Hebei Messi Biology Co., Ltd. stated that a metallurgical precipitation-grade active magnesium oxide for cobalt extraction and its preparation method and application, the active magnesium oxide prepared by this method has high purity and activity, and low calcium content and chlorine content. In addition, the tail water in the present invention is not discharged, and the magnesium oxide lost in the tail water is recovered, comprising the following steps:
This method mixes magnesium oxide, magnesium chloride and water, and then conducts a hydrothermal reaction to obtain magnesium hydroxide precipitate and calcium chloride solution; immerses the magnesium hydroxide precipitate in an ammonium chloride aqueous solution for leaching to obtain a magnesium chloride solution, ammonia gas and leached residue; mixes the magnesium chloride solution, ammonia gas and carbon dioxide for magnesium precipitation reaction to obtain a basic magnesium carbonate precipitate; the basic magnesium carbonate precipitate is dried and calcined in turn to obtain active magnesium oxide. The magnesium oxide prepared by this method has high activity. However, due to the high content of calcium impurities in the magnesium oxide prepared by this method, the purity and activity of the magnesium oxide are affected. At the same time, the application did not pay attention to the treatment of the tail water of magnesium oxide hydration. In addition to the calcium chloride produced in the decalcification process, the tail water also contains unreacted magnesium chloride (accounting for 4-70% of the total feed). In addition to causing pollution, the tail water discharged into the environment will also cause a large amount of useful components to be lost.
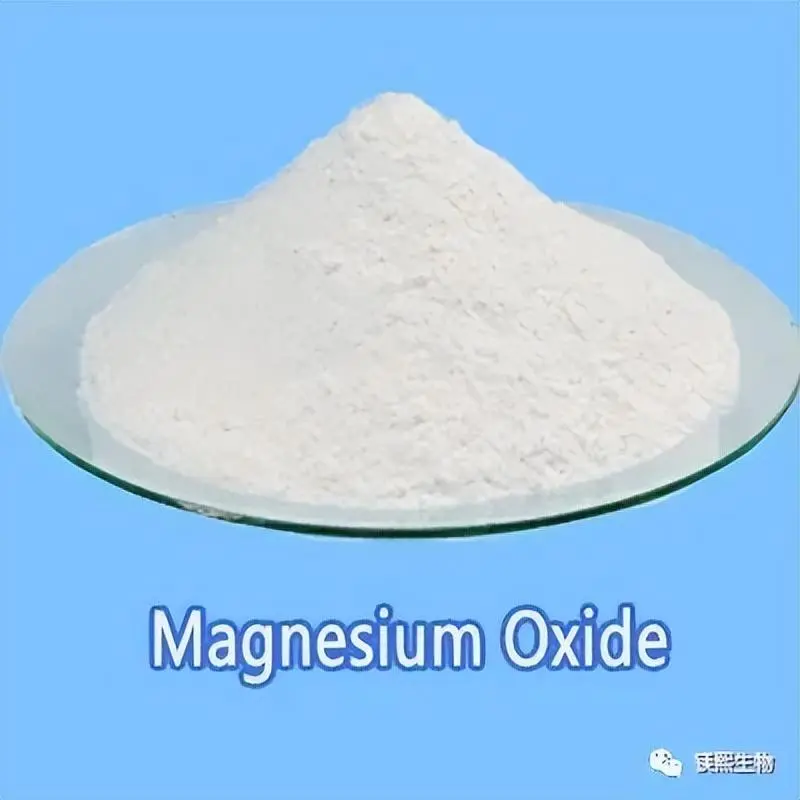
1) Crushing and calcining of magnesite: 40-240mm sized ore is burned into 0-7mm granular magnesium oxide powder through a mechanical vertical kiln, and the magnesium oxide powder is mechanically finely ground into granular materials with a particle size of 200-325 mesh; or the original ore is crushed into 200 mesh particles and fed into a flash suspension calcining furnace to be burned into 200-325 mesh magnesium oxide powder;
2) Hydration reaction decalcification process: Add the ground magnesium oxide powder into the reactor, and add a quantitative magnesium chloride solution in proportion, start stirring, and while stirring Steam is input into the tank at the same time, and the temperature in the kettle is maintained at 60-90℃ and stirred for more than 1.5-3 hours to complete the reaction;
3) Deslagging: The ore liquid after the reaction is pumped into the cyclone separator to separate the larger particle size materials and remove impurities;
4) Filter pressing process: After separation by the cyclone separator, the upper cyclone liquid (fine material) is directly pumped into the plate and frame filter press for solid-liquid separation and filtration. The separated filter cake is put into the stirring kettle again, and clean water is added for secondary stirring, beating and washing to remove chloride ions.
5) Magnesium hydroxide filter pressing: The fine material after secondary beating and washing is pumped into the plate and frame filter press again for solid-liquid separation and filtration, and the finished filter cake is sent to the pre-drying equipment through a conveyor belt for drying.
6) The magnesium hydroxide powder is calcined into magnesium oxide using a flash suspension calcining furnace; and the magnesium oxide powder is then divided into three parts according to the particle range using a particle classifier: coarse particles, intermediate particles and fine particles. The intermediate particle magnesium oxide product is finely ground by mechanical fine grinding or ball milling into a fine particle size, and is collectively called a precipitated grade magnesium oxide product with the classified fine particles. It can be sent to users for use after sealed compression packaging.
The decalcification reaction of the filtrate containing calcium chloride after solid-liquid separation in step 4 is specifically as follows: measure the CA content in the filtrate obtained in step 4), add an excess of magnesium hydroxide slag at 30-50°C, introduce CO2 gas into a sealed container, carbonize to the end point, react magnesium carbonate with CaCl2 in the leaching solution to generate magnesium chloride and calcium carbonate, filter out calcium carbonate, and obtain a pure magnesium chloride aqueous solution. After the filtrate in the decalcification stirring tank is settled and clarified, solid-liquid separation is performed, the solid is calcium carbonate, and the liquid is magnesium chloride solution, which is prepared for use in the reaction of step 3;
After the solid-liquid separation in step 5), the filtrate is subjected to water treatment and reverse osmosis, and the clear water returns to step 5 as dechlorination water; the concentrated water returns to the decalcification device to participate in the decalcification reaction.
The step 2) in which the magnesium chloride solution returns is used as the added magnesium chloride solution.
Step 5) After solid-liquid separation, the filtrate is treated with water and reverse osmosis, and the clean water returns to step 5) for rinsing; the concentrated water returns to the decalcification device to participate in the decalcification reaction.