Hebei Messi Biology Co., Ltd. has comprehensively studied the current status of magnesium salts at home and abroad, the production method of magnesium hydroxide, and the many applications of magnesium hydroxide and magnesium oxide in industrial production. Important varieties of magnesium salts are magnesium oxide, magnesium hydroxide, magnesium chloride, magnesium sulfate and magnesium carbonate. The product after magnesium calcination is magnesium oxide, which is an indispensable refractory material for metallurgical industry and other high temperatures. The total output of magnesium oxide in the world is about 9 million tons, of which 27% is produced from brine, a byproduct of seawater salt production; 10% comes from microcrystalline sedimentary magnesite; 63% is made from crystalline magnesite.
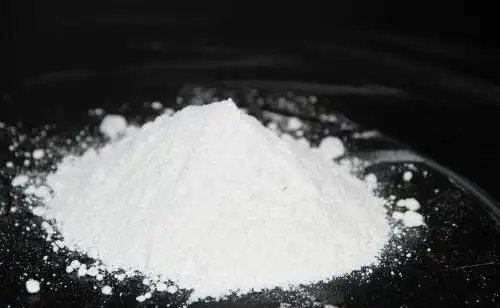
In Western countries, the proportion of brine, a byproduct of seawater salt production, as raw material is even larger, accounting for about 60%; the Soviet Union has now disintegrated, China and other Eastern countries, due to rich mineral resources and good grade, magnesium oxide produced from magnesite accounts for 97% of the total output. However, the use of bischofite ammonia solution to produce magnesium hydroxide and high-purity magnesium oxide is a new process and new technology for the rational use of sea and lake magnesium resources, and an important way to completely solve magnesium harm. It is a “clean” project to rationally utilize the magnesium resources of the sea lake. The sand “ammonialysis” method to produce magnesium hydroxide is not only simple in process flow, but also more suitable for producing magnesium hydroxide by brine ammonialysis from the perspective of my country’s resource situation. The production of magnesium hydroxide by this process not only recovers the salt lake water magnesite, which is toxic, corrosive and causes environmental pollution, but also saves resources.
Hebei Messi Biology Co., Ltd. stated that salt lake brine can produce three products: the first product is magnesium hydroxide, which can be used as a flame retardant for a variety of building materials, and has a large domestic and foreign market; the second product is magnesium oxide, which is made from magnesium hydroxide after satin calcination and is a raw material for manufacturing advanced refractory materials at home and abroad; the third product is ammonium chloride, which can be used as a fertilizer.
Magnesium hydroxide has developed greatly as a flame retardant recently. In addition, it is also used in environmental protection such as acid wastewater treatment, flue gas desulfurization, and heavy metal removal of industrial waste liquid. At present, the sustainable development strategy has become a common goal pursued by countries around the world. Green chemical projects or environmentally friendly projects are more respected by the world. And magnesium hydroxide as an alkali agent can meet these requirements in many aspects. Magnesium hydroxide is calcined at high temperature to produce various and multi-purpose magnesium oxide. Magnesium oxide is also known as magnesia. In nature, magnesium oxide exists in the form of free periclase ore. Magnesium oxide powder is a white loose powder.
The production of natural magnesia began in the late 19th century. Magnesium oxide produced from magnesite mined all over the world. Most of 90% is used for refractory materials. Seawater magnesia has the characteristics of high purity, high density, uniform organization and adjustable composition. It is better than natural magnesia in quality, so it develops very quickly. Magnesium oxide has a wider range of applications. In addition to being well-known as a raw material for advanced refractory materials in the metallurgical industry, it is mainly used to synthesize advanced refractory materials and is widely used in other fields.
Magnesium hydroxide is a chemical product with a wide range of uses, but because magnesium hydroxide is a floc that is difficult to filter and separate, it puts high demands on process operation and equipment selection. Therefore, with regard to the sedimentation of magnesium hydroxide, a single factor study was conducted on the effects of feeding sequence, temperature, reactant concentration, ratio, feeding speed and flocculant on the precipitation of magnesium hydroxide, and the optimal sedimentation conditions were obtained; the filtrate of the reaction was evaporated, and the evaporation residual liquid was salted out with bischofite to produce ammonium chloride, and the remaining solution was dissolved in a certain amount of bischofite and then ammonolyzed to produce magnesium hydroxide, forming a closed circulation system.