Hebei Messi Biology Co., Ltd. stated that the production of silicon steel grade magnesium oxide mainly uses seawater brine and minerals as raw materials. When using liquid raw materials for production, alkaline solution is first used as a precipitant to precipitate magnesium, and then further prepare magnesium oxide. my country mainly uses the brine-ammonium carbonate method with basic magnesium carbonate as an intermediate and the brine-ammonia method with magnesium hydroxide as an intermediate. Japan, Israel and other countries mostly use calcium hydroxide as a precipitant. The solid ore method mainly uses the carbonization method of magnesite and dolomite. After digestion, carbonization and other processes, basic magnesium carbonate is used as an intermediate and then calcined to obtain it.
1. Preparation of silicon steel grade magnesium oxide by brine-ammonium carbonate method
Precipitants such as ammonium carbonate and ammonium bicarbonate react with brine in a reactor to generate basic magnesium carbonate intermediates. Silicon steel grade magnesium oxide is obtained through filtering, washing, drying, calcining, heat treatment and other processes. Using industrial magnesium chloride as raw material, basic magnesium carbonate is obtained through precipitation reaction, and then basic magnesium carbonate is calcined at low temperature and gradually heated to prepare magnesium oxide. The product purity is greater than 98%, the average particle size is 3.182μm, the particle size is less than 5um and reaches 71.27%, and the hydration rate is less than 4%, which meets the technical index requirements of silicon steel grade magnesium oxide. Using brine, ammonium bicarbonate and carbonized ammonia water as raw materials, precipitation reaction is carried out in the reactor, and high-activity magnesium oxide is first obtained by calcination, and magnesium hydroxide is obtained by hydration under certain conditions. Then, it is dried and calcined to obtain silicon steel grade magnesium oxide, with a magnesium oxide content of more than 98%, and the hydration rate and coating properties meet the requirements of silicon steel sheet production. In addition, the product has a high viscosity, which solves the problem that the low viscosity of traditional silicon steel grade magnesium oxide cannot meet the production requirements of some silicon steel sheet plants for magnesium oxide viscosity of more than 80mPa·s. Using brine and ammonium carbonate as raw materials, the intermediate basic magnesium carbonate is generated through brine purification and precipitation reaction. After aging, filtration and calcination, silicon steel grade magnesium oxide is obtained. The product has high chemical purity (>99.1%), small average particle size and high viscosity, good coating and adhesion, etc.
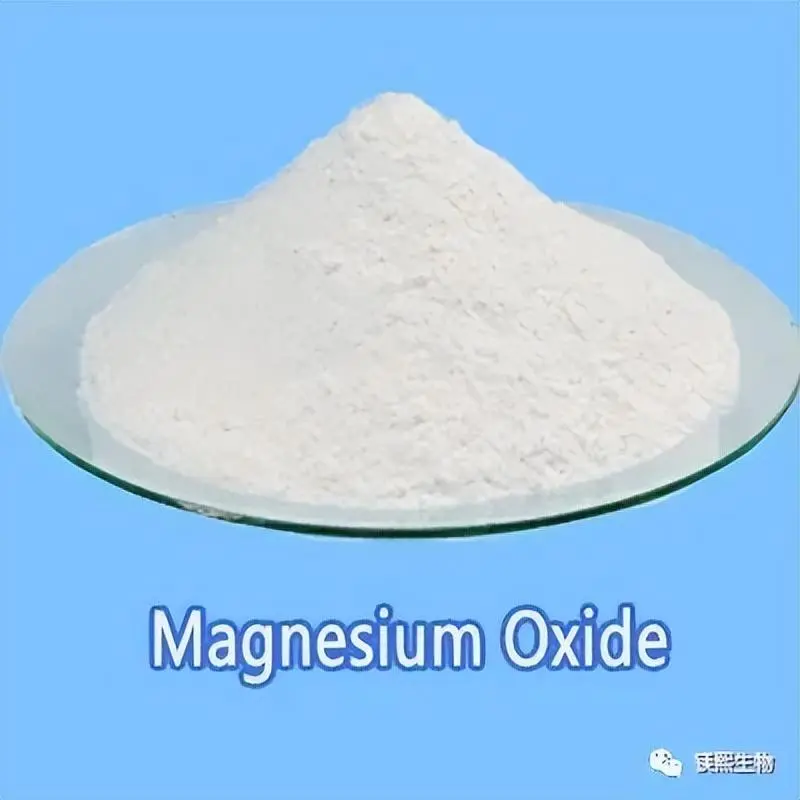
The production process of silicon steel grade magnesium oxide is relatively mature, the product quality is stable and reliable, and industrial production has been realized. The disadvantage is that when preparing basic magnesium carbonate, the by-product ammonium chloride is difficult to recover due to the low concentration of the reaction system, which is easy to cause environmental pollution. Although the ammonium chloride in the mother liquor can be recovered by evaporation, the concentration of ammonium chloride is too low, the energy consumption is too high, and the process is complicated and difficult to control. Moreover, for every ton of product produced, the consumption of ammonium bicarbonate is as high as 6~7t, the electricity consumption is 1000kWh, and the coal consumption is 8~9t, which is costly.
2. Preparation of silicon steel grade magnesium oxide by brine-ammonia method
The process of continuous reaction of brine and ammonia water is adopted. By adjusting the reaction time, the crystal particle size of magnesium hydroxide is controlled to be 0.2~2.0μm, and magnesium hydroxide is dynamically calcined at 800~900℃ for 30~60min to obtain silicon steel grade magnesium oxide. Brine with a magnesium chloride concentration of 4.3mol/L and ammonia water with a pH value of 13.5 are used as raw materials. The pH value of the reaction system is controlled to 11 to obtain a magnesium hydroxide intermediate, which is calcined at 950℃ in a box-type resistance furnace and cooled under closed conditions. Add ethanol, crush with a ball mill, and finally sieve to obtain silicon steel grade magnesium oxide. The product is irregularly spherical under an electron microscope, with a flaky appearance and a relatively uniform particle size. The average particle size of the ground magnesium oxide is 5μm, which is basically normally distributed. The product purity is >98%, and the hydration rate is 3.5%, which meets the requirements of silicon steel grade magnesium oxide.
The advantages of the brine-ammonia method are low equipment requirements, wide sources of raw materials, and large or small scale. Its disadvantages are that the intermediate magnesium hydroxide obtained with ammonia water as raw material has a small particle size and is difficult to settle and filter. When the ammonia concentration is high, the viscosity of magnesium hydroxide is large and it is difficult to separate; when the ammonia concentration is low, the utilization rate of magnesium is low. At the same time, there are environmental problems such as the volatilization of ammonia leading to poor operating environment and difficult treatment of by-product mother liquor.
3. Preparation of silicon steel grade magnesium oxide by magnesium ore carbonization method
Using dolomite as raw material, calcining in a high-temperature resistance furnace to generate dolomite lime, after digestion, purification, carbonization, pyrolysis, obtain basic magnesium carbonate intermediate, and then aging, washing, drying, calcining, obtain magnesium oxide, crushing, screening, obtain silicon steel grade magnesium oxide, the product purity is 98.93%, the hydration rate is 3.2%, the particle size (5μm)>82%, and all indicators are better than the enterprise standard. Magnesite is used as raw material, calcined in a high-temperature resistance furnace to generate light-burned powder, and then digested to make magnesium hydroxide emulsion. After carbonization, basic magnesium carbonate intermediate is obtained, and silicon steel-grade magnesium oxide that meets enterprise standards is prepared by high-temperature calcination. Studies have shown that the appropriate concentration of magnesium oxide in light-burned powder emulsion is 15~20g/L, and the pH value of carbonization endpoint is 7.0~7.1. The decomposition temperature of heavy magnesium water is controlled within 80~90℃, and the average particle size of the product can be controlled within 5~6um; the calcination temperature is controlled at about 950℃, and cooling under air-tight conditions can obtain the activity and hydration rate required by silicon steel-grade magnesium oxide.
The preparation of silicon steel-grade magnesium oxide by magnesium ore carbonization method has the disadvantages of long reaction cycle, complex process, high production cost, etc. At the same time, affected by impurities in the raw materials, the product purity is low.