Tibet Mag stated that the influence of the apparent specific volume and addition amount of porous magnesium oxide on the performance of thermal batteries was systematically studied by the method of centrifugal acceleration. The research found that the apparent specific volume of magnesium oxide has no effect on the static discharge performance at room temperature. However, under high-temperature acceleration, when the apparent specific volume of MgO is lower than 8 mL/g, the safety performance of the battery is poor. The optimal mass fraction of MgO in the thermal battery separator is 40%, and the internal resistance is 50-100 m W. For the first time, the microstructure and surface morphology of magnesium oxide were comprehensively characterized by X-ray diffraction (XRD), scanning electron microscope (SEM) and other methods, which strongly proved the process mechanism of magnesium oxide using the porous structure to adsorb electrolyte, and determined the thermal battery. The selection method of porous magnesium oxide.
The main electrolyte of the thermal battery is a solid salt. In actual use, it will leak due to state changes, which will not only pollute the environment, but also cause other adverse effects. Therefore, a certain proportion of binder should be added to the electrolyte of the battery, so as to achieve the purpose of changing the state and control its flow. In order to better improve the inhibitory effect on lava flow, porous magnesium oxide fibers should be added, so that the performance of the thermal battery is also improved, thus realizing the joint application of physics and chemistry to solve the problem. However, magnesium oxide still has some drawbacks. After the adsorption material is formed, it is not only beneficial to the recycling of the material, but also reduces the loss of the material. Can operate on a fixed bed. Therefore, it is of great practical value to study the adsorption and formation of MgO.
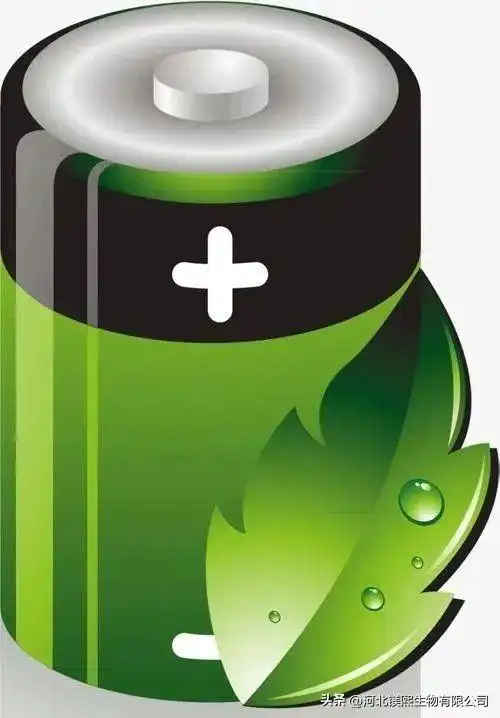
Tibet Mag stated that in nature, magnesium oxide-based adsorption materials are not only easy to obtain, but also cheap. The performance of this film-forming material is obviously better than that of particle form materials, and it can quickly complete the adsorption in actual use, and is not prone to clogging problems. This material can be used on a fixed bed because of its unique film-forming characteristics. The two molding methods compared above have simple processes, can be selected according to actual production, and can effectively reduce costs. In actual production, they have very good prospects and values. If it is to be applied in other fields, a preliminary inspection should be carried out to analyze whether this adsorption principle is applicable to all pollutants, so as to make a more accurate selection.