Hebei Messi Biology Co., Ltd. stated that the Democratic Republic of the Congo is the country with the largest reserves of cobalt resources in the world, and its production capacity accounts for more than half of the world’s total production. The cobalt resources in the Democratic Republic of the Congo mainly exist in the form of copper-cobalt paragenesis, and a few are separate cobalt ores. The hydrometallurgy of copper-cobalt ore generally adopts the leaching-extraction-electrowinning process to produce cathode copper, and the cobalt-containing raffinate after copper extraction generally adopts the impurity removal-cobalt precipitation process to produce cobalt salts or cobalt compounds. The impurity removal process generally adopts the neutralization hydrolysis precipitation method to remove impurities such as iron ions and manganese ions in the solution. The neutralizing agent generally uses lime or slaked lime. The oxidation impurity removal (iron, manganese, etc.) methods usually include sulfur dioxide and air mixed gas oxidation method, strong oxidant (sodium chlorate, etc.) oxidation method, sodium thiosulfate and air oxidation method, etc. Among them, the strong oxidant oxidation method is prone to cause local high potential and cause the loss of valuable metal cobalt, and sodium thiosulfate will introduce impurity sodium ions into the system. The sulfur dioxide and air mixed gas oxidation method has the advantages of relatively low potential to avoid cobalt loss and no introduction of impurity ions.
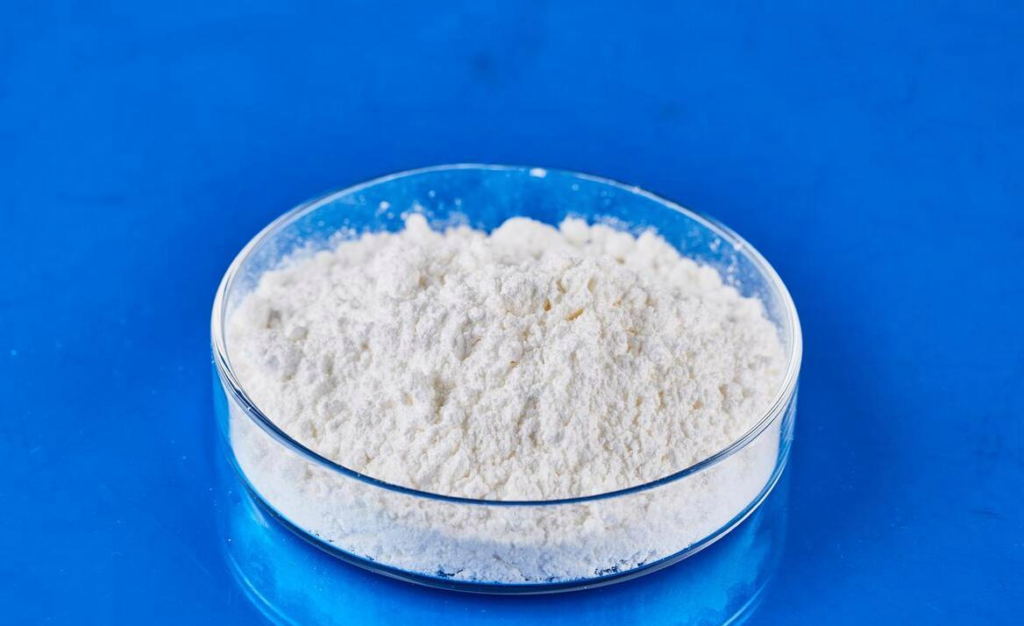
The cobalt precipitation process generally uses a precipitant to separate the cobalt ions from the solution by forming insoluble cobalt salts or cobalt compounds. The precipitants used in the cobalt precipitation process are usually HS, sodium salts, etc. HS is toxic, harmful to human health and easy to cause environmental pollution. Sodium salts such as Na, CO, NaOH, etc. are highly alkaline and easily form a solution with a high pH environment, causing other impurity ions in the solution to precipitate together with cobalt ions, resulting in a lower cobalt grade in the cobalt product and a high level of impurities. In addition, the use of sodium salts will introduce sodium ions into the system that are difficult to handle, and a high concentration of sodium ions will have an adverse effect on production. Activated magnesium oxide has a weak alkalinity, is relatively safe to use, and the wastewater after cobalt precipitation is easier to handle.
This paper provides a new process for removing impurities from cobalt-containing raffinate, cobalt precipitation with magnesium oxide in one stage, cobalt precipitation with slaked lime in two stages, and magnesium precipitation with slaked lime to produce high-grade cobalt hydroxide. The focus is on studying the effect of magnesium oxide addition on the first stage of cobalt precipitation, and organizing trial production according to the whole process. The trial production results show that the selected process is suitable for the production of high-grade cobalt hydroxide. The cobalt grade in the cobalt hydroxide product obtained by the first stage of cobalt precipitation is 32%, the cobalt recovery rate of the whole process is more than 96%, and the wastewater from magnesium precipitation can be returned as production water.
1. Raw materials and auxiliary materials
- 1.1 Raw materials
The cobalt sulfate solution used in production is the cobalt-containing raffinate after stirring, leaching and extraction of a copper-cobalt mine in the Democratic Republic of the Congo.
- 1.2 Main auxiliary materials
Slaked lime: industrial use, -200 mesh>90%, CaO>70%;
Magnesium oxide: industrial use, -325 mesh>99%, MgO>90%;
Sulfur dioxide: acid production flue gas (SO₂ concentration 7.5%).
2. Treatment process
The treatment process mainly consists of impurity removal, first-stage cobalt precipitation, second-stage cobalt precipitation, magnesium precipitation and cobalt hydroxide drying. Impurity removal is to add slaked lime to the cobalt-containing raffinate and introduce a certain proportion of sulfur dioxide and air mixture to oxidize the low-valent iron and manganese ions in the solution into high-valent iron and manganese ions, which are hydrolyzed at a certain pH to form precipitation and separate from the valuable cobalt ions. First-stage cobalt precipitation is to add magnesium oxide to the impurity-removed liquid to make the cobalt ions in the solution enter the precipitation to obtain the cobalt hydroxide product. Second-stage cobalt precipitation is to add slaked lime to the first-stage cobalt precipitation liquid to recover the cobalt ions that have not been completely precipitated, and the second-stage cobalt slag returns to the iron removal and dissolves again into the impurity-removed liquid. Magnesium precipitation is to add slaked lime to the second-stage cobalt precipitation liquid to remove impurities such as magnesium ions in the solution, realize the reuse of magnesium precipitation wastewater, and store magnesium slag separately.