Hebei Messi Biology Co., Ltd. stated that nano magnesium oxide refers to materials with at least one dimension less than 100nm in space. Based on the excellent performance of nanomaterials, nano magnesium oxide has attracted much attention because it combines the performance of magnesium oxide and the characteristics of nanomaterials in terms of light, heat, magnetism, etc. At present, since the industrial production of magnesium oxide in my country is mainly prepared by roasting ore resources such as magnesia, the quality of magnesium oxide is greatly affected by the quality of the ore, which is not conducive to the preparation of high-purity magnesium oxide.
my country is rich in dolomite resources. At present, many processes and methods for preparing magnesium oxide have been applied to industrial production. The use of dolomite to produce nano magnesium oxide products with higher added value can effectively reduce the production cost of products and realize the effective utilization of my country’s mineral resources.
At present, the preparation of nano magnesium oxide from dolomite is rarely industrialized because there are two problems that need to be solved, namely, dolomite calcium and magnesium separation and agglomeration.
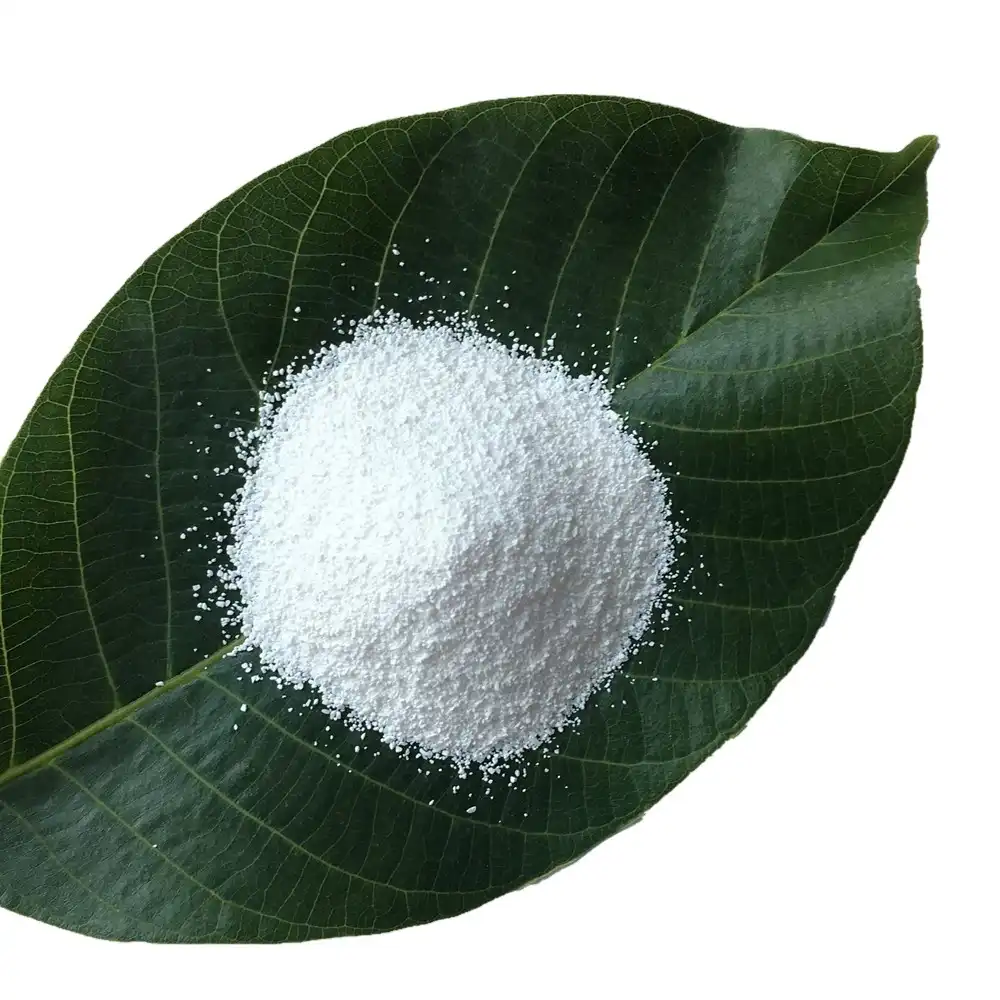
Dolomite calcium and magnesium separation
Dolomite deposits are important calcium and magnesium resources. The key issue in practical applications is how to successfully separate calcium and magnesium in dolomite to prepare pure magnesium products or calcium products. At present, the commonly used separation methods for calcium and magnesium in dolomite include three types: acid hydrolysis, carbonization and ammonium leaching.
1. Acid hydrolysis
The acid hydrolysis method is to use an acid hydrolyzer to dissolve dolomite to obtain the corresponding magnesium salt and calcium salt. The commonly used acid hydrolyzers in this method are hydrochloric acid and sulfuric acid.
The use of different acid hydrolyzer processes has its own advantages and disadvantages. Using hydrochloric acid as an acid hydrolyzer, magnesium compounds and calcium compounds can be produced at the same time, with high raw material utilization, but the production steps are more complicated; while using sulfuric acid as an acid hydrolyzer is generally only used to produce magnesium compounds, and its production process is relatively simpler, and calcium and magnesium ions can be separated in one step.
The acid hydrolysis method uses acid to directly dissolve dolomite. This method does not require calcination of dolomite, has low requirements for equipment, and has high production efficiency and fast reaction speed. Most importantly, the calcium and magnesium separation degree is very high, so the prepared calcium and magnesium products have high purity. However, the disadvantage of the acid hydrolysis method is that the acid consumption during the reaction is large, which greatly increases the production cost and is not suitable for industrial production.
2. Carbonization method
Carbonization is also a common method for separating calcium and magnesium from dolomite. Its basic process flow is as follows:
(1) Calcination: Dolomite is calcined under high temperature conditions to produce calcium oxide and magnesium oxide powders;
(2) Digestion: After adding water to the above powders for digestion and removing the residue, refined calcium hydroxide and magnesium hydroxide slurry can be obtained;
(3) Carbonization: The slurry is carbonized with carbon dioxide gas in a carbonization tower. Calcium hydroxide is carbonized to produce calcium carbonate precipitation, and magnesium hydroxide is carbonized to form soluble magnesium salt magnesium bicarbonate and become a clear liquid;
(4) Pyrolysis: Magnesium bicarbonate can be calcined to produce light magnesium carbonate, and magnesium carbonate can be calcined to prepare magnesium oxide.
Carbonization is the most commonly used method in domestic industrial production at present, but the process has strict requirements on equipment and is relatively complicated to operate, so it is not suitable for laboratory research.
3. Ammonium leaching method
Ammonium leaching uses calcined dolomite as raw material and ammonium salt as leaching agent to leach calcium and magnesium. The basic principle of this method is that the ammonium salt solution is acidic and can react with the digested calcined dolomite under heating conditions to generate soluble magnesium salt and calcium salt, or soluble magnesium salt and insoluble calcium salt. The former can be separated from calcium and magnesium by adding alkaline substances to adjust the pH value of the solution so that the magnesium salt is converted into magnesium hydroxide or magnesium carbonate precipitation, while the latter can be successfully separated from calcium and magnesium by direct filtration.
Relatively speaking, the ammonium leaching method has mild reaction conditions, simple operation, low production cost, and high leaching rate of calcium and magnesium, which can more effectively separate calcium and magnesium.
Agglomeration phenomenon of nano magnesium oxide
Nano materials are widely used because they have special properties such as small size effect, macroscopic quantum tunneling effect, and surface effect that many traditional materials do not have. However, nano materials have a large specific surface area, high activity, and are extremely unstable. They are extremely easy to agglomerate and lose their original properties, which reduces the value of the material and causes certain difficulties in the preparation and storage of nano materials. Therefore, the agglomeration problem of nano materials is a key technical problem that restricts the development of nano materials.
The agglomeration of nano materials is divided into soft agglomeration and hard agglomeration. Soft agglomeration is caused by intermolecular interaction and van der Waals force, which is relatively easy to remove. There are currently five viewpoints on the formation of hard agglomeration: capillary adsorption theory, hydrogen bond theory, crystal bridge theory, chemical bond theory, and surface atomic diffusion bonding mechanism. However, there is no unified explanation so far.
There have been a lot of studies on the anti-agglomeration technology of nano-magnesium oxide, mainly physical dispersion method and chemical dispersion method.
Physical dispersion is to improve the uniform agglomeration of nanoparticles through physical methods such as mechanical stirring and ultrasonic action.
Chemical dispersion is a method to reduce the attraction between nanoparticles through surface modification, improve the surface electrical properties, functional groups, adsorption properties of nanoparticles, improve the dispersion of nanoparticles, and improve the agglomeration phenomenon. It can be divided into the following two categories:
1. Surface chemical repair
(1) The coupling agent method is to use the coupling agent to treat the surface of nanoparticles with both inorganic and organic groups. It can not only improve the dispersibility of nanopowders and effectively improve the agglomeration phenomenon, but also improve the compatibility of nanoparticles in other organic materials. (2) Esterification reaction refers to the reaction between metal oxide and alcohol, which changes the hydrophilic property of the surface of metal oxide nanoparticles into hydrophobic property, reduces the surface charge of nanoparticles, and improves the dispersibility of nanoparticles.
(3) Surface grafting modification is also a common surface modification method. The monomer is used to polymerize on the surface of inorganic nanoparticles under the action of initiator, and finally forms a coating layer on the surface of nanoparticles, or the monomer is grafted with inorganic nanoparticles at the same time of polymerization, which increases the repulsion between nanoparticles and effectively improves the agglomeration problem of nanoparticles.
2. Dispersant dispersion
Dispersant dispersion is widely used in wet chemical methods. By adding dispersants, the surface charge distribution of nanoparticles is changed, and the dispersion effect is achieved through three mechanisms: electrostatic stabilization mechanism, steric stabilization mechanism, and electrosteric steric stabilization mechanism.
(1) Electrostatic stabilization mechanism.
By adding dispersants, a double electron layer is formed at the contact surface between nanoparticles and polar solution, which increases the electrostatic repulsion between particles, thereby achieving the purpose of preventing agglomeration;
(2) Steric stabilization mechanism. The dispersant molecules are adsorbed and wrapped around the nanoparticles to form a protective layer, which increases the distance between the nanoparticles and reduces the intermolecular forces, so that the nanoparticles can be evenly dispersed;
(3) Electrosteric barrier stabilization mechanism.
If the added dispersant is a polyelectrolyte, under certain circumstances, it can simultaneously exert the electrostatic stabilization mechanism and steric barrier effect to achieve a dual stabilization effect.
Hydrothermal treatment is a typical dispersant dispersion treatment method. In addition to using pure water as a solvent, mineralizers, surfactants, etc. are often added to assist hydrothermal treatment. By changing the hydrothermal temperature, hydrothermal time, hydrothermal medium, surfactants, etc., the crystal growth rate and growth orientation are controlled, thereby achieving the purpose of changing the product morphology, particle size, and dispersibility.
With the progress of society and the development of science and technology, people pay more and more attention to the effective development and utilization of mineral resources, and the demand for high-strength, high-temperature resistant, multifunctional and high-value-added composite materials is increasing. The preparation of nano magnesium oxide materials with uniform particle size and high dispersibility using dolomite as raw material will receive more and more attention.