At present, the methods for preparing magnesium oxide using dolomite as raw material mainly include carbonization method, ammonium leaching method, acid hydrolysis method, brine method, etc. The ammonium leaching method has disadvantages such as environmental pollution, the acid hydrolysis method has high cost and complex process, and the carbonization method has high requirements for equipment. The brine-dolomite method uses dolomite ash as a precipitant for brine, and obtains the precursor magnesium hydroxide after reaction, which is then calcined to obtain magnesium oxide. This method not only precipitates magnesium in brine, but also realizes the separation of calcium and magnesium in dolomite itself, and obtains magnesium in two resources; from the perspective of comprehensive utilization, it is economical and environmentally friendly, the operation method is simple, and the application prospect is large.
Hebei Messi Biology Co., Ltd. has conducted preliminary research on the new process of preparing nano-magnesium oxide by brine-dolomite method.
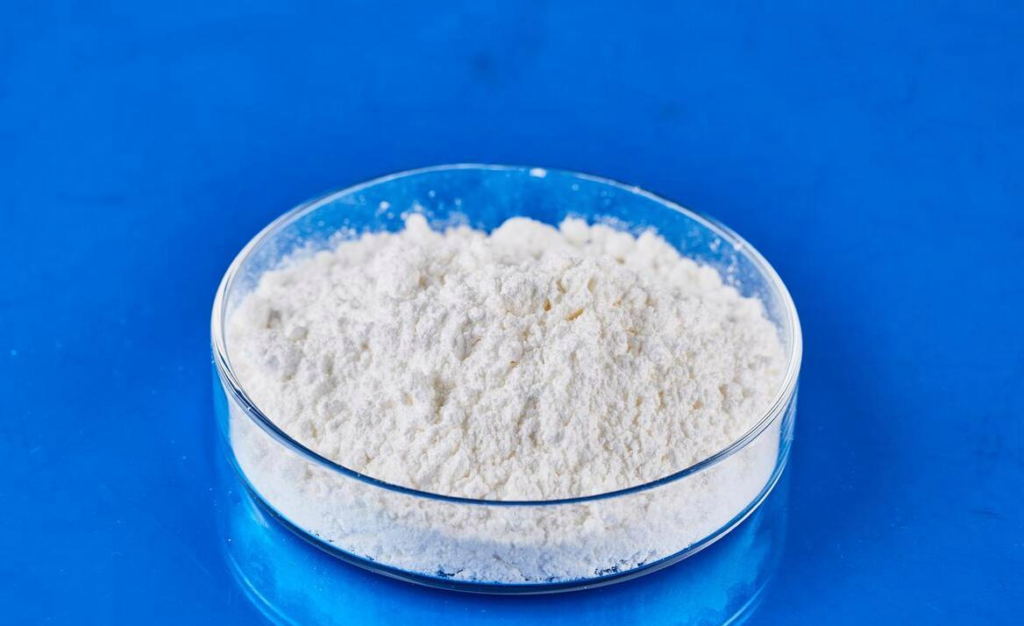
1 Experimental part
1.1 Experimental principle
Dolomite is calcined at high temperature to obtain dolomite lime, that is, magnesium oxide and calcium oxide. Dolomite lime is digested and the temperature is controlled at 70-80℃. The digestion product is reacted with brine at a reaction temperature of 50-80℃ to obtain the precursor magnesium hydroxide, which is then calcined at high temperature to obtain the desired product.
1.2 Reagents and instruments
Raw materials: brine (commercially available); dolomite ore.
Reagents: hexadecyltrimethylammonium bromide (CTAB), sodium carbonate, ethylenediaminetetraacetic acid (EDTA), anhydrous ethanol, all of analytical grade. Instruments: electronic analytical balance, 79-3 constant temperature magnetic stirrer, SGM2893HA artificial intelligence resistance furnace (muffle furnace), TGA851e/SF/1100 differential thermal-thermogravimetric analyzer, D-78 X-ray diffractometer, JL-1166 laser particle size analyzer, Hitachi S-4800 scanning electron microscope.
1.3 Preparation of basic raw materials
1.3.1 Dolomite
Crush the dolomite into small pieces with a particle size of about 30 mm, calcine it in a muffle furnace at 950℃ for 1.5h, grind it into dolomite with a particle size of less than 85μm after calcination, seal it to prevent moisture and set it aside.
1.3.2 Refined brine
Add a small amount of 10% hydrogen peroxide solution and dolomite to the brine to convert the heavy metal salt into hydroxide precipitation and remove it, and then you can get refined brine. The obtained brine is titrated with EDTA solution to a magnesium ion concentration of 2.2mol/L. The obtained refined brine is prepared into solutions with magnesium ion concentrations of 0.5, 1.0, 1.5, and 2.0mol/L for use.
1.4 Experimental method
Weigh 10g of dolomite lime, add a small amount of hot water to moisten it, place it on a constant temperature magnetic stirrer, control the temperature at 70-80℃, add hot water at about 90℃ while stirring, react for 20-30min, pour out the upper emulsion, continue to add water to the remaining residue for digestion, repeat 2-3 times, remove the indigestible residue, merge the emulsion, remove the upper clear liquid (i.e. water) after standing, and adjust the mass concentration of dolomite lime emulsion to 100g/L.
According to the ratio of Ca in dolomite to Mg in brine of 1:1, measure brine of different concentrations, add a certain amount of CTAB solution, control the reaction temperature at 40-80℃, and add the prepared dolomite lime emulsion dropwise while stirring, with an addition rate of 2-3mL/min. After the addition is completed, react for about 20min, stand, remove the upper clear liquid (i.e. CaCl2 solution), and the obtained product is a single reaction precipitate.
The mass concentration of the first reaction precipitate was adjusted to 100g/L. An equal amount of brine was added for a second reaction. The reaction conditions were the same as the first reaction to obtain a second reaction precipitate. The second reaction precipitate was filtered and washed several times until 0.5mol/L NaCO3 solution was added to the washed filtrate without precipitation. The obtained precipitate was dried at 110℃ and calcined at 700℃ in a muffle furnace for 90min to obtain nano magnesium oxide powder.
2 Results and Discussion
2.1 Effect of Reaction Temperature on Product Purity
The reaction temperature was controlled at 40, 50, 60, and 70℃. It can be seen that the XRD diffraction peak intensity of magnesium oxide obtained at 60℃ was the highest, and no impurity peak appeared, indicating that the product obtained at this temperature had the highest purity. This is because when the temperature is low, the reaction speed is slow, which is not conducive to the conversion of calcium hydroxide to magnesium hydroxide; when the temperature increases, the solubility of calcium hydroxide decreases, which is not conducive to the formation of magnesium hydroxide, and will increase the degree of agglomeration of nanoparticles. Therefore, 60℃ is selected as the optimal reaction temperature.
2.2 Effect of brine concentration on magnesium oxide particle size
With the increase of brine concentration, the particle size of magnesium oxide tends to decrease first and then increase. In the process of preparing precursors, the concentration of brine has a great influence on the particle size of the precipitate. When the initial concentration of brine is too low, the crystal nucleation rate is slow, which will give the crystal grains sufficient time to grow, and the resulting product particle size is larger; high-concentration brine is more conducive to the dissolution of calcium and improves the purity of the product, but when the concentration is too high, the homogeneous nucleation effect is significant, which will increase the degree of agglomeration of the precipitated particles and make the product particle size too large. The brine concentration selected in the experiment is 1.0 mol/L.
2.3 Effect of surfactant on magnesium oxide particle size
In the preparation of nanoparticles, adding surfactants can effectively solve the agglomeration problem of precursors during preparation and drying. This is because surfactants can be adsorbed on the surface of precursor particles to form a steric barrier layer, reduce direct contact between particles, and make it difficult for particles to agglomerate, thereby achieving the purpose of dispersing precipitated particles. As the amount of CTAB increases, the particle size of magnesium oxide gradually decreases. When the amount of CTAB is greater than 0.3% (mass fraction, the same below), the particle size basically does not change. Therefore, 0.3% is selected as the optimal amount of CTAB.
2.4 TG-DTA analysis of precursors
It can be seen from the DTA curve that the endothermic peak of 0-150℃ is the process of the precursor removing adsorbed water; the endothermic peak of 350-550℃ is the process of the precursor decomposing to generate magnesium oxide and water. The corresponding TG curve also shows that the precursor magnesium hydroxide decomposes faster at 350-550℃, and completely decomposes into magnesium oxide above 650℃, with a mass loss of about 30%. The mass no longer changes after 650℃, indicating that magnesium oxide has been completely crystallized at this time, so the calcination temperature of magnesium oxide should be greater than 650℃. Considering that the particle size of magnesium oxide will grow with the increase of temperature, the calcination temperature should not be too high, so the calcination temperature selected in the experiment is 700℃.
2.5 XRD analysis of magnesium oxide
The product magnesium oxide was characterized by XRD, with a scanning range of 10-80° and a scanning speed of 0.01 (°)/s. It was compared with the standard diffraction card of magnesium oxide (PDF45-0496). The positions and intensities of each diffraction peak were basically consistent, indicating that the product was cubic magnesium oxide with complete crystal shape and high purity.
2.6 SEM analysis of magnesium oxide
The magnesium oxide particles were spherical with an average particle size of about 50nm.
3 Conclusion
A new process for preparing nano magnesium oxide was obtained by adding surfactants using the brine-dolomite method. The effects of reaction temperature, brine concentration, and surfactant dosage on the preparation process of nano magnesium oxide were studied. The experimental results of Hebei Messi Biology Co., Ltd. showed that when the reaction temperature was 60℃, the brine concentration was 1.0mol/L, and the mass fraction of CTAB added was 0.3%, the obtained magnesium oxide had high purity, good dispersibility, and small particle size. This method has low cost, readily available raw materials, simple process, and is environmentally friendly, and has certain reference value for industrial application.