at the same time to obtain magnesium hydroxide spheres. The magnesium hydroxide spheres are dried at 135℃~315℃, and then dried at 425 Heat treatment is performed at ℃~590℃ to obtain the final product. In order for the product to have good mechanical strength, at least 1% magnesium hydroxide should be retained in the final product.
High performance liquid chromatography (HPLC) is an effective separation technology, and its separation effect is greatly affected by the column packing. The currently used fillers are mainly silica-based fillers. When silica-based fillers are used for separation under alkaline conditions, they have problems such as secondary reactions, long retention times, severe tailing, low efficiency, and poor reproducibility.
Due to the above shortcomings of silica-based fillers, some research has been conducted on new fillers used under alkaline conditions. These fillers include organic polymers, carbon, alumina, titanium oxide, zirconia, etc. Among these fillers, alumina, Titanium oxide and zirconia have better chemical stability, thermal stability and selectivity, so they have attracted more attention. However, they have problems such as uneven pore size and small specific surface area.
In order to further improve the performance of chromatographic fillers that can be used under alkaline conditions, spherical magnesium oxide was studied as a chromatographic separation filler used under alkaline conditions. The average diameter of the spherical magnesia used was 9.5 μm and the specific surface area was 211.7 m2/ g, with a pore volume of 0.76mL/g and an average pore diameter of 14.3nm, which meets the packing requirements of HPLC columns in terms of physical properties. Compared with silica, due to the presence of oxygen vacancies and single electrons on the surface of magnesium oxide, magnesium oxide has better selectivity for the separation of basic compounds such as aniline derivatives, quinoline derivatives, and pyrimidine derivatives. The surface of magnesium oxide The interaction between the oxygen vacancies and the lone electrons or π electrons of these electron-rich compounds is an important mechanism for adsorption.