Hebei Messi Biology Co., Ltd. stated that one of the most important ways to obtain magnesium oxide is to calcine magnesium carbonate or magnesium bicarbonate at the appropriate temperature. In industry, the most commonly used material is magnesite, which is a common natural carbonate mineral, but before calcination, the magnesite raw material must undergo appropriate pretreatment.
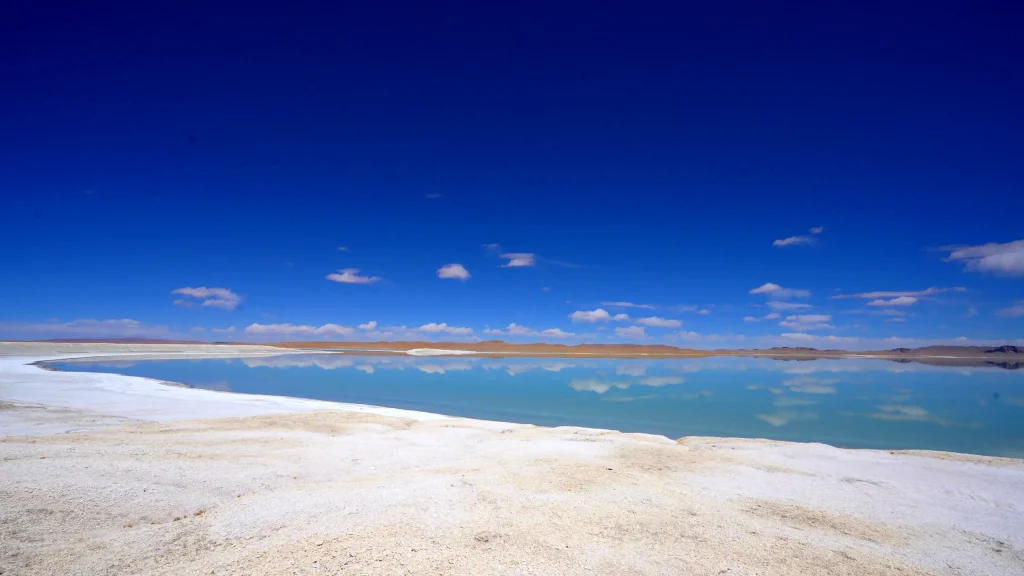
In the first stage, the magnesite is separated from the impure raw material by suspending ferrosilicon (alloy). Because the concentration of ferrosilicon is intermediate, it is intermediate between the lighter dolomite and the heavier magnesite, so the magnesite sinks in the fluid, and the smaller silicate impurities are removed by flotation. , the final particles need to be finely ground.
The calcination process of magnesite involves the decarburization reaction of magnesium carbonate. Physical and chemical test analysis found that the decomposition product of magnesium carbonate (magnesium oxide) has high catalytic activity. The “caustic” magnesium oxide formed directly after thermal decomposition is a material with high specific surface area and strong reactivity. The characteristics of the material obtained after calcination mainly depend on the roasting time and temperature. When the temperature is 450°C, it is obtained The mesopores are the largest, but when the calcination temperature is further increased, the macropores begin to disappear due to crystal growth.
Hebei Messi Biology Co., Ltd. stated that the thermal decomposition process of hydrated magnesium carbonate is not only accompanied by structural changes, but also changes in surface composition and activity. XRD testing showed that the initial material was a mixture of two compounds, MgCO3·Mg(OH)2·3H2O and 4MgCO3·Mg(OH)2·4H2O. Differential thermal analysis (DTA) showed that there were three Obvious endothermic effect: the first one occurs in the temperature range of 25-380°C, accompanied by a 20% mass decrease; the next endothermic effect occurs in the temperature range of 380-490°C, with a mass decrease of 12.0±0.2%, which is due to Magnesium hydroxide undergoes a dehydration process; the exothermic effect at 500°C is related to the formation of magnesium oxide crystals from carbonate roasting; the last of the three thermal effects results in a mass loss of 25.7±0.2%. When the temperature reaches 450°C, the sample is completely decomposed and the surface area increases to 300m2/g; when the heating temperature is higher, the specific surface area decreases rapidly, which may be due to surface sintering.
Hebei Messi Biology Co., Ltd. stated that although the method of synthesizing magnesium oxide by roasting commercial magnesium sources at high temperatures is relatively simple, it is difficult to control the morphology of the product magnesium oxide well.